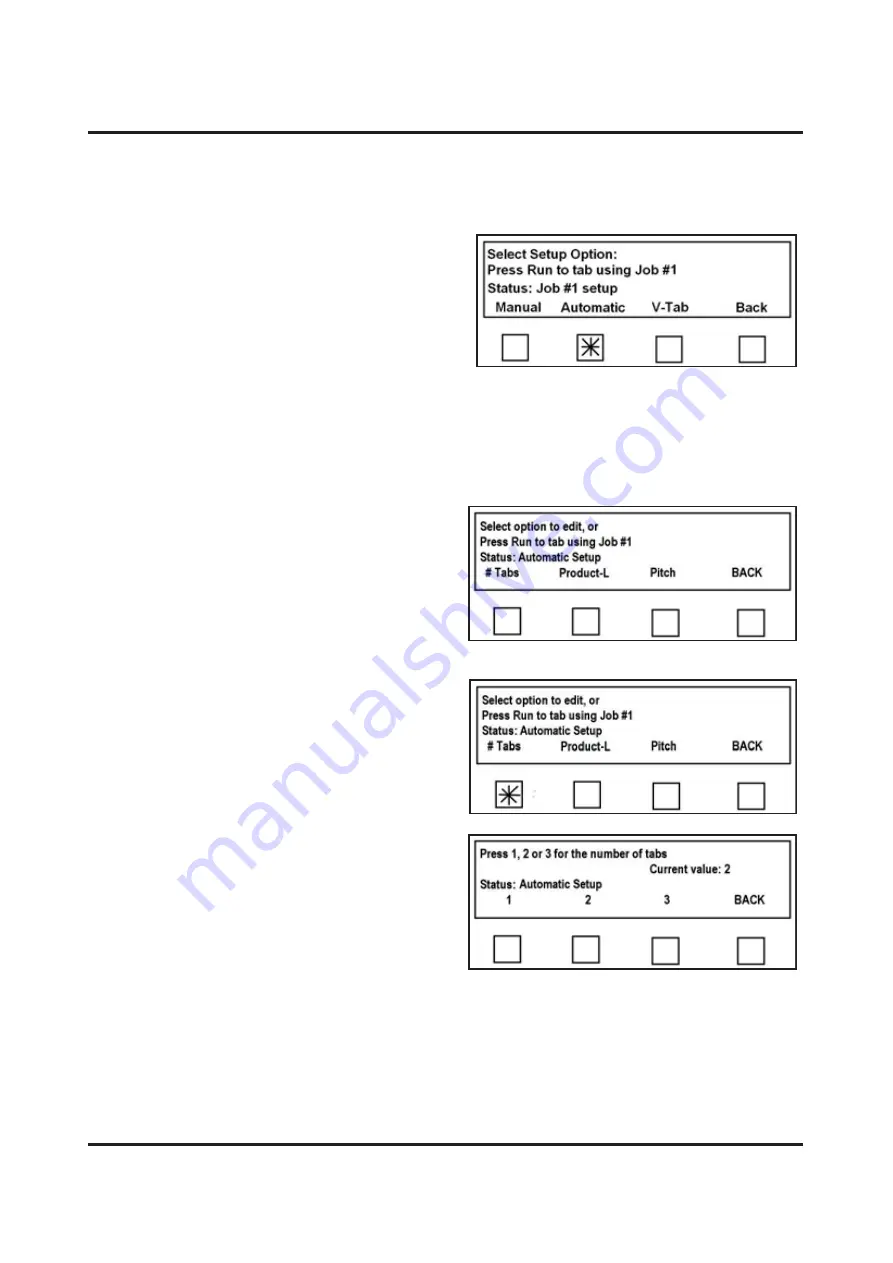
PROGRAMMING TABBER
28
Automatic Tab Positioning
Automatic Tab Positioning Features
Pressing
Automatic
soft key from
“
Select Setup
Option
”
screen puts Tabber into
“
automatic
positioning mode
”
.
Tabber will automatically set
Offset Values
(
positions
) based on product length and number of
tabs selected.
1 Tab
–
Tab is applied centered along length
of media.
2 Tabs
–
Tabs are applied within 0.5" from each edge.
3 Tabs
–
Two tabs are applied within 0.5" from each edge and one tab is centered.
When
“
Automatic
”
is selected, the following choices appear:
# Tabs
–
Allows you to choose Number of
Tabs to apply to media.
Product-L
–
Set Paper Length of media you
are using.
Pitch
–
Set
Tab Pitch
(
distance from top of
one tab, to top of next tab
) for Tab stock used.
BACK
–
Returns to previous screen.
When
#Tabs
soft key is pressed, display
prompts you to select number of Tabs to be
applied to mail piece.
1
–
Selects one tab
2
–
Selects two tabs
3
–
Selects three tabs
BACK
–
Returns to previous screen.