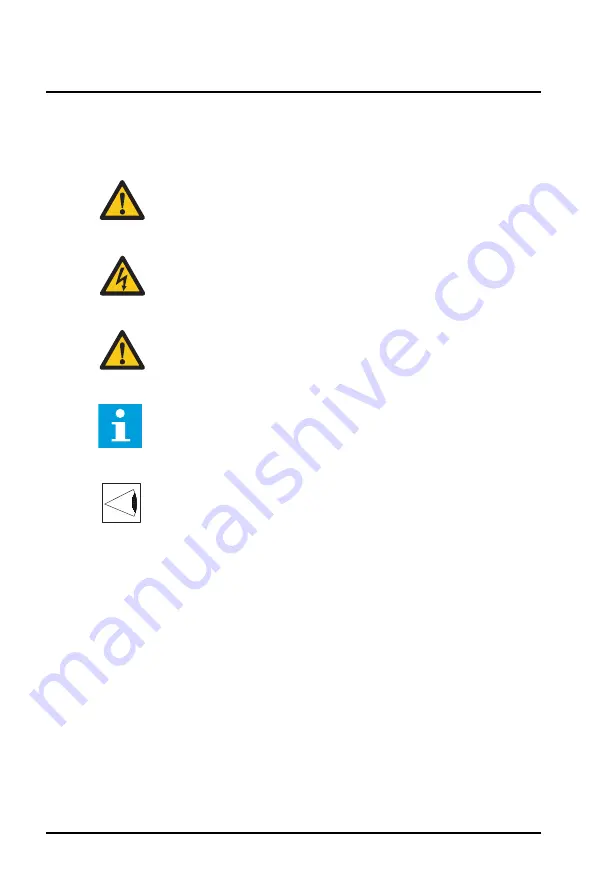
About this manual
User Manual Chemical centrifugal pumps with mechanical seal V080716
6
1.4
Safety symbols and descriptions used in this
manual
/i
WARNING
“Warning” tells you that there is a risk of personal injury or death.
WARNING
“Electrical hazard” tells you that there is a risk of electrical shock.
CAUTION
“Caution” tells you that there is a risk of property damage.
Note
“Note” gives further information.
Do a check.