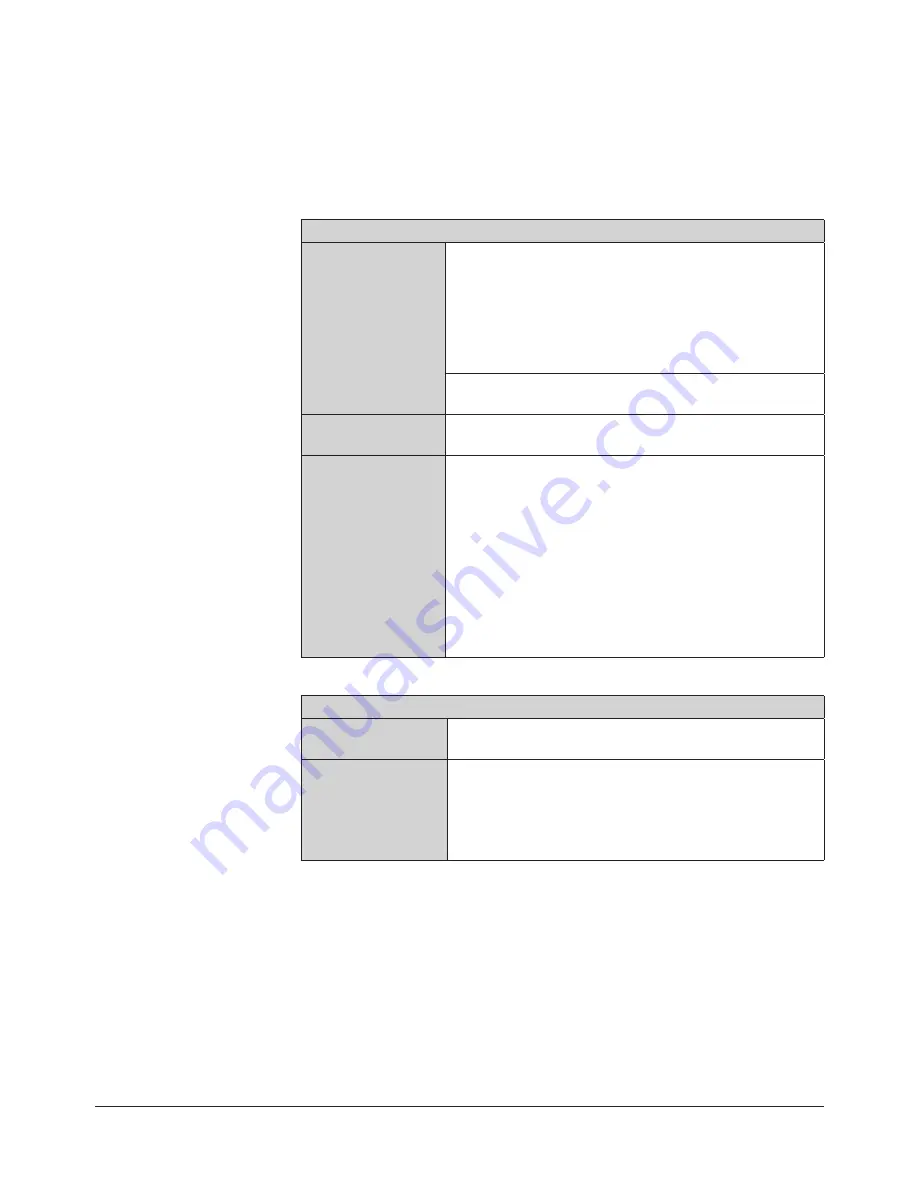
Manual, Flexdeburr, RC‑660 Series
Document #9610‑50‑1017‑10
Pinnacle Park • 1031 Goodworth Drive • Apex, NC 27539 USA • Tel: +1.919.772.0115 • Fax: +1.919.772.8259 • www.ati‑ia.com
10
2.3 Technical description
The technical overview of the product is provided in the following tables and graphs. For additional
technical specifications, refer to
.
2.3.1 Environmental Limitations
2.3.1.1 Operation
Table 2.1—Operation
Installation
position
Mounted to robot using the side mounting pattern
or rear adapter flange. Refer to
. The flange is specific to each type of robot.
This optional flange is normally supplied by ATI in a
blank form suitable for customer modification. Refer to
Mounted to a table or stand by means of the bench
adapter (the robot is carrying the work piece).
Temperature
range
5
°
C–35
°
C
(41
°
F–95
°
F)
Utilities
The tool requires the following:
•
Clean, dry, filtered, non‑lubricated air.
•
A coalescing filter and filter elements rated
5 micron or better.
•
The motor spindle must be supplied air at
6.2 bar (90 psi).
•
The radial compliance (centering) air must be
supplied from a regulated source between
1.0–4.1 bar (15–60 psi).
2.3.1.2 Storage
Table 2.2—Storage
Temperature
range
0
°
C–45
°
C
(32
°
F–113
°
F)
Conditions
The tool should be stored in its crate and in a dry
place.
When not in use, keep the unit in its crate if possible.
Consult
Section 3.4—Storage and Preventive
of this manual.
2.3.2 Compliance Unit Performance
The graphs in
illustrate the variation of compliance force with applied air pressure in the
vertical orientation with the collet pointed toward the ground. Measurements may vary from one
product to another and should only be treated as nominal.
The actual force characteristics are dependent on mounting orientation and condition of the unit. In
applications, where the deburring tool is mounted horizontally, additional compliance air pressure
is required to overcome the weight of the motor. Compliance pressure is also dependent upon the
material of the work piece, type of bur tool, and the amount of material that is removed.
The turbine motor attempts to maintain its full rated speed even under loaded conditions. However,
when extremely heavy cuts are taken, the motor may eventually stall. Therefore, multiple, light
passes are preferred over slow, heavy cuts.