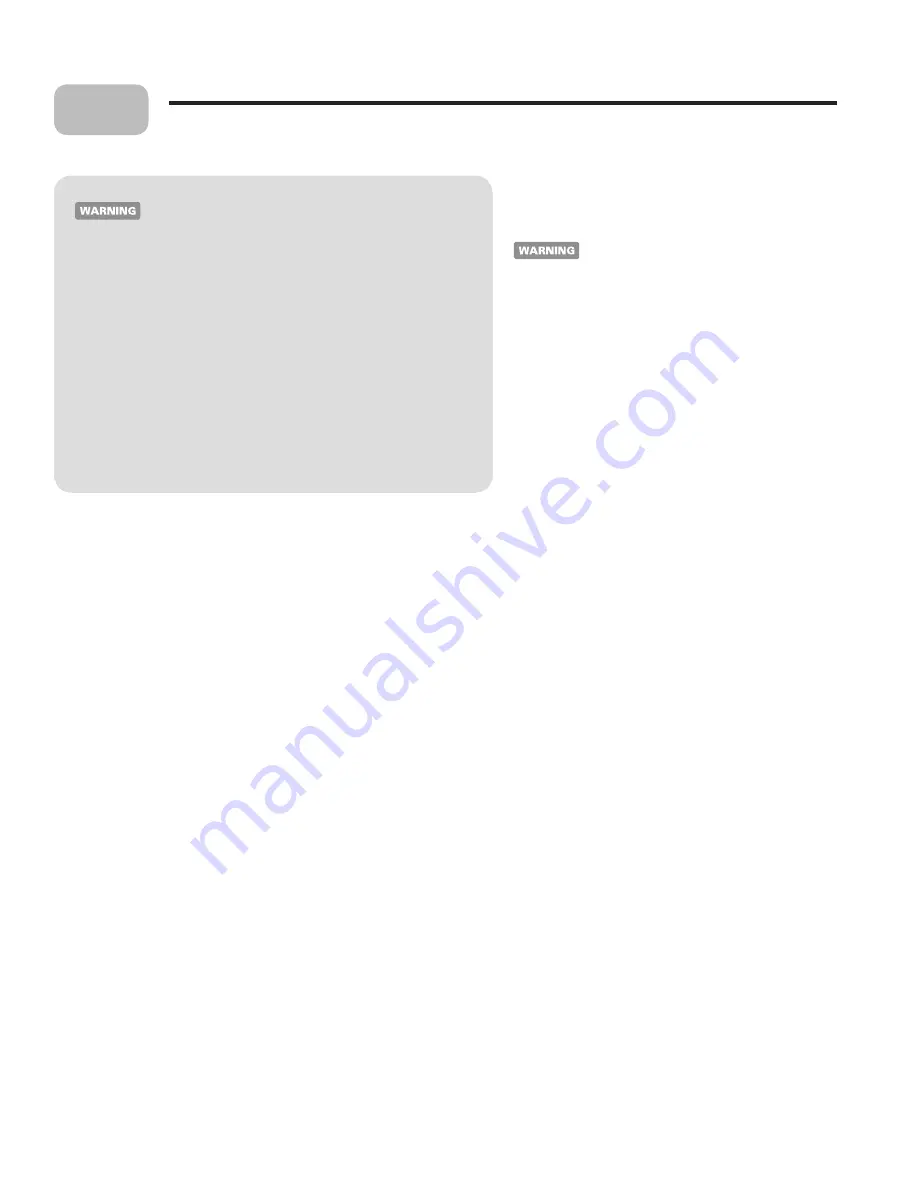
Page 30
KN INSTALLATION AND OPERATION INSTRUCTIONS
Fill and test the system
Failure to adhere to the following could result in
boiler section failure, resulting in potential for
severe personal injury, death or substantial property
damage.
❑
Flush and clean the system before filling.
❑
Provide clean water to fill the system
❑
Water quality must be as prescribed in this manual.
Follow the system water checklist
Follow the guidelines in this section to fill and test the system. The system
water quality must meet the conditions given, and you and the owner must
make sure the conditions will be maintained throughout the life of the boiler.
❑
Closed systems only
• Do not apply the
K N
boiler on open systems, such as direct heating of domestic
water, swimming pool heating or process applications that use system water. For
these applications, you must install a heat exchanger.
❑
Hard water conditions
• If water hardness exceeds 7 grains, use a water softener in the fill line to soften the
water before it enters the system.
• On multiple boiler commercial installations, the large volume of water in the
system can contain substantial mineral salts, even if the fill water hardness is less
than 7 grains. These salts can deposit in the boiler heat exchanger as limestone,
causing possible section damage. Commercial installations should usually be filled
with soft water to avoid this problem.
❑
Prevent oxygen corrosion
• Make sure the system is provided with adequate automatic air elimination, including
an in-line air separator and automatic air vents (diaphragm or bladder tank systems) or
piping to the expansion tank (closed-type expansion tank systems).
• Do not connect the
K N
boiler to a system that contains non-barrier radiant
tubing. Non-barrier tubing can allow oxygen to enter the system, causing oxygen
corrosion of the boiler heat exchanger.
❑
Flush and clean the system
• Flush the system to remove sediment, flux, filings and other foreign matter. Use
cleaning chemicals sold for use in hydronic systems.
• Replacement boiler installations often have large amounts of accumulated
sediment and corrosion that must be removed to ensure boiler life and reliable
operation.
• Flush each zone of multi-zone systems individually using the purge valves and
isolation valves in the system.
• Flush until the water runs clean.
• After flushing the system thoroughly, use trisodium phosphate
or other chemical sold for cleaning hydronic systems to remove
sediment and sludge.
Use caution when working with chemicals,
following all guidelines specified by the chemical
supplier and the applicable codes.
❑
Purge air from the system
• The system should be installed with purge valves such as
those shown in the suggested piping in this manual. Purging
is the most efficient way to fill the system and remove most
of the air.
• Connect a hose to a purge valve and run the hose to an
appropriate draining area. (When filling with antifreeze
solution, run the hose back to the solution tank.)
• Close all isolation valves in the system.
• Open the manual valve (or quick-fill valve) on the make-up
water line. (When filling the system with glycol, connect
from the glycol pump to one of the purge valves with a
hose.)
• Purge each zone separately by opening the isolation valves
for that zone, allowing water to push the air through and fill
the zone. After filling the zone, close the isolation valves and
move to the next zone.
• Fill and purge the boiler loop in the same manner.
• After the boiler is operated for a while, air entrained in the
fill water will bubble out of the water as it heats, and will
have to be removed by using air vents in the system.
❑
Add a chemical inhibitor
• After purging and filling the system, add a chemical inhibitor
sold for use in hydronic systems to prevent limestone and
magnetite deposits from forming, and to protect the boiler
from galvanic corrosion.
❑
Water pH
• The boiler water must be slightly basic, never acidic. Use
litmus paper to check pH, which should range from 6.5
minimum to 11 maximum.
• If pH does not comply, provide water chemistry correction
from a qualified water treatment specialist. If required, make
sure that the owner is aware and that the regimen will be
continued.
11