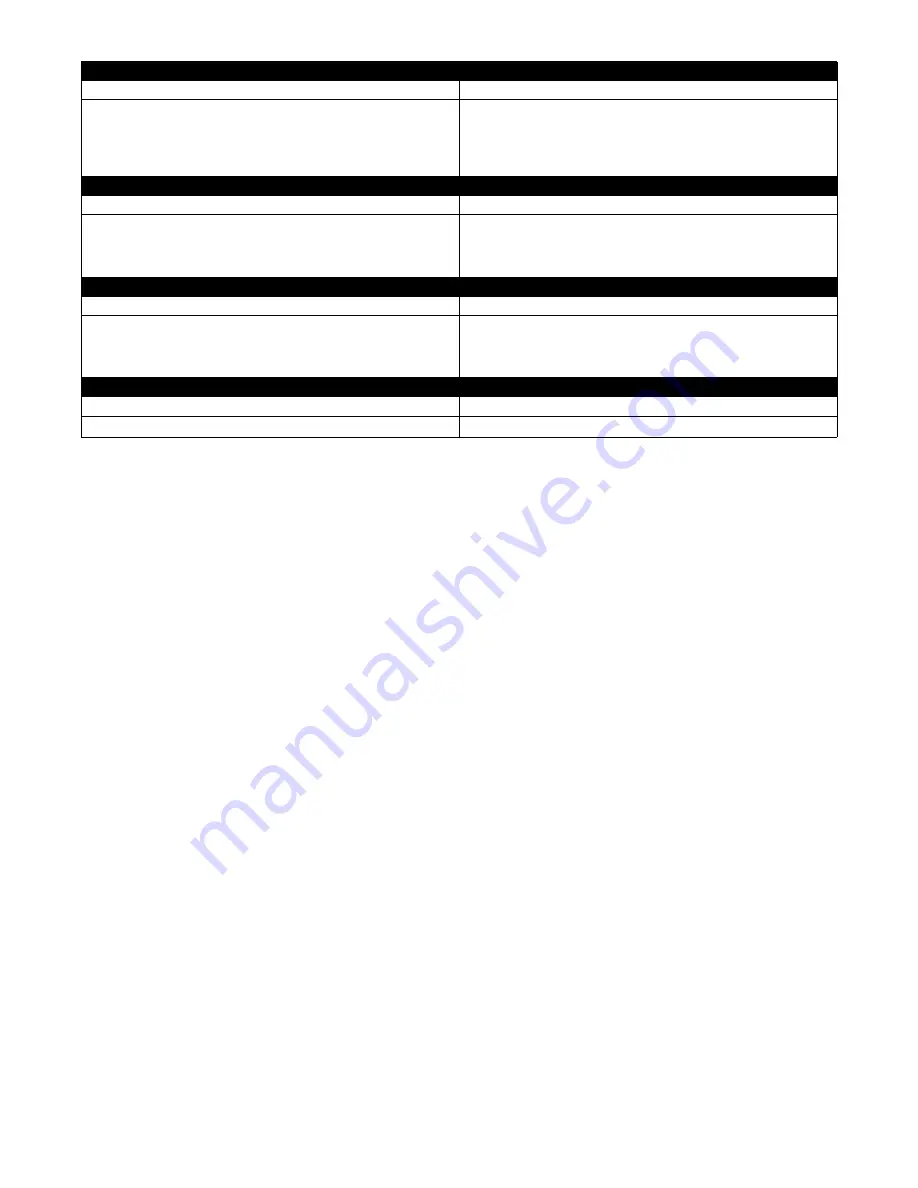
5-14
Problem: Starter button not effective
Condition
Remedy
1.
Battery charge
low
2.
Switch contacts
defective
3.
Starter relay
defective
4.
Emergency stop - ignition switch
off
5.
Wiring connections
loose - disconnected
1. Charge - replace battery
2. Replace switch
3. Replace relay
4. Turn on switches
5. Connect - tighten - repair connections
Problem: Battery “sulfation” (Acidic white powdery substance or spots on surfaces of cell plates)
Condition
Remedy
1.
Charging rate
too low - too high
2.
Battery
run-down - damaged
3.
Specific gravity
too low (lead-acid)
4.
Battery electrolyte
insufficient (lead-acid)
1. Replace battery
2. Replace battery
3. Charge battery - add distilled water
4. Keep electrolyte to prescribed level
Problem: Battery discharges too rapidly
Condition
Remedy
1.
Charging system
not charging
2.
Cell plates
overcharged - damaged
3.
Battery
short-circuited
4.
Specific gravity
too low (lead-acid)
1. Check magneto - regulator/rectifier - circuit connections
2. Replace battery - correct charging system
3. Replace battery
4. Charge battery - add distilled water
Problem: Battery polarity reversed
Condition
Remedy
1.
Battery
incorrectly connected
1. Reverse connections - replace battery - repair damage
FOR ARCTIC CAT ATV DISCOUNT PARTS CALL 606-678-9623 OR 606-561-4983
www.mymowerparts.com