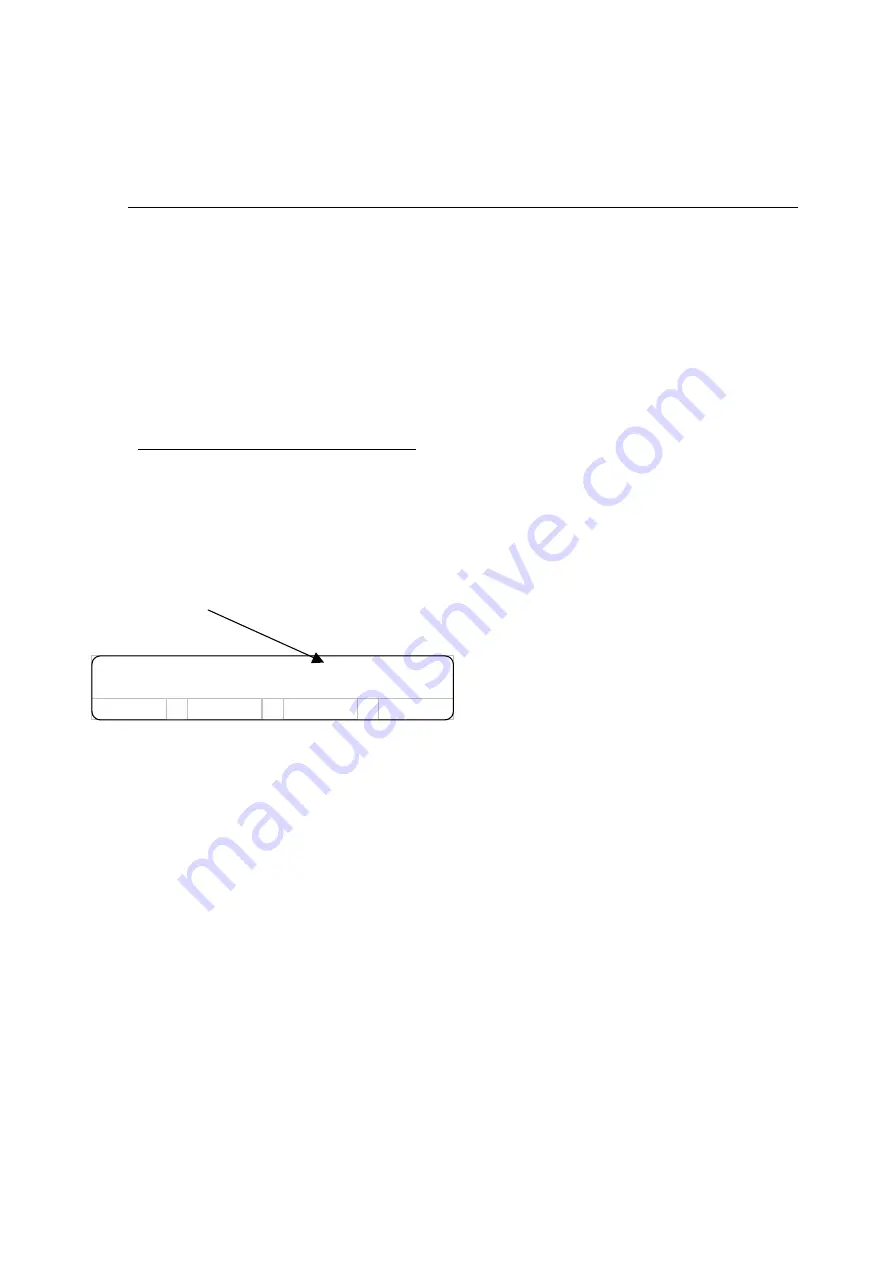
©2004 AUGIER SA.
I-21
I.5.3.3 “Overcurrent”:
Overcurrent protection is activated if the output current goes above a defined value for a defined period.
There are three adjustable Overcurrent levels:
Setting current levels I>> Level 1, I>> Level 2, I>> Level 3, Duration IL1, Duration IL 2, Duration IL 3 :
Go into the menu “Alarms and Warnings” then “Overcurrent”.
There is a fourth level, which is not adjustable : The fault “Peak Overcurrent!” occurs if the output current
goes instantly above twice the nominal peak current (see IEC definition).
An Overcurrent fault can be automatically cancelled according to the value of the “Restarts number”
parameter.
As each fault occurs, the number of faults is incremented. If the number of faults is greater than or equal to
“Restarts number” in a period of less than 10s the fault is activated. The number of faults is reset to 0 after 10s
without fault.
If the programmed number of restarts is reached without control of the current, the CCR stops instantly,
and the display shows which level has been reached.
Setting the “Restarts number” parameter :
Go into the menu “Alarms and Warnings” then “Overcurrent”.
I.5.3.4 Cancelling “Open circuit” and “Overcurrent” faults:
Faults are memorised during a mains power loss :
Alarm message
to cancel any faults, press reset , when CCR is energised in the stop mode.
I.5.4 AUTOMATIC
OPERATION:
The operation of the device is programmed into the software. In local mode, the brightness selected
from the keyboard is activated, in remote control mode the highest priority is given to multiwire remote control
(control terminal block), then to the JBUS link or other present communication interface
When a brightness level is activated, the motherboard turns on the main contactor and controls the
thyristors optically in order to have an output current according to the desired setting.
It continually compares the loop current measurement coming from the measuring board (which uses a
HALL effect sensor) and the requested setting, and then applies the error obtained to a digital regulator which
synthesises thyristor control impulses and transmits them, via two fibre optic cables, to the thyristor interface
board.
The phase control for the thyristors is therefore constantly adjusted so that the true RMS current in the
loop corresponds to the required setting with an accuracy better than 1%.
L
See paragraph I.3.1 for block diagrams of the system.
ALARM: I<<Open Cir.
reset