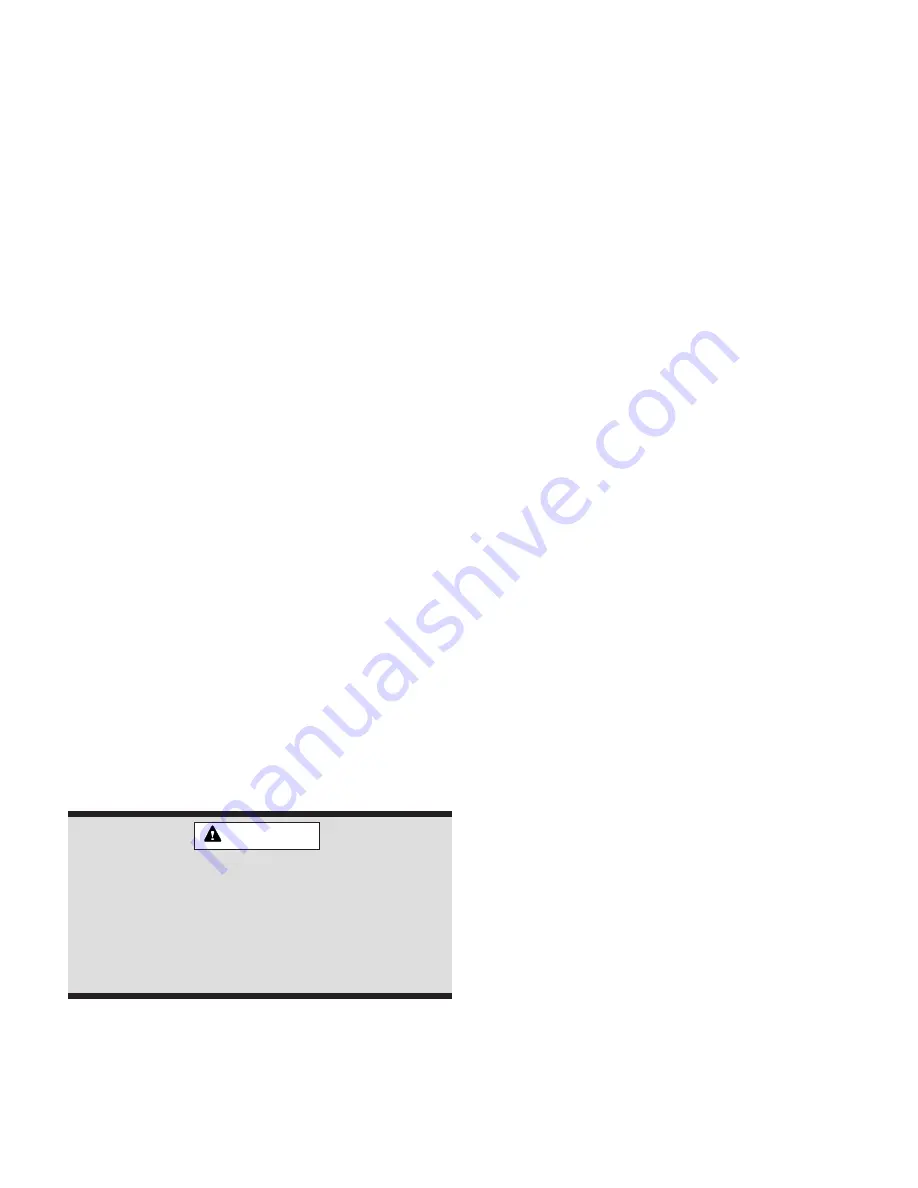
# 48478A006
Page 11
to protect the manifold gauge set from damage
caused by high pressure.)
2. With both manifold valves closed, connect the cylin-
der of R410A refrigerant. Open the valve on the
R410A cylinder (vapor only).
3. Open the high pressure side of the manifold to allow
R410A into the line set and indoor unit. Weigh in a
trace amount of R410A. (A trace amount is a maxi-
mum of 2 oz. of refrigerant or 3 lbs. pressure.) Close
the valve on the R410A cylinder and the valve on the
high pressure side of the manifold gauge set. Discon-
nect the R410A cylinder.
4. Connect a cylinder of nitrogen with a pressure regulat-
ing valve to the center port of the manifold gauge set.
When using high pressure gas such as nitrogen
for this purpose, be sure to use a regulator that
can control the pressure down to 1 or 2 psig.
5. Adjust nitrogen pressure to 150 psig. Open the valve
on the high side of the manifold gauge set to pressur-
ize the line set and the indoor coil.
6. After a short period of time, open a refrigerant port to
make sure that an adequate amount of refrigerant has
been added for detection (refrigerant requirements will
vary with lengths). Check all joints for leaks. Purge
nitrogen and R410A mixture. Correct any leaks and
recheck.
Evacuation
Evacuating the system of noncondensables is critical for
proper operation of the unit. Noncondensables are defined
as any gas that will not condense under temperatures and
pressures present during operation of an air conditioning
system. Noncondensables and water vapor combine with
refrigerant to produce substances that corrode copper
piping and compressor parts.
•
Low pressure gauge to suction line service valve
•
High pressure gauge to liquid line service valve
2. Connect micron gauge.
3. Connect the vacuum pump (with vacuum gauge) to
the center port of the manifold gauge set.
4. Open both manifold valves and start vacuum pump.
5. Evacuate the line set and indoor unit to a minimum of
500 microns or lower. During the early stages of
evacuation, it is desirable to close the manifold gauge
valve at least once to determine if there is a rapid rise
in pressure. A rapid rise in pressure indicates a
relatively large leak. If this occurs, the leak testing
procedure must be repeated.
6. When 500 microns or lower is maintained, close the
manifold gauge valves, turn off the vacuum pump, and
disconnect the manifold gauge center port hose from
the vacuum pump. Attach the manifold gauge center
port hose to a nitrogen cylinder with pressure regulator
set to 150 psig and purge the hose. Open the manifold
gauge valves to break the vacuum in the line set and
indoor unit. Close the manifold gauge valves.
7. Shut off the nitrogen cylinder and remove the manifold
gauge hose from the cylinder. Open the manifold
gauge valves to release the nitrogen from the line set
and indoor unit.
8. Reconnect the manifold gauge to the vacuum pump,
turn the pump on, and continue to evacuate the line
set and indoor unit until 500 microns is maintained
within a 20-minute period after shutting off the
vacuum pump and closing the manifold gauge valves.
9. When the requirements above have been met,
disconnect the manifold hose from the vacuum pump.
Open the service valves to break the vacuum in the
line set and indoor unit.
Do not use a compressor to evacuate a sys-
tem. Avoid deep vacuum operation. Extremely
low vacuums can cause internal arcing and
compressor failure. Danger of equipment
damage. Damage caused by deep vacuum
operation will void warranty.
WARNING
Use a thermocouple or thermistor electronic vacuum
gauge that is calibrated in microns. Use an instrument that
reads down to 50 microns.
1. Connect the manifold gauge set to the service valve
ports as follows: