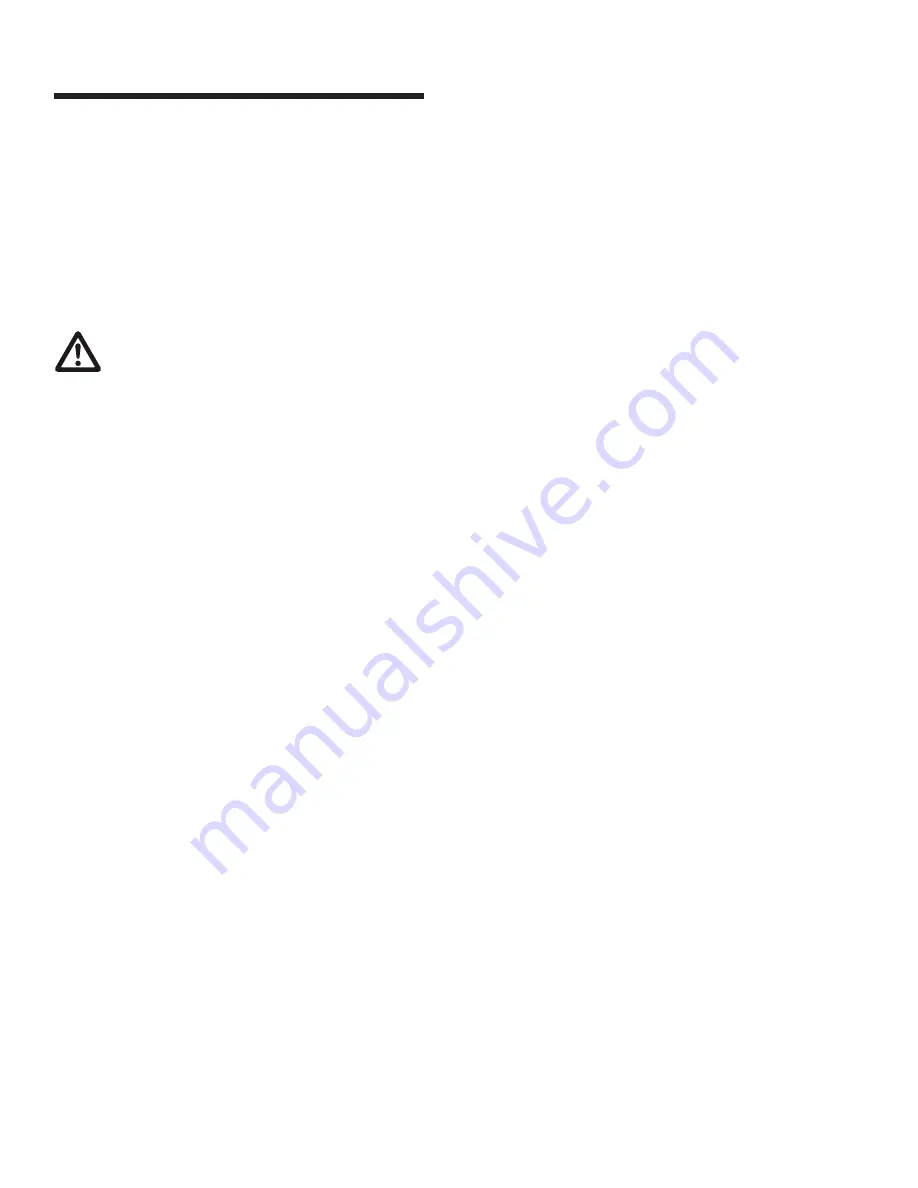
installation &
operating instructions
Design Envelope
4300
&
4380
Vertical In-line Pumping Unit
30
with larger motors it is advisable to install a permanent device
for lifting the rotating assembly out of the pipe mounted casing
to service the unit.
Breakdown procedures:
caution
Exercise extreme care when handling power wiring.
Ensure that the fuses are removed or breaker discon-
nected in the power line to the motor. Power discon-
nect should be within sight of the pump being serviced and
tagged with the reason for disconnection.
a
Electrical wiring
If the pump and/or motor assembly is to be serviced on a
bench, the motor wiring must be disconnected.
b
Isolation valves
If the system is not drained: Ensure that the suction and dis-
charge piping isolation valves are closed. Remove drain plug
(35)
from the bottom of the casing and drain the pump.
c
Prepare assembly for removal
Secure the motor
(10)
by lifting straps to an overhead chain
fall or similar lifting device. The device must be designed to lift
the weight of the unit safely. Raise the lifter to bring the lifting
straps taut. Disconnect the flush/vent flex hose from pump
suction and secure flex hose to one side. Remove the clamp
ring between casing
(100)
and adapter
(40)
. Care should
be taken not to apply pressure to the outside diameter of the
adapter, to prevent possible breakage, outside pressure should
be on the casing only.
d
Remove rotating assembly
The rotating assembly [motor, adapter and impeller]
(10, 40 &
80)
may now be lifted out of the casing.
e
Rotating assembly notes
The impeller
(80)
is fastened directly to the stub shaft and
must be removed to replace the mechanical seal assembly
(61/62)
. This may be accomplished on a safe surface near the
installation, or more conveniently on a work bench.
f
Impeller cap screw
The impeller
(80)
should be prevented from rotating while the
impeller cap screw
(86)
is loosened. A heavy screwdriver or
pry bar may be inserted in between the impeller blades to en-
able the impeller cap screw
(86)
to be backed off with a socket
wrench [
note:
be careful not to damage the impeller blades].
Remove the impeller cap screw and washer
(86 & 83)
.
g
Pump impeller
Using wheel pullers, with the jaws behind the rear shroud of
the impeller
(80)
[Behind a vane at each side] pull the impeller
free of the pump shaft. Impeller that is difficult to remove may
be loosened by heating the impeller hub with a torch during the
pulling process to remove the impeller from the motor shaft.
h
Remove mechanical seal from motor shaft
The mechanical seal spring usually comes free with the impel-
ler. The mechanical seal rotating element [seal head]
(62)
must be pried loose with pry bars or screwdrivers, placed under
each side of the seal drive band. Leverage is applied against the
adapter. Once loosened, the seal may be pulled free of
the shaft.
Do not damage the carbon face when removing the rotating
element [seal head]. It may be needed for analysis if seal failure
investigation is required.
i
Remove seal seat from adapter
The stationary seat
(61)
typically O-ring or L-cup mounted
Silicon Carbide material, is pried loose from the recess in the
adapter. If the seat cannot be removed in this manner, remove
the motor cap screws and washers [lock washers]
(43,44)
and separate the adapter
(40)
from the motor
(10)
. A screw-
driver may then be used to push the seat out of the adapter
from the rear.
j
Remove old casing gasket
The former adapter O-ring should be scraped from the adapter,
leaving clean surfaces [groove] for the new O-ring. [A standard
putty knife and wire brush are useful for this purpose].
k
Assembly Procedures:
Replace mechanical seal
•
Clean the shaft stub
(21)
surface, ensuring all the former
seal elastomer pieces have been removed. Inspect for dam-
age. Replace if necessary.
•
Install a new stationary seat
(61)
in the adapter cavity, being
sure the lapped (polished) side of the insert is facing up.
Ensure that the cavity has been thoroughly cleaned. Lubri-
Summary of Contents for Design Envelope 4300
Page 2: ......