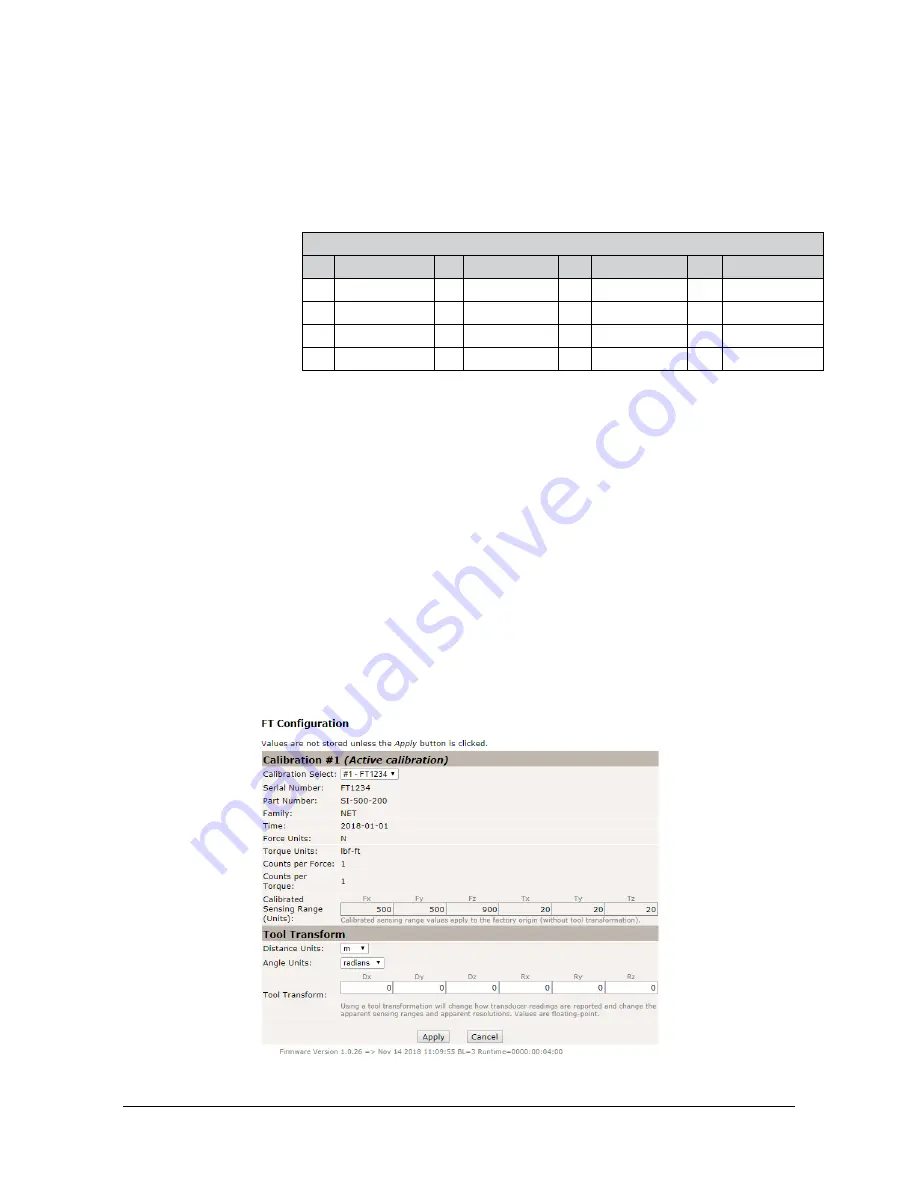
Manual, F/T Sensor, Ethernet Axia
Document #9610-05-Ethernet Axia-09
Pinnacle Park • 1031 Goodworth Drive • Apex, NC 27539 • Tel:+1 919.772.0115 • Fax:+1 919.772.8259 •
51
Output Code:
When this statement’s comparison is found true, this 8-bit value will be bitwise
OR’ed with the Output Code values of all other true statements to form the
threshold output. Any set bits remain latched until the user issues a
Resent Latch
.
If no statements are true the threshold output is zero.
The value displays in hexadecimal, format 0x00. A user may type output codes
in hexadecimal format or in decimal. Bit pattern representing each thresholding
statement number are in the following table.
Table 6.3—Bit Patterns for Thresholds Breached
#:
Bit Pattern
#:
Bit Pattern
#:
Bit Pattern
#:
Bit Pattern
0:
0x00000001
4:
0x00000010
8:
0x00000100
12:
0x00001000
1:
0x00000002
5:
0x00000020
9:
0x00000200
13:
0x00002000
2:
0x00000004
6:
0x00000040 10: 0x00000400
14:
0x00004000
3:
0x00000008
7:
0x00000080 11: 0x00000800
15:
0x00008000
Get Statuses:
Click the
Get Statuses
button to update the static display of the threshold status. If
a threshold is unsatisfied, the threshold numbers are crossed out.
6.6 F/T
Configurations Page (config.htm)
On the
Configurations
page, a user may select the active calibration (
Section 15.3—Calibration Ranges
)
and tool transformation settings for the sensor system. When the user clicks the
Apply
button, the changes
on this page are implemented on the sensor. For more information about tool transformation feature, refer to
Section 4.7—Tool Transformation
.
From the
Configurations
page, a user may obtain the following values: the sensor’s
Serial Number
,
Part
Number
, calibration
Family
,
Time
or date the sensor was calibrated, force units, torque units, counts per
force, and counts per torque. Note that these are the same values that are in
“SET” Command Fields and Values
and
Section 11.2—Calibration Information (netftcalapi.xml)
For more information about how F/T values are scaled with the counts per force and counts per torque, refer
to
Section 4.4—Converting Counts Per Force/Torque to F/T Values
The
Calibrated Sensing Range
field displays the maximum rating for each axis of the selected calibration.
Figure 6.7
—Configurations Page