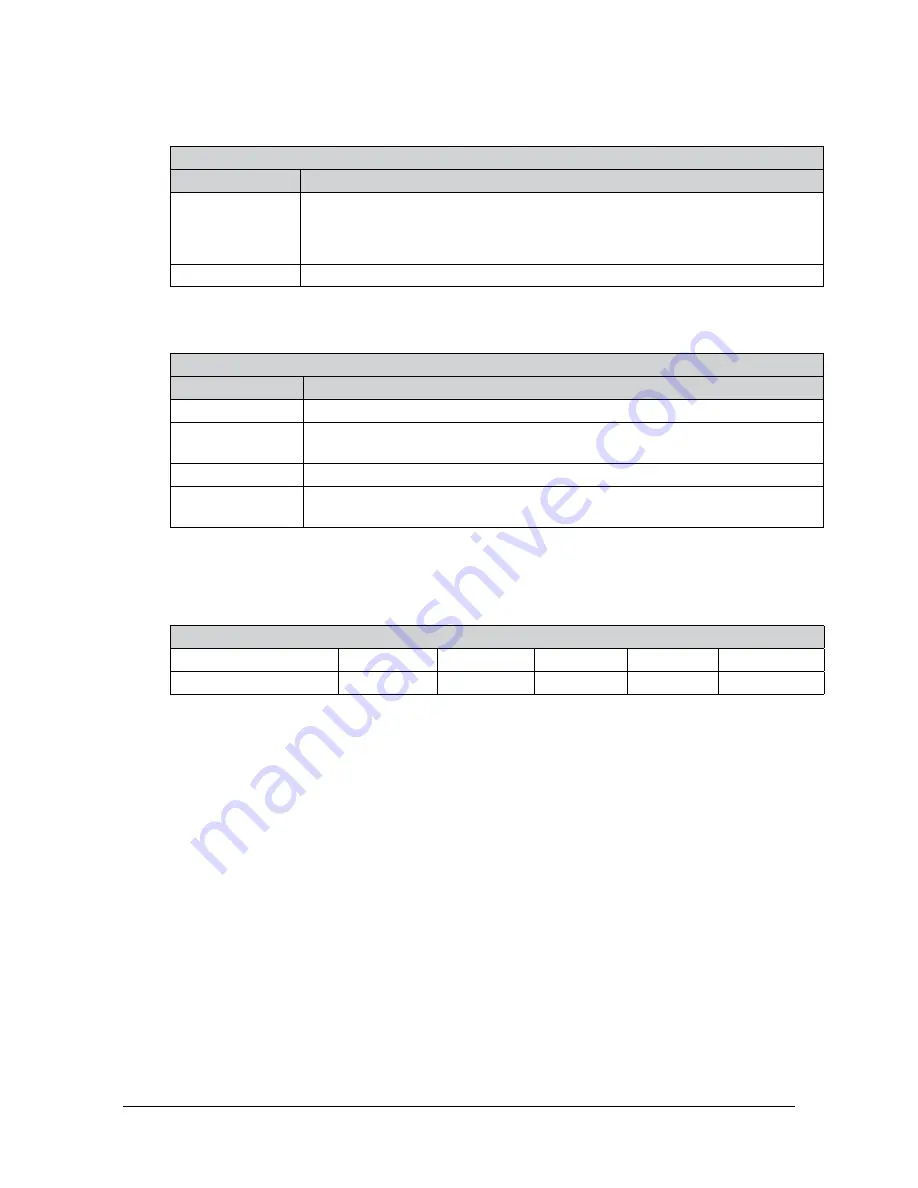
Manual, F/T Sensor, Ethernet Axia
Document #9610-05-Ethernet Axia-09
Pinnacle Park • 1031 Goodworth Drive • Apex, NC 27539 • Tel:+1 919.772.0115 • Fax:+1 919.772.8259 •
27
4.2.3 DIAG LED
One LED signals the communication status of the Ethernet Axia sensor interface as follows:
Table 4.3—DIAG LED
LED State
Description
Red
Indicates an error in the STATUS word except the following:
1. The gage temperature is out of range.
2. A gage is disconnected.
Off
Ethernet interface is in an operational state. No errors are found.
4.2.4 Sensor Status LED
One LED signals the health status of the sensor as follows:
Table 4.4—Sensor Status LED
LED State
Description
Off
The sensor is powering up and checking STATUS.
Red
Indicates an error in the STATUS word, or a
bad system status
reported on
the
System Information
webpage.
Green
Normal operation. Indicates no error in the STATUS word.
Red/Green
(Orange)
Indicates that a F/T axis is out of range.
4.3 Sample Rate
The power-on default sample rate is the rate the user set before removing power. The sample rate is stored
to nonvolatile memory. The
adcRate
Section 8.4—Console “CAL” | “SET” Command Fields and
controls the current sample rate. The following table lists the rounded and exact sample rates.
Table 4.5—Sample Rate
Rounded Sample Rate
0.5 kHz
1 kHz
2 kHz
4 kHz
8 kHz
Exact Sample Rate
488 Hz
976 Hz
1953 Hz
3906 Hz
7912 Hz
4.3.1 Sample Rate Versus Data Rate
The data rate is how fast data can be output over the Ethernet network.
If the data rate is faster than the sample rate, the customer sees duplicate samples output over the
network until the next sample is read internally. A faster data rate could be useful so that the sensor
sends data at the same rate that other devices in a customer’s system are outputting. For example: if
a discrete I/O device on the same network as the Axia is outputting data at 7,000 Hz, the customer
may want the Axia to be outputting data to the network at 7,000 Hz as well, even though the sensor
is not sampling that quickly internally.
If the sample rate is faster than the data rate, the customer does not receive the data from every
internal sample over the network. However, any filters that are enabled work based on the faster
internal sample rate, and so the sensor filters out higher frequency noise sources than if the filter is
operating at a slower data rate.
4.4 Converting Counts Per Force/Torque to F/T Values
To obtain the real force and torque values, each force value must be divided by the counts per force (cpf)
factor, and each torque value must divided by the counts per torque (cpt) factor. The cpf and cpt factors
can be obtained using the “set” command or from the
Configurations
Configurations Page (config.htm)
).
For example: if a calibration reports 1,000,000 counts per N and the F
z
reports 4,500,000 counts, then the
force applied in the Z axis is 4.5 N.