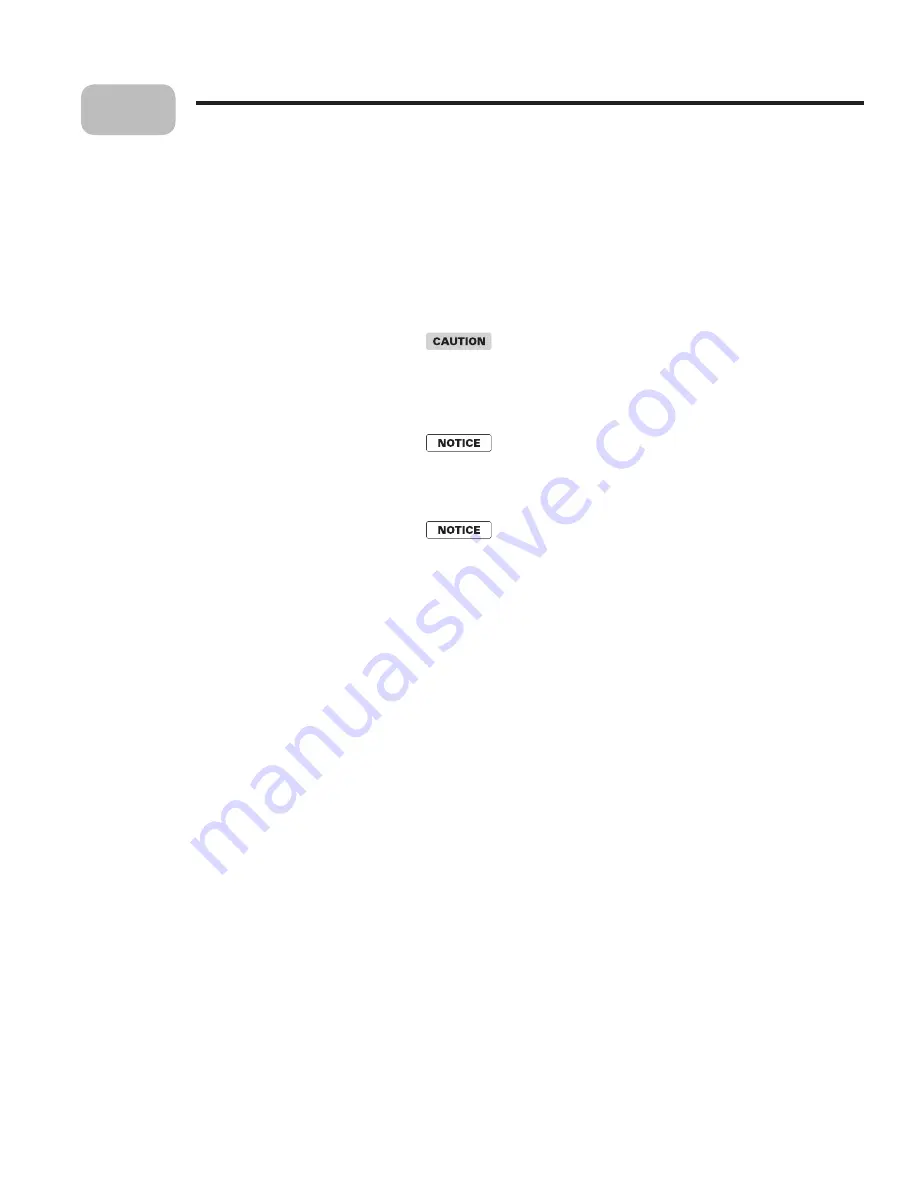
Page 53
KN INSTALLATION AND OPERATION INSTRUCTIONS
IAR (Indoor Air Reset) wiring, when used
Wiring for typical zone controller
• Heat Demand terminal connections — The end switch leads from the controller
must connect to the Heat Demand terminals on the electrical connection board as
shown in Figure A3.
• IAR connections — See Figure A3 for typical wiring to the IAR inputs when using
a zone controller. For other applications, see the Control manual and Section 7 of
this manual.
Polarity
— The connections to the
IAR
positive terminals (
IAR +
)
must be to the same location on the zone valve as the thermostat wire,
as shown in Figure A3. The connections to the
IAR
negative terminals
(
IAR –
) must be from the zone controller’s 24VAC common terminal
as shown. Connecting the wires incorrectly can cause the transformer
to be shorted out and damaged.
Thermostat terminal connections:
Use a voltmeter to verify the
wiring is correct. Measure the voltage on the thermostat terminals
with the zone controller powered, BEFORE connecting any wires. The
IAR positive terminal connections (
IAR +
) must be to the side of the
thermostat connections that have zero voltage.
DHW priority zone:
Most zone controllers will provide a priority
zone for connection to a DHW tank aquastat and circulator. The priority
switch will turn off space heating when there is a DHW call. Read the
controller manufacturer’s instructions to determine which zone is set
up for priority operation.
Appendix A — suggested wiring
(continued)
16