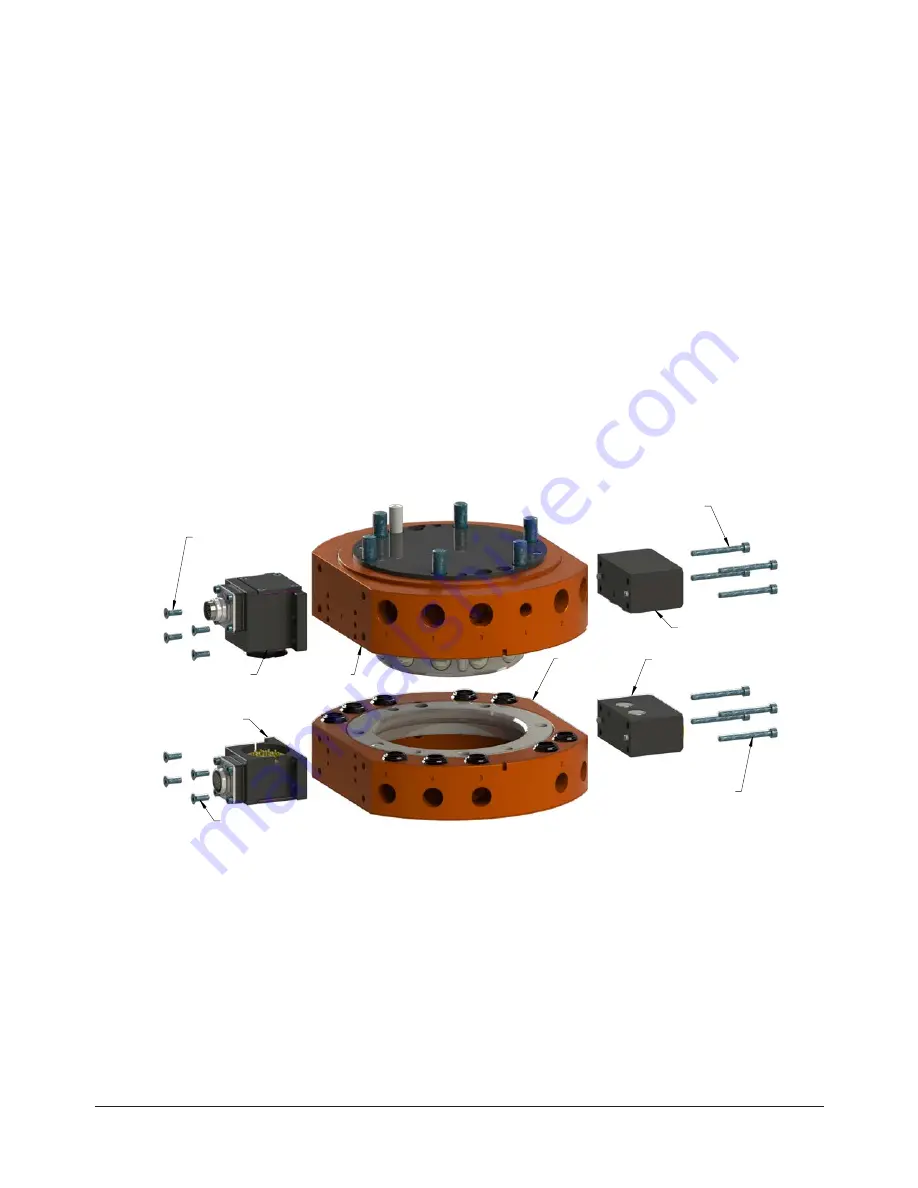
Manual, Robotic Tool Changer, QC-150
Document #9610-20-2256-02
Pinnacle Park • 1031 Goodworth Drive • Apex, NC 27539 USA • Tel: 919.772.0115 • Fax: 919.772.8259 • www.ati-ia.com • Email: [email protected]
18
3.7 Optional Module Installation
Tools required: 2.5 mm and 3 mm Allen wrench, torque wrench
Supplies required: Clean rag, Loctite 222
The optional modules are typically installed on Tool Changers prior to shipment. The following steps outline
installation or removal as required. Tool Changers are compatible with many different types of modules.
Some modules require an adapter plate to be installed to the Tool Changer.
1. Place the Tool in a secure location.
2. Uncouple the Master and Tool plates.
3.
Turn off and de-energize all energized circuits (e.g. electrical, air, water, etc.).
4. Clean the mating surfaces.
5. Align optional module on the Master or Tool plate as shown in
6.
If not using fasteners with pre-applied adhesive, apply Loctite 222 to supplied fasteners.
7. Using an Allen wrench, secure the module with (4) M4 mounting fasteners. Refer to
for torque
for your specific mounting fasteners.
8.
Remove all protective caps, plugs, tape, etc from the module prior to operation.
9.
After the procedure is complete, resume normal operation.
Figure 3.4—Optional Module Installation
Tool Plate
Assembly
Master Plate
Assembly
(4) M4 Socket Head
Cap Screw
Fluid/Air Module
(9120-FN2-T Shown)
(4) M4 Socket Head
Cap Screw
Fluid/Air Module
(9120-FN2-M Shown)
(4) M4 Socket Flat
Head Cap Screw
(4) M4 Socket Flat
Head Cap Screw
Electrical Module
(9120-RF19-M Shown)
Electrical Module
(9120-RF19-T Shown)
3.8 Optional Module Removal
Tools required: 2.5 mm and 3 mm Allen wrench
1. Place the Tool in a secure location.
2. Uncouple the Master and Tool plates.
3.
Turn off and de-energize all energized circuits (e.g. electrical, air, water, etc.).
4. Disconnect any cables, air line, etc. if required.
5. Supporting the module and using an Allen wrench, remove the M4 mounting fasteners.
6.
Remove the module from the Master or Tool plate.