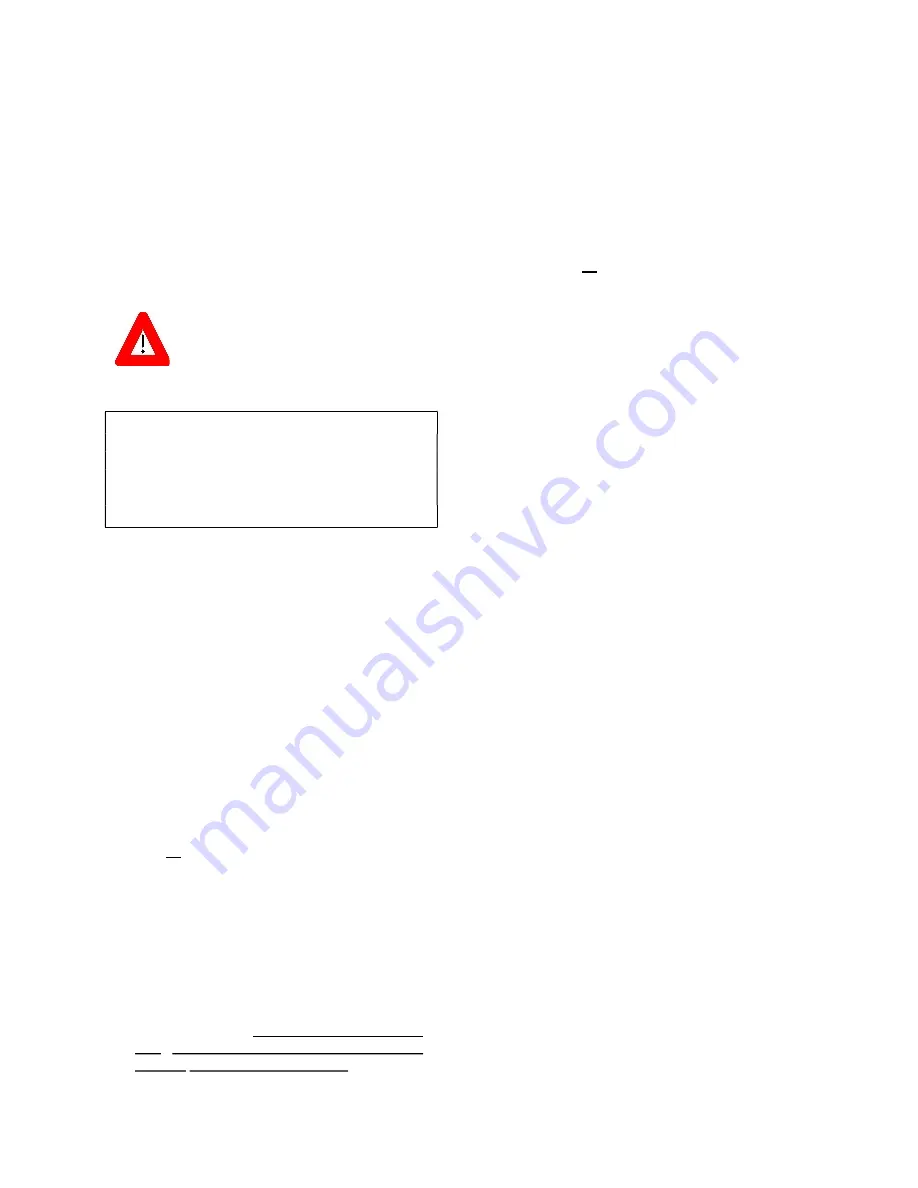
ATS Systems Ultimate Chuck Installation and Operations Manual
calculated to establish parameters for actual
testing with a dynamic grip force gage. See this
manual section 4.6)
Jaws should never
be positioned to extend beyond the outside
diameter of the chuck more then the standard
amount as described for the standard base
jaws in the ATS technical specifications.
1.3.4 Chuck Rotational Speed (RPM)
WARNING
If the maximum speed of the lathe is greater than the
maximum recommended speed of the chuck and/or
the clamping cylinder, the machine must be equipped
with a speed limiting device.
The centrifugal force acting on the clamping jaws
must be considered when determining the required
clamping force to machine a workpiece. See
section 1.3.3 above and section 4.6.
1.3.5 Maintenance Instructions
The reliability of the chuck can only be guaranteed
if the maintenance requirements in these operating
instructions are followed exactly. In particular,
attention must be paid to:
•
Lubrication: Only ATS K05 grease (Part
#11139101) should be used. (Unsuitable
lubricants can reduce the clamping force by
more than 50%). The chuck should be greased
each
24
hours of
operation under normal conditions. (See 5.2.3)
•
All surfaces that require lubrication must be
reached. (The close fits of mating parts require
a high injecting pressure. For this reason a high
pressure grease gun should be used).
Important:
Grease must be injected into the
three fittings on the face of the chuck when the
chuck jaws are fully opened (jaws outward
from centerline).
It is only in this position
that lubrication will properly reach the
internal components of the chuck.
•
To ensure good grease distribution, inject one
shot of grease into each of the three grease
fittings, actuate the chuck full stroke several
times, and then inject a second shot of grease
into each of the three fittings. Check the
clamping force with a grip force gauge.
•
After each
50
clamping strokes it is advisable
to actuate the chuck several times without
gripping a workpiece so that the chuck is
stroked to its extreme limits. When this is
done, lubricant that has been displaced is
returned to the pressure surfaces and the
clamping force is retained for a longer period
of time without re-lubrication.
•
Depending on the application and the
workpiece materials being machined, the chuck
will periodically need to be disassembled and
cleaned. After cleaning, all internal parts must
be coated with a film of KO5 grease, and the
chuck body cavities at either end of the wedge
bars filled 50% with KO5 grease. Each time
the chuck is actuated and the wedge bars
stroke, this “reservoir” of grease is pumped
back through ports in the wedge bar to lubricate
critical surfaces.
•
Ultimate Chucks were designed primarily for
JIT applications with frequent jaw changeover.
No grease fitting ports lubricate the jaw guide
ways. Whenever jaws are changed, inspect the
chuck guide ways for cleanliness and put a film
of grease on the sliding surfaces of the master
base jaws before inserting them into the chuck.
For high volume production applications when
jaws aren’t changed frequently, the jaws should
be removed once per shift (depending on
machining cycle time), cleaned and re-
lubricated.
•
It is recommended that the clamping force be
checked using a grip force gauge before
beginning a new production batch and between
maintenance checks. Only regular checks can
guarantee safety.
1.3.6 Use of Special Design jaws
When using special design jaws the following rules
must be observed:
Summary of Contents for ULTIMATE CHUCK UC2
Page 12: ......
Page 13: ......
Page 15: ......
Page 25: ......
Page 26: ...ATS Systems Formerly SMW Systems Ultimate Chuck UC2 Spare Parts List 3 16 2007 Page 1 of 19...