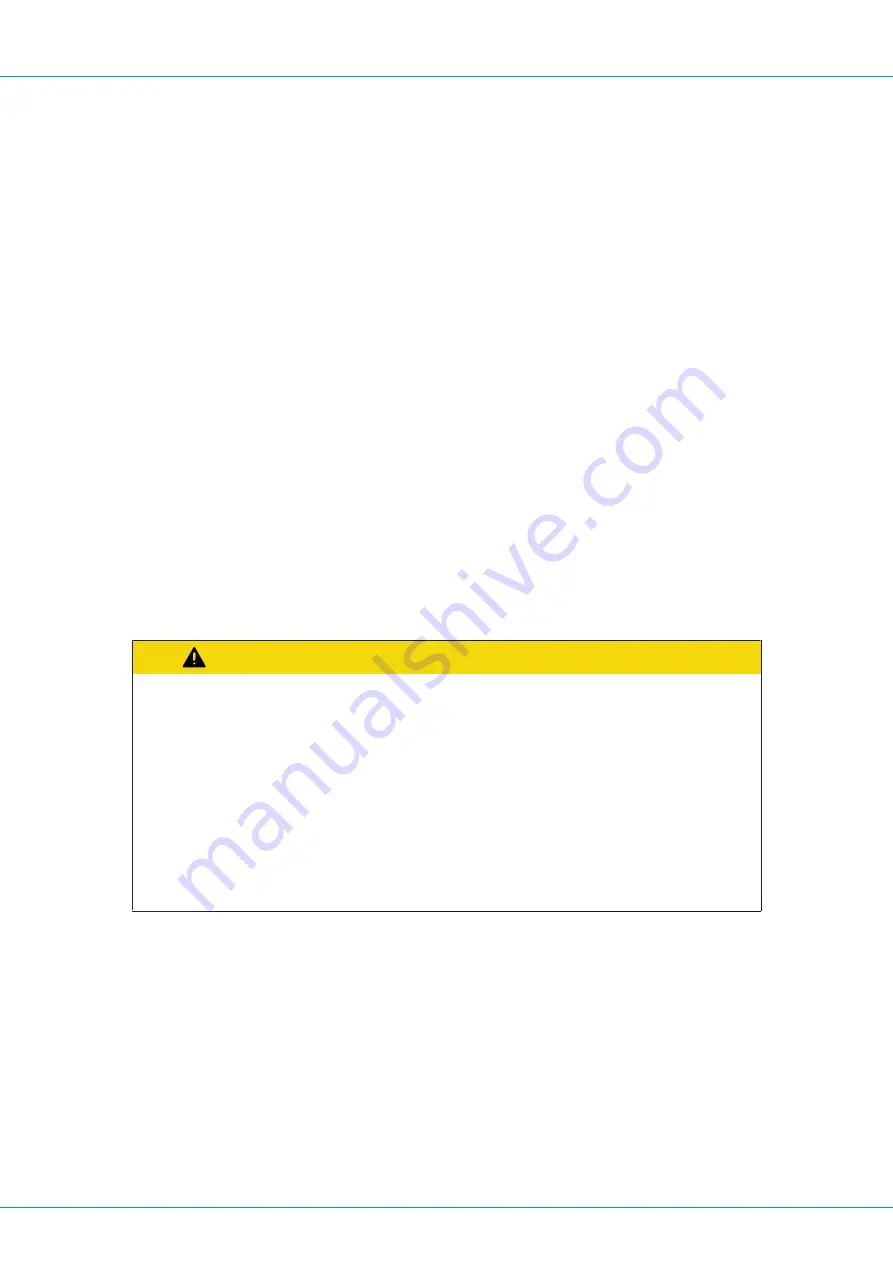
SmartROC D65 Tier 4 Final
14 Options
216
n
The RC tubes are removed and replaced with normal drill pipes. The air swivel is re-
moved and replaced with an adapter. The deflectors and sample hose can be re-
moved. An adapter is fitted on the rotation head for the air supply to the drill string.
This is a longer-term adaptation and is used if normal drilling is to be carried out over
several weeks or more.
14.4 Fire suppression system
14.4.1 Daily checks and maintenance
If there is a pressure gauge fitted, then check that the needle on the pressure meter for the
containers is within the green zone.
On
semi-automatic fire fighting systems
, check that the LEDs are working as specified
in the Operator's Manual. Perform a test - press the green test button (7) for at least 1
second. The diodes come on successively and conclude with an alarm test of signal and
lamp.
14.4.2 Annual maintenance
In many countries, insurance companies require proof that a qualified engineer has inspec-
ted and approved the fire fighting system annually. We recommend checking with your in-
surance company to find out if they have any requirements concerning this system.
14.4.3 Electric Welding, Steam Cleaning and High Pressure Cleaning
CAUTION
Risk of injury
The operator's panel on semi-automatic fire fighting systems must be disabled for the
following tasks:
u
Electric welding, battery charging and start help. Harmful currents can damage the
electronics.
u
Steam cleaning. The heat detectors are triggered at 120°C and could be activated by
the steam.
u
High-pressure washing. Components or cables could be damaged by the jets and trig-
ger the system.
Once the semi-automatic fire fighting system is enabled again, make sure the LEDs and
the system work as specified in the Operator's Manual. Perform a test - press the green
test button on the operator's panel for at least 1 second. The diodes come on successively
and conclude with an alarm test of signal and lamp. A description of the operator's panel
can be found in the Operator's Manual
14.5 Service Winch
14.5.1 Cleaning
Always clean the winch after use.
Summary of Contents for SMARTROC D65 TIER 4 FINAL
Page 2: ......
Page 4: ......
Page 10: ...SmartROC D65 Tier 4 Final Table of Contents x...
Page 32: ...SmartROC D65 Tier 4 Final 2 General 32...
Page 38: ...SmartROC D65 Tier 4 Final 3 Transport instructions 38...
Page 50: ...SmartROC D65 Tier 4 Final 5 RCS drilling system 50 Rig Layout Feeder Layout...
Page 69: ...SmartROC D65 Tier 4 Final 5 RCS drilling system 69 Rig Layout Feeder Layout...
Page 86: ...SmartROC D65 Tier 4 Final 5 RCS drilling system 86 Logging Signal Log Signal Log...
Page 109: ...SmartROC D65 Tier 4 Final 5 RCS drilling system 109 Drilling DCT DCT n Parameters n Actuations...
Page 120: ...SmartROC D65 Tier 4 Final 5 RCS drilling system 120 Rig parameters Parameters n Tramming...
Page 140: ...SmartROC D65 Tier 4 Final 6 Hydraulic systems 140...
Page 157: ...SmartROC D65 Tier 4 Final 9 Dust collector DCT 157 Dust collector...
Page 158: ...SmartROC D65 Tier 4 Final 9 Dust collector DCT 158...
Page 160: ...SmartROC D65 Tier 4 Final 10 Radiator 160 Radiator and expansion tank...
Page 170: ...SmartROC D65 Tier 4 Final 11 Diesel engine 170...
Page 182: ...SmartROC D65 Tier 4 Final 12 Compressor and air system 182...
Page 192: ...SmartROC D65 Tier 4 Final 13 Oil and fuel 192...
Page 219: ...14 Options 219...
Page 220: ...www atlascopco com 2015 12 17 No 713991051 3...