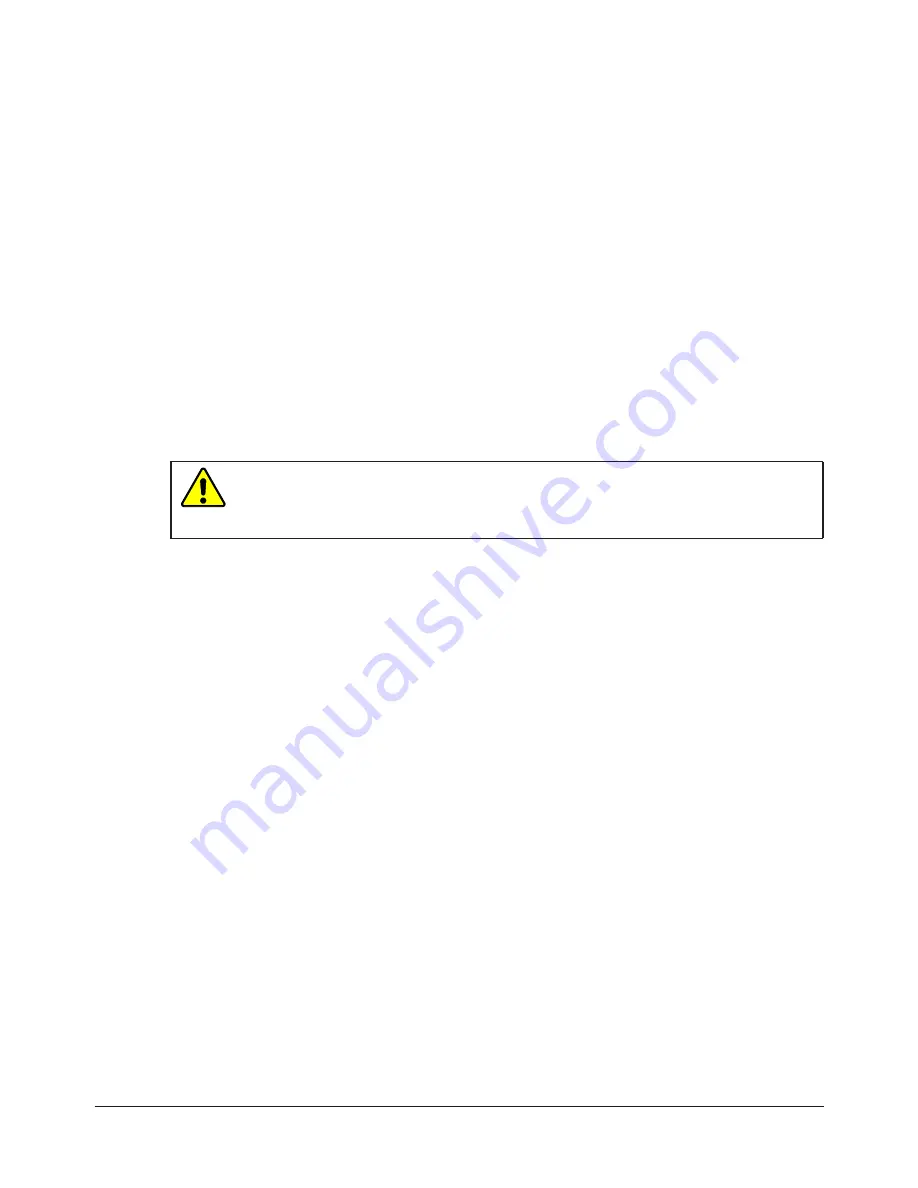
Manual, Flexdeburr, RC‑660 Series
Document #9610‑50‑1017‑10
Pinnacle Park • 1031 Goodworth Drive • Apex, NC 27539 USA • Tel: +1.919.772.0115 • Fax: +1.919.772.8259 • www.ati‑ia.com
24
5. Maintenance
The RC deburring tool provides long life with regular maintenance. The preventive maintenance of the deburring
tool consists of cleaning the unit and regular inspection for wear or damage to the pneumatic lines, filter element,
spindle boot, and bur. Refer to
Section 6—Troubleshooting and Service Procedures
to assist with service.
For all service, the air supply (before the solenoid valves) must be disconnected. Drain any trapped air pressure in
the lines. It is suggested that the air supply be “locked out” to prevent accidental operation of the spindle. Refer to
Section 6.2—Service Procedures
for maintenance instructions. Service and repair parts are identified in
.
5.1 Pneumatics
The air lines to the deburring tools must routinely inspected for their general condition and replaced as
required. The air to the Flexdeburr must be filtered, dry, and non‑lubricated. Inspect air filters and replaced
as required to maintain optimum performance. The life of the filter elements is dependent on the quality of
compressed air at the customer’s facility and therefore cannot be estimated.
5.2 Lubrication
Lubrication systems are not to be used
. The Flexdeburr air motor must be supplied with clean, dry, filtered
air. Oil in the air stream will cause the air motor to fail prematurely. Failure of the motor due to oil in the air
stream is not covered under the warranty. See
for details on air supply and quality.
CAUTION:
Do not use lubricated air with the Flexdeburr. Oil in the air stream will
result in the premature failure of the air motor and is not covered under warranty. It
is recommended that the customer use a coalescing filter and filter elements rated 5
micron or better.
5.3 Spindle Boot Inspection
The spindle boot prevents debris from entering the housing and protects internal components. Inspect
the spindle boot regularly for damage and replace if necessary. Refer to
5.4 Bur Inspection
The bur wear depends on cut depth, feed rate, and material being deburred. Inspect the bur regularly for
wear and refer to
symptoms of worn bur.
5.5 Spindle Motion Inspection
The pivot bearing allows articulation of the motor assembly. The pivot bearing is subject to wear and must
be replaced when excessive spindle motion is observed. Contact between the motor air supply fitting and
the main housing indicates pivot bearing wear and must be corrected. Refer to