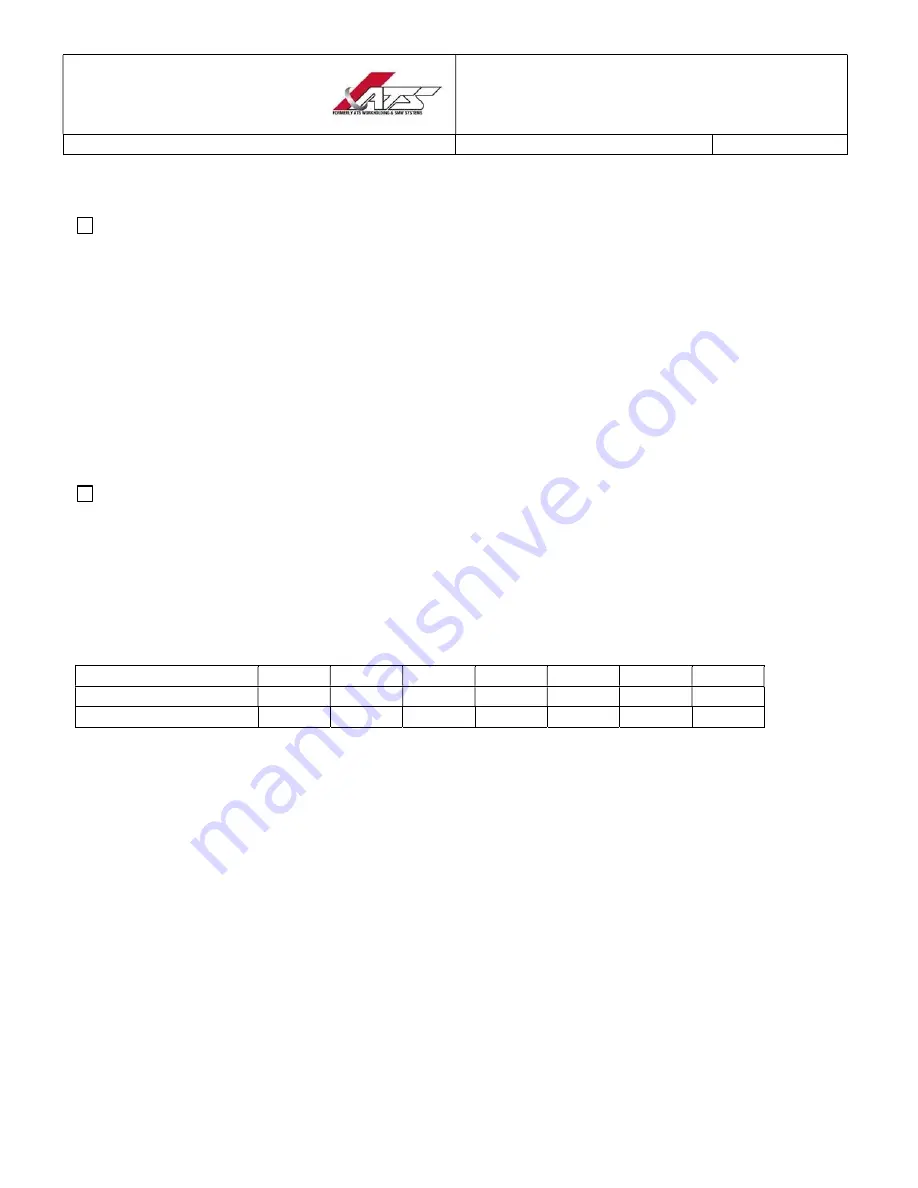
Effective Date: 09/25/08
Page 3 of 9
ATS Systems
Form
Subject: Ultimate Chuck Install & Training Checklist
Doc. No. FM 9-112
Rev.C
___
Check runout of spindle nose taper and flange. Max allowable .0002” TIR. Actual_______"TIR.
___
Check drive button counterbore depth and make sure it is deeper than spindle drive button.
___
Inspect UC2 chuck. Clean mating surfaces. Stone to remove any imperfections.
Check that mounting bolts are correct length to provide minimum 1.5x diameter engagement and are grade
12.9 if metric, grade 8 if inch.
Note: Some spindle flanges have thru tapped holes and bolts too long could
damage seals or bearings.
___
Place a light film of KO5 grease on drawtube adapter end and insert into chuck. Locktite drawtube adapter
lockring into chuck using service removable (blue) Locktite. Adapter must turn freely in chuck without any
restrictions and have no vertical movement of any kind.
___
With the drawtube fully retracted and the chuck piston forward mount the chuck to the spindle and tighten
the bolts. Screw the chuck adapter fully onto the drawtube with the wrench provided. With the chuck in the
open position unscrew the adapter until it will not rotate. The chuck should now be mounted and the
drawtube length correct for jaw stroke and jaw change.
___
Check operation of drawtube and jaw change. If necessary, adjust drawtube adapter a half turn at a time
until cam bolts turn with hex key and jaw stroke is to spec. If this is not set correctly, jaw change will be
difficult. See manual 3.1.2
Measure actual jaw stroke and record. ______”. Confirm it is either full stroke or proportional to short
stroking cylinder noted above.
___
Inspect chuck concentricity on the OD indicating surface, and face runout.
Record actual runouts: OD__________TIR; Face___________TIR
___
Using the dynamic grip force gauge, inspect the grip force at either the maximum available hydraulic
pressure, or the maximum allowable pressure for this cylinder that yields the maximum allowable drawbar
pull. (Refer to the “Chuck and Cylinder Specifications” decal you completed.) Compare your gauge
reading to a calculated grip force.
Chuck model/size
180
215
260
315
400
500
630
Max. drawbar pull – lb.
7,400
11,915
16,400
22,480
29,890
29,890
29,890
Max. total grip force- lb
13,480
22,480
30,300
40,460
53,950
53,950
53,950
Later, demonstrate gauge during training session and recommend purchase of gauge.
Training Checklist:
Customer Employees Trained Include:
________________________ ____`____________________ _________________________
________________________ ________________________ _________________________
Summary of Contents for ULTIMATE CHUCK UC2
Page 12: ......
Page 13: ......
Page 15: ......
Page 25: ......
Page 26: ...ATS Systems Formerly SMW Systems Ultimate Chuck UC2 Spare Parts List 3 16 2007 Page 1 of 19...