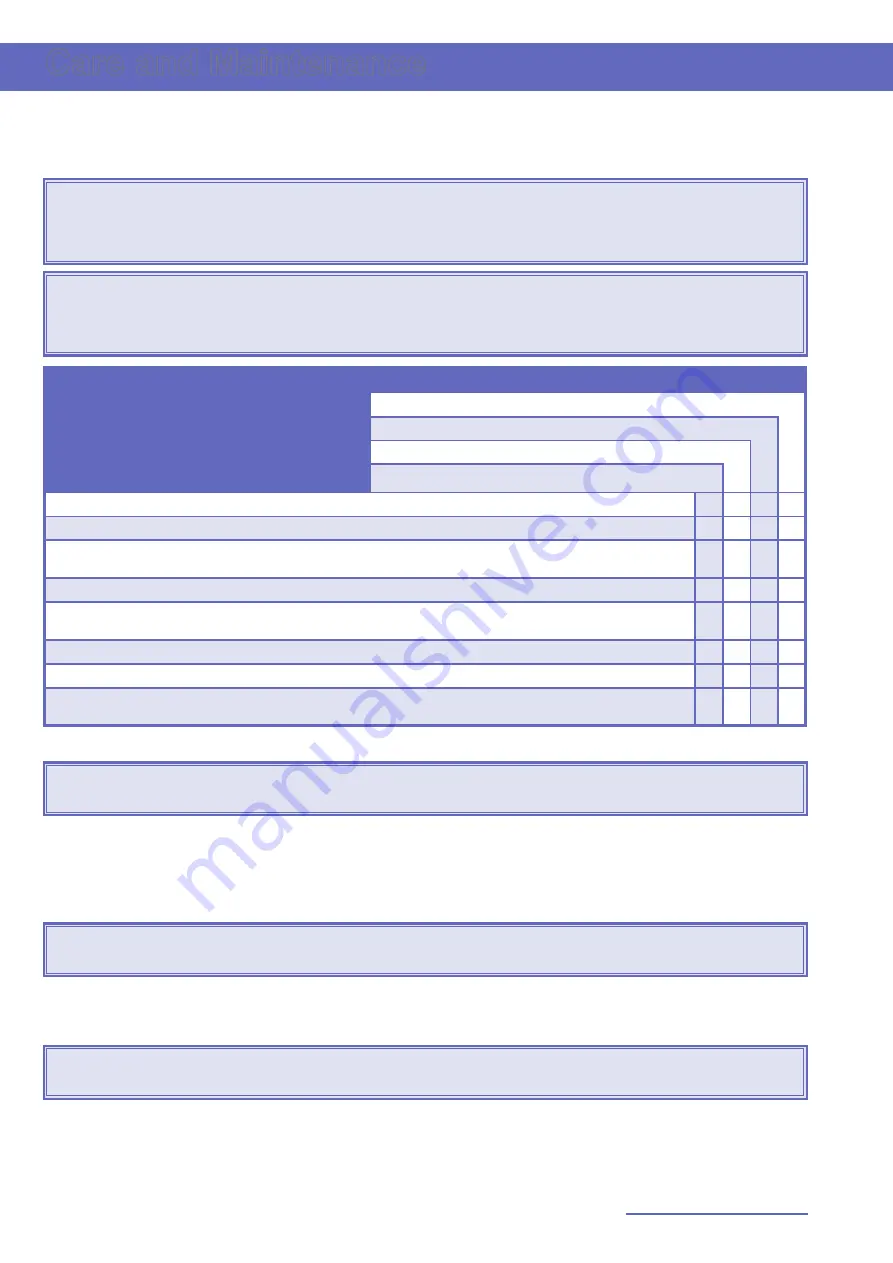
001.10610.EN rev
. 13
Care and Maintenance
16
Care and Maintenance
Preventive Maintenance Schedule
The
EASYTRACK
is subject to wear and tear, and the following actions must be performed when specified
to ensure that the product remains within its original manufacturing specification.
WARNING
: The points on this checklist are the minimum the manufacturer recommends. In some
cases more frequent inspections should be carried out. Continuing to use the
EASYTRACK
without
conducting regular inspections will seriously compromise the user and resident / patient’s safety.
Preventive maintenance specified in this manual can prevent accidents.
WARNING:
Safety related maintenance and authorized service must be carried out by qualified
personnel, fully trained in servicing procedures by Arjo and equipped with correct tools and proper
documentation, including
Parts List
and
Service Manua
l. Failure to meet these requirements could
result in personal injuries and / or unsafe equipment.
POINTS TO BE INSPECTED BY
USER / SERVICE TECHNICIAN
FREQUENCY
Annually / every 1400 transfer / every 50 assembling*
Monthly
Before every use
Before installing
Inspect for evidence of external damage or missing parts.
Ensure all components are in working order.
Using the clip-on level, make sure that all posts are straight. If any post is not straight remove the
track and level post accordingly.
Red mark on top of each post (under the top plate) is not visible.
The tracks are secured in place. Press down on each track to make sure they are locked onto the
posts.
Clean the inside of the tracks to ensure there is no dust or grease build-up inside the tracks.
Check to make sure that the trolleys move freely along the tracks.
Make sure the padding on the foot and top plate is clear of any foreign substance and is not
damaged. Have the paddings replaced accordingly.
* Which ever comes first: Annually - every 1400 patient transfer cycles - every 50 assembling/disassembling cycles.
WARNING
: If any of the above inspection point fails, DO NOT USE the
EASYTRACK
system until
appropriate corrective action is taken.
Annual Inspection by an Authorized Technician
The
EASYTRACK
must be inspected by a qualified Arjo technician on an annual basis to ensure
the proper functioning of its components, as well as the safety of the patients and care givers that
use the
EASYTRACK
. Please contact your local representative to make arrangements.
NOTE
: If the product does not work as intended, immediately contact your local Arjo agent for
support.
Cleaning
To clean the
EASYTRACK
, wipe it down with a damp cloth using warm water and mild detergent.
CAUTION
: Do not use phenol, chlorine or any other type of solvent that may damage the
finish.
To ensure a better rolling surface for the trolley wheels, clean the inside of the track every four
months. To do so, insert a damp cloth in the opening and slide it from one end of the track to the
other.
Summary of Contents for EASYTRACK 9330010
Page 4: ...Page intentionally left blank...
Page 22: ...Page intentionally left blank...