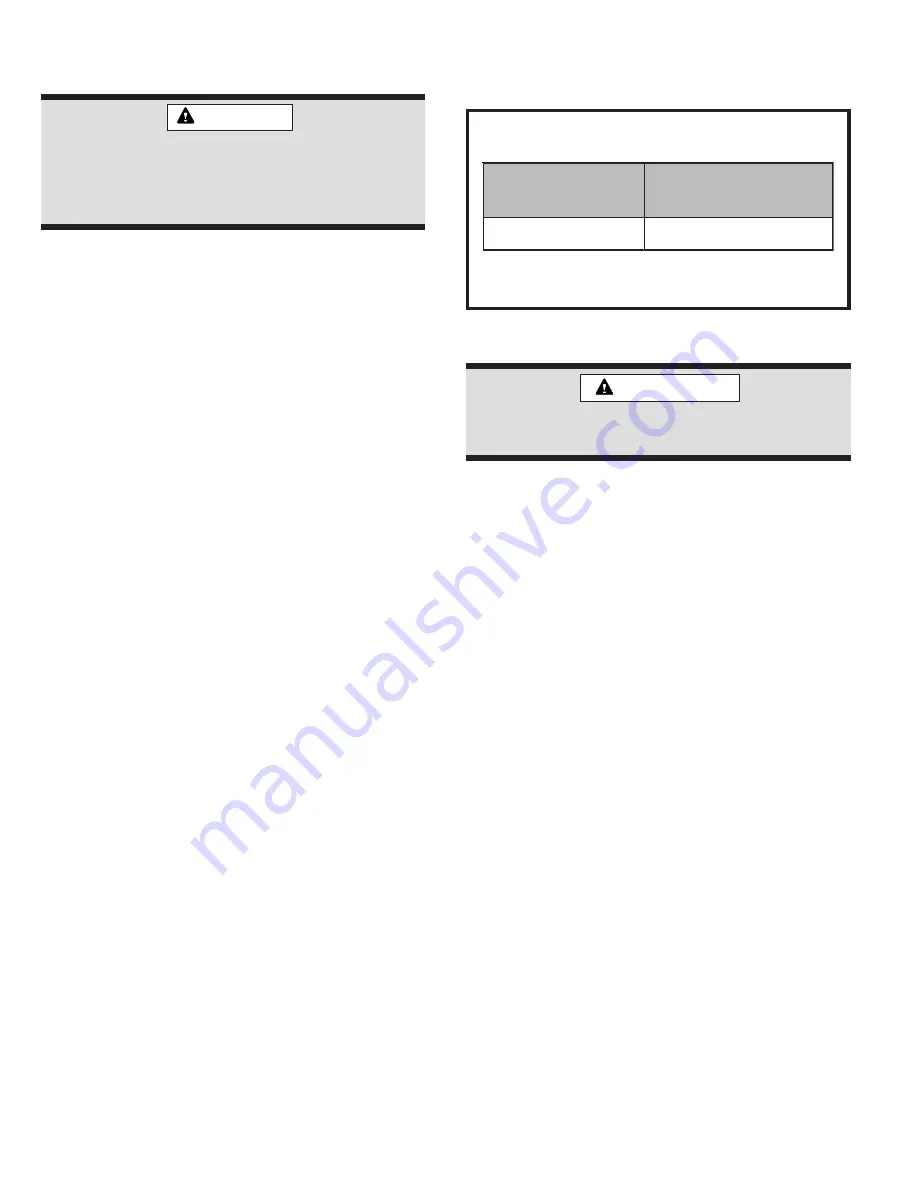
Page 12
# 48478A006
START-UP
1. Rotate fan to check for frozen bearings or binding.
2. Inspect all factory and field-installed wiring for loose
connections.
3. After evacuation is complete, open liquid line and
suction line service valves to release refrigerant
charge (contained in outdoor unit) into system.
4. Replace the stem caps and secure finger tight, then
tighten an additional 1/6 of a turn.
5. Check voltage supply at the disconnect switch. The
voltage must be within the range listed on the unit
nameplate. If not, do not start equipment until the
power company has been consulted and the voltage
condition corrected.
6. Set thermostat for cooling demand, turn on power to
indoor blower, and close the outdoor unit disconnect
switch to start the unit.
7. Recheck unit voltage with unit running. Power must be
within range shown on unit nameplate.
Refrigerant Charging
This system is charged with R410A refrigerant which
operates at much higher pressures than R22. The liquid line
drier provided with the unit is approved for use with R410A.
Do not replace it with one designed for use with R22.
This
unit is NOT approved for use with coils which use
capillary tubes as a refrigerant metering device.
R410A refrigerant cylinders are rose colored. Refriger-
ant should be added through the suction valve in the
liquid state.
Certain R410A cylinders are identified as being
equipped with a dip tube. These allow liquid refriger-
ant to be drawn from the bottom of the cylinder
without inverting the cylinder. Do not turn this type of
cylinder upside down to draw refrigerant.
Units are factory charged with the amount of R410A
refrigerant indicated on the unit rating plate. This charge is
based on a matching indoor coil and outdoor coil with 15'
line set. For varying lengths of line set, refer to Table 4 for
If unit is equipped with a crankcase heater, it
should be energized 24 hours before unit
start-up to prevent compressor damage as a
result of slugging.
CAUTION
Mineral oils are not compatible with R410A. If
oil must be added, it must be a polyol ester oil.
IMPORTANT
refrigerant charge adjustment. A blank space is provided
on the unit rating plate to list the actual field charge.
If the system is void of refrigerant, clean the system using
the procedure described below.
1. Use dry nitrogen to pressurize the system and check
for leaks. Repair leaks, if possible.
2. Evacuate the system to remove as much of the
moisture as possible.
3. Use dry nitrogen to break the vacuum.
4. Evacuate the system again.
5. Weigh the appropriate amount of R410A refrigerant
(listed on unit nameplate) into the system.
6. Monitor the system to determine the amount of
moisture remaining in the oil. Use a test kit to verify
that the moisture content is within the kit’s dry color
range. It may be necessary to replace the filter drier
several times to achieve the required dryness level.
If system dryness is not verified, the compressor
will fail in the future.
The outdoor unit should be charged during warm weather.
However, applications arise in which charging must occur
in the colder months. The method of charging is deter-
mined by the
outdoor ambient temperature
.
Measure the liquid line temperature and the outdoor
ambient temperature as outlined below:
1. Connect the manifold gauge set to the service valve
ports as follows (see Figure 12):
Refrigerant Charge Adjustment
* If line length is
greater than 15 ft.
, add this amount.
If line length is
less than 15 ft.
, remove this amount.
Table 4
t
e
S
e
n
i
L
d
i
u
q
i
L
r
e
t
e
m
a
i
D
t
s
u
j
d
a
.
t
f
5
r
e
p
.
z
O
*
t
e
s
e
n
i
l
.
t
f
5
1
m
o
r
f
.
n
i
8
/
3
.
t
f
5
r
e
p
.
z
o
3