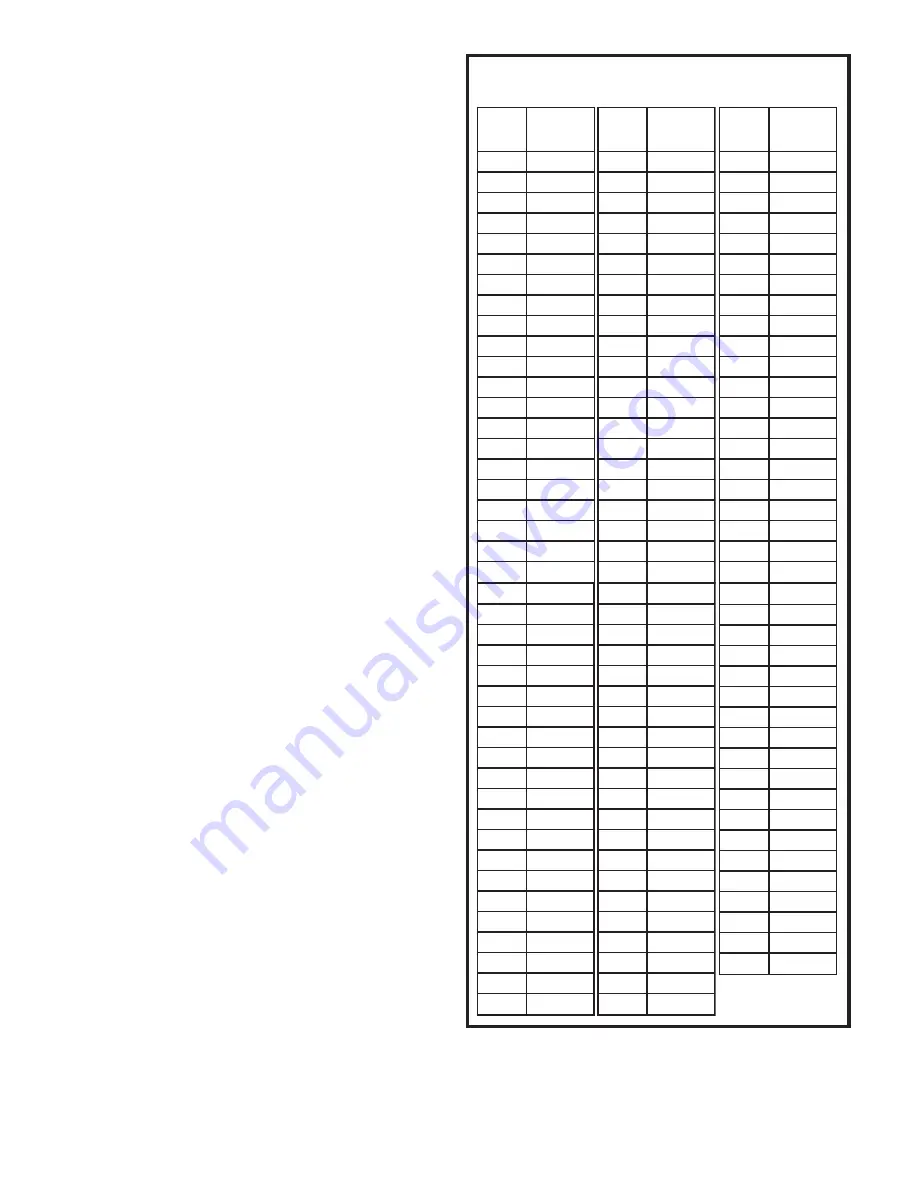
Page 14
# 48387H005
2. Close manifold gauge set valves. Connect the center
manifold hose to an upright cylinder of R410A.
3. If room temperature is below 70°F, set the room thermo-
stat to call for heat. This will create the necessary load
for properly charging the system in the cooling cycle.
4. Use a digital thermometer to record the outdoor
ambient temperature.
5. When the heating demand has been satisfied, switch
the thermostat to cooling mode with a set point of
68°F. When pressures have stabilized, use a digital
thermometer to record the liquid and suction line
temperatures.
6. The outdoor temperature will determine which charg-
ing method to use. Proceed with the appropriate
charging method.
Charge Using Weigh-In Method (Fixed Orifice/TXV
Systems) – Outdoor Temperatures Below 65°F
If the system is void of refrigerant, or if the outdoor ambient
temperature is cool, first locate and repair any leaks then
use the weigh-in method to charge the unit.
1. Recover the refrigerant from the unit.
2. Conduct a leak check, then evacuate as previously
outlined.
3. Weigh in the charge according to the total amount
shown on the unit nameplate.
If weighing facilities are not available or if unit is being
charged during warm weather, follow one of the other
procedures outlined below.
Charge Using Subcooling Method (Fixed Orifice/TXV
Systems) – Outdoor Temperatures 65°F or Above
If charging a fixed orifice or TXV system when the outdoor
ambient temperature is 65°F or above, the subcooling
method can be used to charge the unit.
1. With the manifold gauge hose on the liquid service
port and the unit operating stably, use a digital ther-
mometer to record the liquid line temperature.
