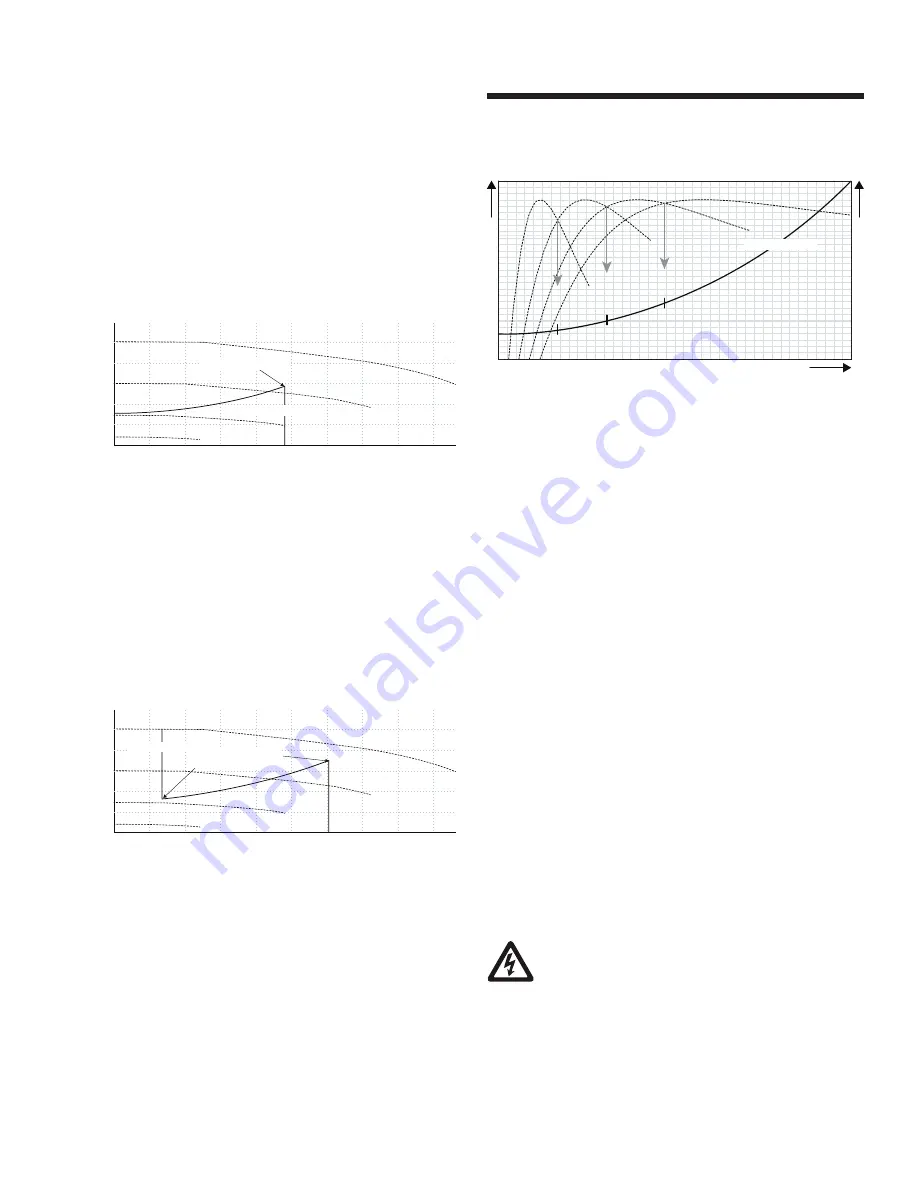
installation &
operating instructions
Design Envelope
4300
&
4380
Vertical In-line Pumping Unit
27
a maximum flow setting. This will prevent over-pumping and
save energy costs. Over-pumping is common in
hvac
systems
as pumps are typically oversized for the application. Pump
controls can only control the flow to a minimum speed; thus a
dry-contact relay is supplies which will close when maximum
flow is reached, which can be used for an alarm or other device.
0
0
20
40
60
80
100
200
400
600
800
1000
1200
120
140
160
180
head
flow
target curve
Maximum Flow Setting
5.7 quadratic curve control with minimum
& maximum flow protection
This control mode combines the control logic of
5.5 & 5.6
which takes the values of the quadratic control curve and
protection for both the maximum & minimum flow limits. Pump
controls can only control the flow to the motor limit or maxi-
mum / minimum speed limits of the unit, thus a dry-contact
relay is supplies which will close when either the minimum or
maximum flow is reached, which can be used for an alarm or
other device.
0
0
20
40
60
80
100
200
400
600
800
1000
1200
120
140
160
180
head
flow
target curve
Minimum & Maximum
Flow Settings
5.8 parallel sensorless pump control (pspc)
This configuration maps the system quadratic control curve
into the
pspc
controller where the controller intelligence
ensures the system flow requirements are met, while stag-
ing the pumps on and off to maintain optimum pump energy
usage. This is accomplished by operating the pumping units
at the best pumping efficiency level for the required flow. This
controller is available for all Design Envelope equipment to a
total quantity of
6
units.
head
efficiency
flow
1-pump
1p eff
2p eff
3p eff
4p eff
2-pump
s
3-pum
ps
4-p
um
ps
pspc control curve
5.9 2*100% capacity split units
When duty / standby is specified, enter the total system flow
into ACE Online or ADEPT, then select
2*100%
unit split for
a superior customer value. The
100%
flow redundancy is still
in place
plus
the onboard
pspc
will engage the second unit in
parallel operation should it predict lower operating costs.
If second side power is locked out, the operating pump will
operate alone on the control curve to
100%
design flow.
6.0 maintenance
6.1 general care
Vertical In-Line pumps are built to operate without periodic
maintenance, other than motor lubrication on larger units. A
systematic inspection made at regular intervals, will ensure
years of trouble-free operation, giving special attention to the
following:
•
Keep unit clean
•
Provide the motor with correctly sized overload protection.
Keep moisture, refuse, dust or other loose particles away
from the pump and ventilating openings of the motor.
•
Avoid operating the unit in overheated surroundings (Above
100°f/40°c)
.
warning
Whenever any service work is to be performed on
a pumping unit, disconnect the power source to
the driver, lock it off and tag with the reason. Any
possibility of the unit starting while being serviced must be
eliminated. If mechanical seal environmental accessories are
installed, ensure water is flowing through the sight flow
indicator and that filter cartridges are replaced as recommend-
ed. (See Armstrong files
43.85
and
43.86
for seal environ-
mental instructions).
Summary of Contents for Design Envelope 4300
Page 2: ......