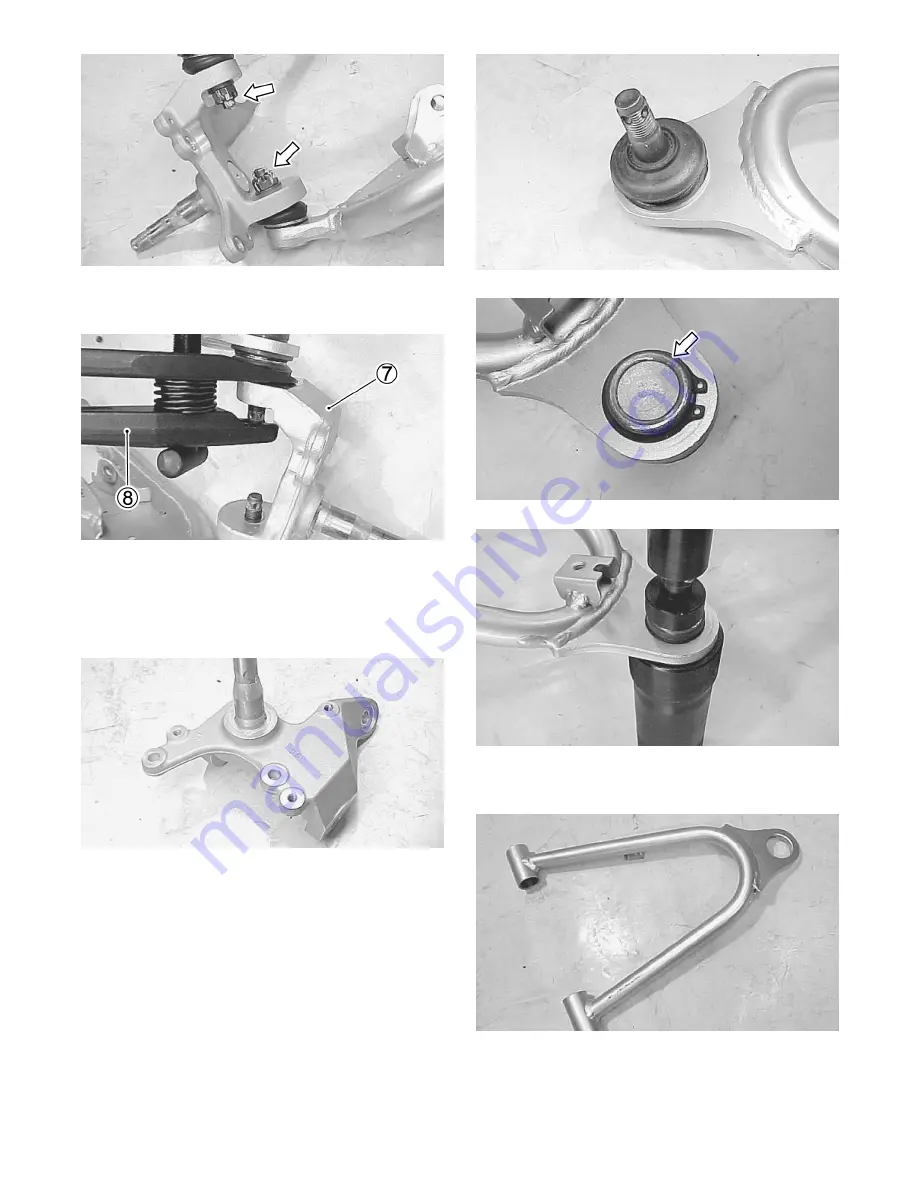
12
SP373
10. Using a ball joint remover (8), remove the ball joint
from the knuckle (7).
SP374
CLEANING AND INSPECTING
1. Clean the knuckle in parts-cleaning solvent; then dry
with compressed air. If any damage or excessive
wear is detected, the knuckle must be replaced.
SP375
2. Inspect the ball joint for boot damage or wear.
Remove the circlip and replace the ball joint if dam-
age is found.
SP376
SP377
SP378
3. Inspect the arm for broken welds, cracks, or bends.
Replace if damaged.
SP379
4. Remove the spacers and dust seals and inspect for
damage to seal lips and spacers.
Summary of Contents for DVX 400 2004
Page 1: ...ATV Service Manual 2004 2004 2004 A A RC C C T T I DVX 400...
Page 15: ...8 ATV2152...
Page 16: ...9 ATV2153...
Page 80: ...9 Oil Flow Chart ATV2180...
Page 89: ...18 NOTES...
Page 103: ...14 WIRING DIAGRAM Harness p n 3509 007 Insert Fold Out 0739 430...
Page 109: ...6 NOTES...
Page 153: ......