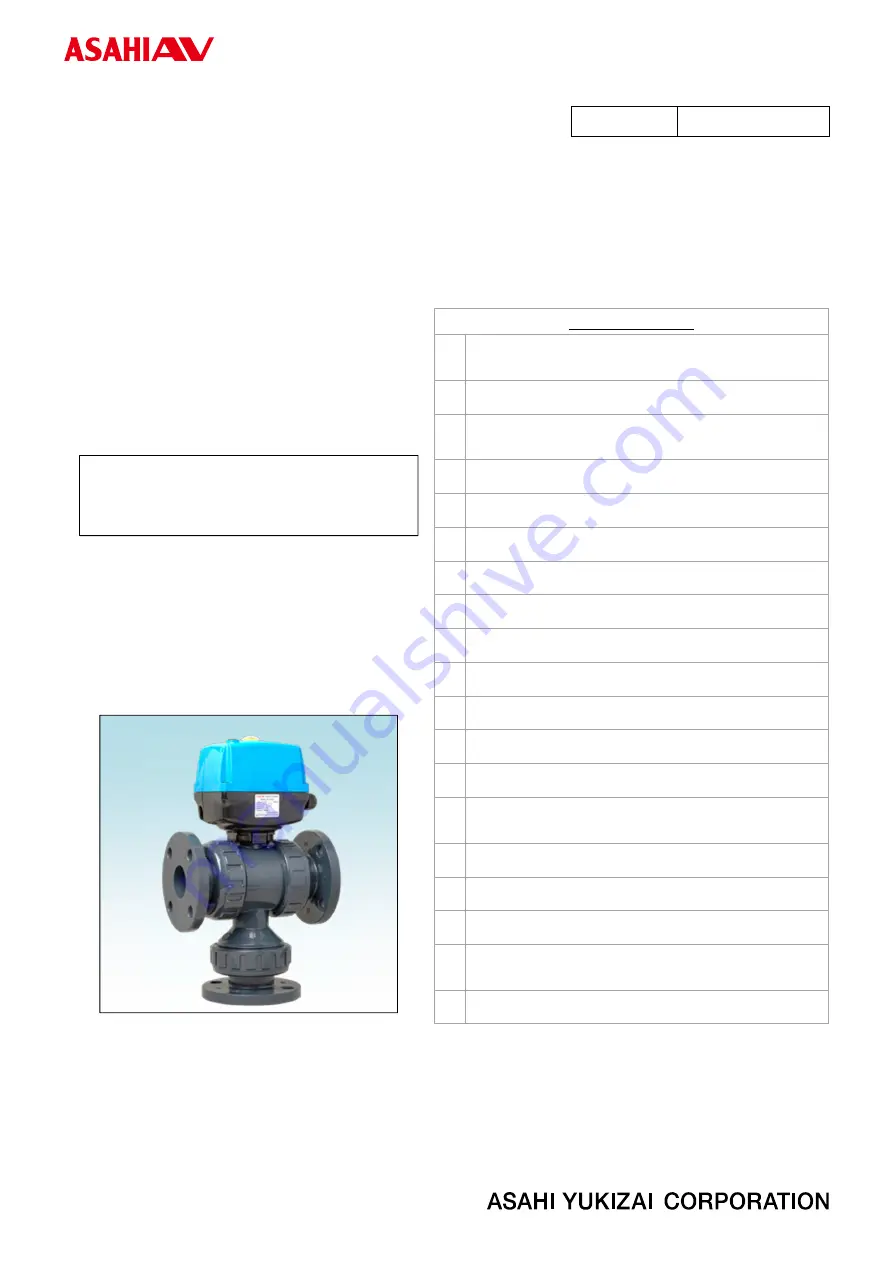
Installation, Operation and Maintenance Manual
【
H-A077-E-00
】
3-Way Ball valve Type 23 Electric actuated Type Z 15
~
50mm (½”-2”)
Serial No.
H-A077-E-00
Table of contents
1.
Be sure to read the following warranty clauses
of our product
·······································
1
2.
General operating instructions
··················
2
3.
General instructions for transportation,
unpacking and storage
···························
4
4.
Name of parts
·······································
5
5.
Maximum working pressure vs. temperature
7
6.
Specifications of valves
···························
7
7.
Specifications of actuator
························
8
8.
Installation procedure
···························
10
9.
Support setting procedure
·····················
17
10.
Electric wiring procedure
·······················
18
11.
Operating procedure
····························
20
12.
Adjustment of limit switches procedure
·····
23
13.
Actuator removal procedure
···················
24
14.
Method of adjusting face pressure between ball
and seat
············································
25
15.
Disassembling method for replacing parts
·
26
16.
Inspection items
··································
28
17.
Troubleshooting
··································
28
18.
How to inquire about defects or replacement
·························································
30
19.
Handling of residual and waste materials
··
30
3-Way Ball valve Type 23
Electric actuated Type Z
(15〜50mm [
½
”-2”])
Userʼs Manual