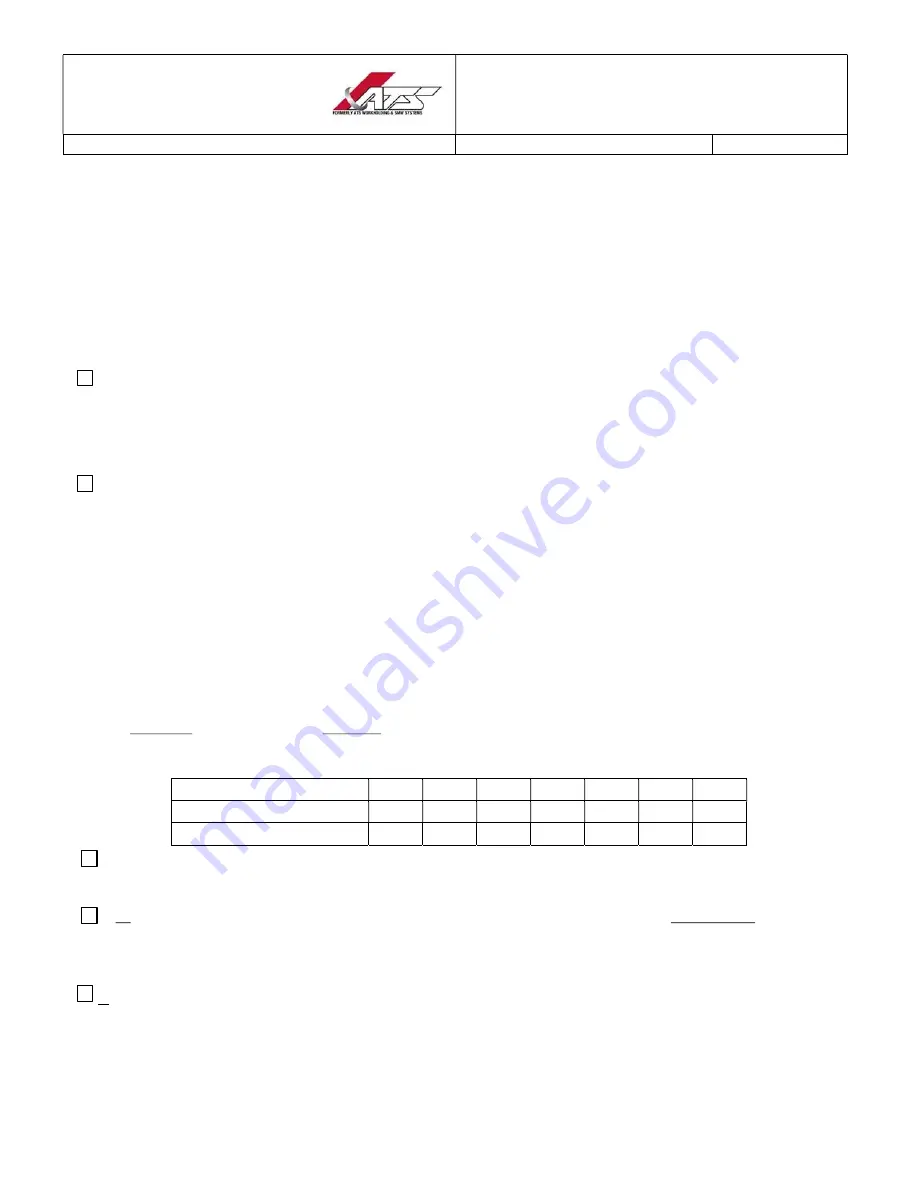
Effective Date: 09/25/08
Page 2 of 9
ATS Systems
Form
Subject: Ultimate Chuck Install & Training Checklist
Doc. No. FM 9-112
Rev.C
Ultimate Chuck UC2 Installation and Customer Training Checklist
Note: All items with signature box must be initialed by ATS Systems Service Engineer.
General
Inventory Checklist - ATS supplied items
(See BOM for details of this specific order)
:
___
Chuck
___
manual
___
maintenance decal
___
Drawtube adapter
___
grease gun & grease
___
Jaw change wrench
___
Wrench-drawtube
___
bolts- chuck to spindle
Key Checks
Before Proceeding:
___
Get list of people to train and name of management contact to advise of any safety or other issues.
___
Check that lathe spindle nose is the same as the chuck provided.
Machine top speed is lower then rated speed of chuck, or soft limit is set.
___
Are top jaws available for first job? Check jaw fit on base jaws. ___
Is material available for first job?
Installation Steps:
Manual section 3
Attach safety/maintenance decal to lathe.
___
Remove existing chuck. Actuate the chuck and hit the e-stop in mid-stroke. This will cause an alarm and
shutoff the machine hydraulics for easy removal of chuck. Clean spindle nose and flange, remove defects
with a stone.
___
Make sure the drawtube is screwed in tight to the cylinder.
___
Screw the drawtube adapter all the way on to the drawtube to inspect proper threads. Retract the drawtube
to ensure the drawtube adapter will fit into the bore of the spindle.
___
Measure the length from the spindle flange face to the end of the drawtube. It must be shorter than the
respective dimension in the back of the chuck. Check with drawtube in forward position, chuck piston in
the forward open position.
___
Measure actual drawtube stroke and record. ________
For reference: * Below, minimum drawtube stroke to use hard jaws and avoid need for ½ pitch base jaws
assuming drawtube length is perfectly adjusted. You would like to have more stroke than this to allow for
some drawtube length adjustment tolerance. Explain this to the customer if it's close.
UC2 Model
180
215
260
315
400
500
630
Full piston stroke
.82
.94
1.10
1.10
1.18
1.38
1.57
Min. stroke for hard jaws*
.73
.72
.85
.85
.85
1.1
1.1
Complete and attach to the machine the “Chuck and Cylinder Specifications” decal with all engineering data
and fill in all data on the copy on pg. 8 of this checklist. You’ll need to get cylinder and lathe hydraulic specs
off the machine or in the machine manuals. Call Santa Fe Springs for help.
If drawtube stroke is less than "Min stroke for hard jaws" shown above, advise user management (in addition
to training the shop staff) they will need half pitch base jaws for hard jaw applications and to take care that
they are always gripping in the first part of the jaw stroke. If stroke is longer but close, advise them to
regularly check drawtube adjustment and jaw stroke. Measure and record actual jaw stroke below.
If available machine pressure and resulting drawbar pull exceeds chuck limit, advise user management not
to exceed limit. Suggest customer obliterate pressure information on lathe builder decals that apply to other
chucks to avoid confusion.
Summary of Contents for ULTIMATE CHUCK UC2
Page 12: ......
Page 13: ......
Page 15: ......
Page 25: ......
Page 26: ...ATS Systems Formerly SMW Systems Ultimate Chuck UC2 Spare Parts List 3 16 2007 Page 1 of 19...