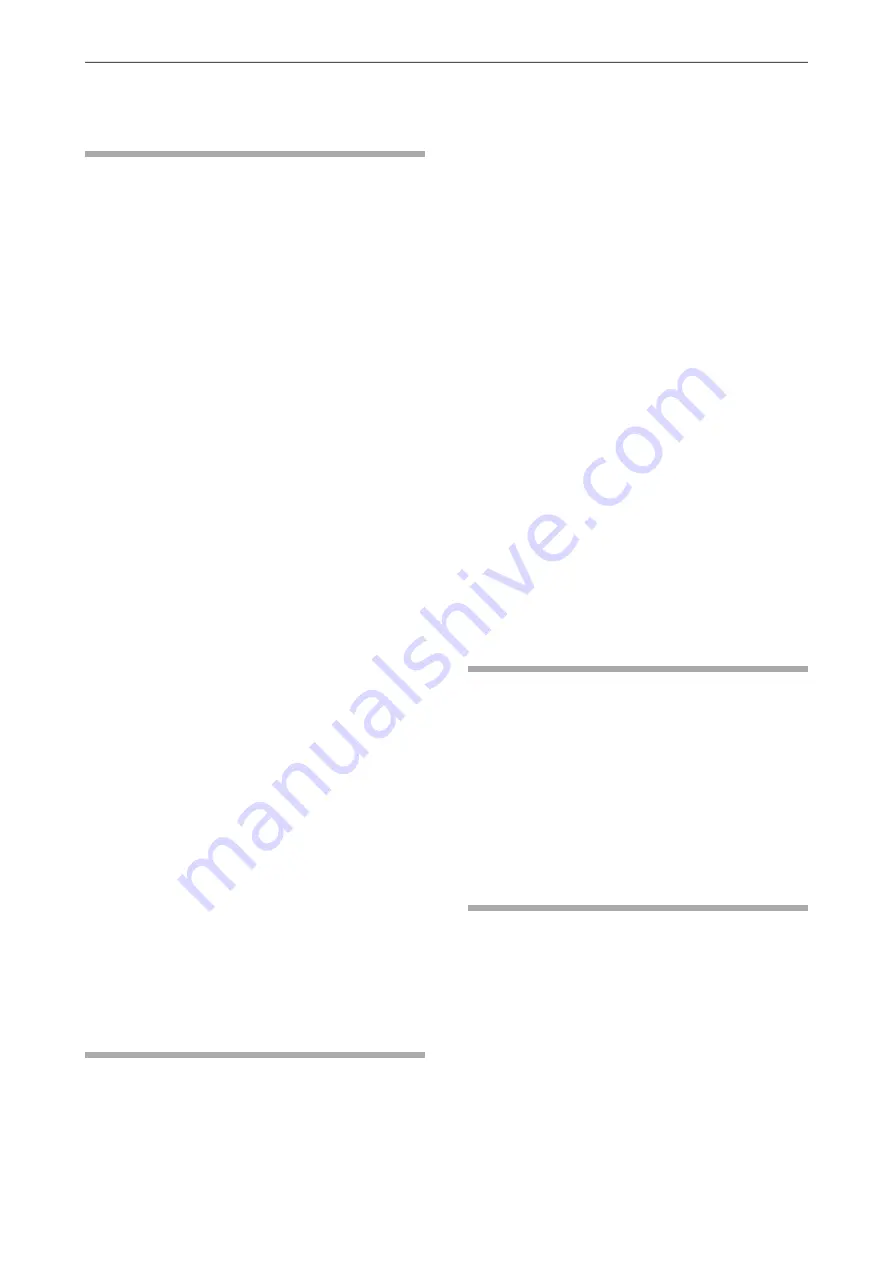
Depressurising the hydraulic
system
Even when you have switched off the carrier, a
considerable residual pressure can still be present
in the hydraulic system.
A residual pressure can still be present in the
hydraulic attachment even after you have
disconnected the quick-release couplings or closed
the shut-off valves.
The hydraulic attachment can only be depressurized
using the hydraulic system of the carrier, by allowing
hydraulic oil to drain to the tank via the return
connection.
Depending on the type of hydraulic attachment, the
internal leaks, the oil temperature, the type of
hydraulic oil and the design of the hydraulic
installation of the carrier, the time required to relieve
the pressure can vary.
Observe the following steps in order to depressurise
the hydraulic attachment:
1. Ensure that the hydraulic oil in the hydraulic
attachment and in the carrier has a temperature
of at least 0 °C. If necessary, pre-heat it to at
least 0 °C.
2. The hydraulic attachment must be connected to
the hydraulic system of the carrier device, i.e.
the hydraulic hoses must be connected up and
the respective shut-off valves in the supply pipe
and in the connection to the tank must be
opened.
3. Place the hydraulic attachment on timber support
blocks laying on the ground.
4. Depressurise the hydraulic system according to
the manufacturer's safety and operating
instructions for the carrier.
5. You must wait at least another 60 minutes until
the pressure has been relieved through leakages.
6. When you have made sure that no more pressure
is present in the hydraulic system, you must
disconnect the hydraulic connection to the carrier.
Close the shut-off valves or disconnect the
quick-release couplings, so that no hydraulic oil
can flow back from the carrier.
Cleaning
♦
Clean the hydraulic compactor if dirt adhering to
the tool impedes visual checks of the parts (hoses,
rubber isolators etc.).
NOTICE
Environmental damage due to polluted
water
Hydraulic oil and cutter grease are environmentally
harmful and must not penetrate the ground or enter
the water table or water supplies.
►
Collect the water used for cleaning if it has been
contaminated by hydraulic oil and cutter grease.
►
Dispose of the water in accordance with the
applicable regulations to avoid environmental
hazards.
Preparations
Hydraulic compactor attached:
♦
Deposit the hydraulic compactor on level ground.
♦
Secure the carrier such that it cannot move
unexpectedly.
Hydraulic compactor not attached:
♦
Plug up all hydraulic ports.
Procedure
♦
Use a pressure cleaner to remove dirt from the
hydraulic compactor.
Checking the adapter plate and
the outer and rotor housings
for cracks and/or wear
♦
Check the adapter plate and the outer and rotor
housings for cracks every week.
♦
Have rework activities or repairs carried out in time
to avoid major damage.
♦
Consult the Atlas Copco Customer Center/Dealer
in your area.
Checking the rubber isolators
for cracks
♦
Check the rubber isolators for wear every day.
♦
Have repairs carried out in time to avoid major
damage.
© 2014 Construction Tools EOOD | No. 3390 5121 01 | 2014-11-19
Original instructions
34
HC 150, 350, 450, 850, 1050, 1055
MAINTENANCE