2. At the same time, record the liquid line pressure reading.
3. Use the temperature/pressure chart (Table 6) to
determine the saturation temperature for the liquid line
pressure reading.
4. Subtract the liquid line temperature from the satura-
tion temperature (according to the chart) to determine
subcooling.
R410A Temperature/Pressure Chart
Table 6
.
p
m
e
T
F
°
e
r
u
s
s
e
r
P
g
i
s
P
2
3
8
.
0
0
1
3
3
9
.
2
0
1
4
3
0
.
5
0
1
5
3
1
.
7
0
1
6
3
2
.
9
0
1
7
3
4
.
1
1
1
8
3
6
.
3
1
1
9
3
8
.
5
1
1
0
4
0
.
8
1
1
1
4
3
.
0
2
1
2
4
6
.
2
2
1
3
4
0
.
5
2
1
4
4
3
.
7
2
1
5
4
7
.
9
2
1
6
4
2
.
2
3
1
7
4
6
.
4
3
1
8
4
1
.
7
3
1
9
4
6
.
9
3
1
0
5
2
.
2
4
1
1
5
8
.
4
4
1
2
5
4
.
7
4
1
3
5
1
.
0
5
1
4
5
8
.
2
5
1
5
5
5
.
5
5
1
6
5
2
.
8
5
1
7
5
0
.
1
6
1
8
5
9
.
3
6
1
9
5
7
.
6
6
1
0
6
6
.
9
6
1
1
6
6
.
2
7
1
2
6
5
.
5
7
1
3
6
5
.
8
7
1
4
6
6
.
1
8
1
5
6
3
.
4
8
1
6
6
7
.
7
8
1
7
6
9
.
0
9
1
8
6
1
.
4
9
1
9
6
3
.
7
9
1
0
7
6
.
0
0
2
1
7
9
.
3
0
2
2
7
2
.
7
0
2
3
7
6
.
0
1
2
.
p
m
e
T
F
°
e
r
u
s
s
e
r
P
g
i
s
P
4
7
0
.
4
1
2
5
7
4
.
7
1
2
6
7
9
.
0
2
2
7
7
4
.
4
2
2
8
7
0
.
8
2
2
9
7
6
.
1
3
2
0
8
3
.
5
3
2
1
8
0
.
9
3
2
2
8
7
.
2
4
2
3
8
5
.
6
4
2
4
8
3
.
0
5
2
5
8
1
.
4
5
2
6
8
0
.
8
5
2
7
8
0
.
2
6
2
8
8
0
.
6
6
2
9
8
0
.
0
7
2
0
9
1
.
4
7
2
1
9
2
.
8
7
2
2
9
3
.
2
8
2
3
9
5
.
6
8
2
4
9
8
.
0
9
2
5
9
1
.
5
9
2
6
9
4
.
9
9
2
7
9
8
.
3
0
3
8
9
2
.
8
0
3
9
9
7
.
2
1
3
0
0
1
2
.
7
1
3
1
0
1
8
.
1
2
3
2
0
1
4
.
6
2
3
3
0
1
0
.
1
3
3
4
0
1
7
.
5
3
3
5
0
1
5
.
0
4
3
6
0
1
3
.
5
4
3
7
0
1
1
.
0
5
3
8
0
1
0
.
5
5
3
9
0
1
0
.
0
6
3
0
1
1
0
.
5
6
3
1
1
1
0
.
0
7
3
2
1
1
1
.
5
7
3
3
1
1
2
.
0
8
3
4
1
1
4
.
5
8
3
5
1
1
7
.
0
9
3
.
p
m
e
T
F
°
e
r
u
s
s
e
r
P
g
i
s
P
6
1
1
0
.
6
9
3
7
1
1
3
.
1
0
4
8
1
1
7
.
6
0
4
9
1
1
2
.
2
1
4
0
2
1
7
.
7
1
4
1
2
1
2
.
3
2
4
2
2
1
8
.
8
2
4
3
2
1
5
.
4
3
4
4
2
1
2
.
0
4
4
5
2
1
9
.
5
4
4
6
2
1
8
.
1
5
4
7
2
1
6
.
7
5
4
8
2
1
5
.
3
6
4
9
2
1
5
.
9
6
4
0
3
1
6
.
5
7
4
1
3
1
6
.
1
8
4
2
3
1
8
.
7
8
4
3
3
1
0
.
4
9
4
4
3
1
2
.
0
0
5
5
3
1
5
.
6
0
5
6
3
1
9
.
2
1
5
7
3
1
3
.
9
1
5
8
3
1
8
.
5
2
5
9
3
1
4
.
2
3
5
0
4
1
0
.
9
3
5
1
4
1
6
.
5
4
5
2
4
1
3
.
2
5
5
3
4
1
1
.
9
5
5
4
4
1
9
.
5
6
5
5
4
1
8
.
2
7
5
6
4
1
8
.
9
7
5
7
4
1
8
.
6
8
5
8
4
1
8
.
3
9
5
9
4
1
0
.
1
0
6
0
5
1
1
.
8
0
6
1
5
1
4
.
5
1
6
2
5
1
7
.
2
2
6
3
5
1
1
.
0
3
6
4
5
1
5
.
7
3
6
5
5
1
0
.
5
4
6