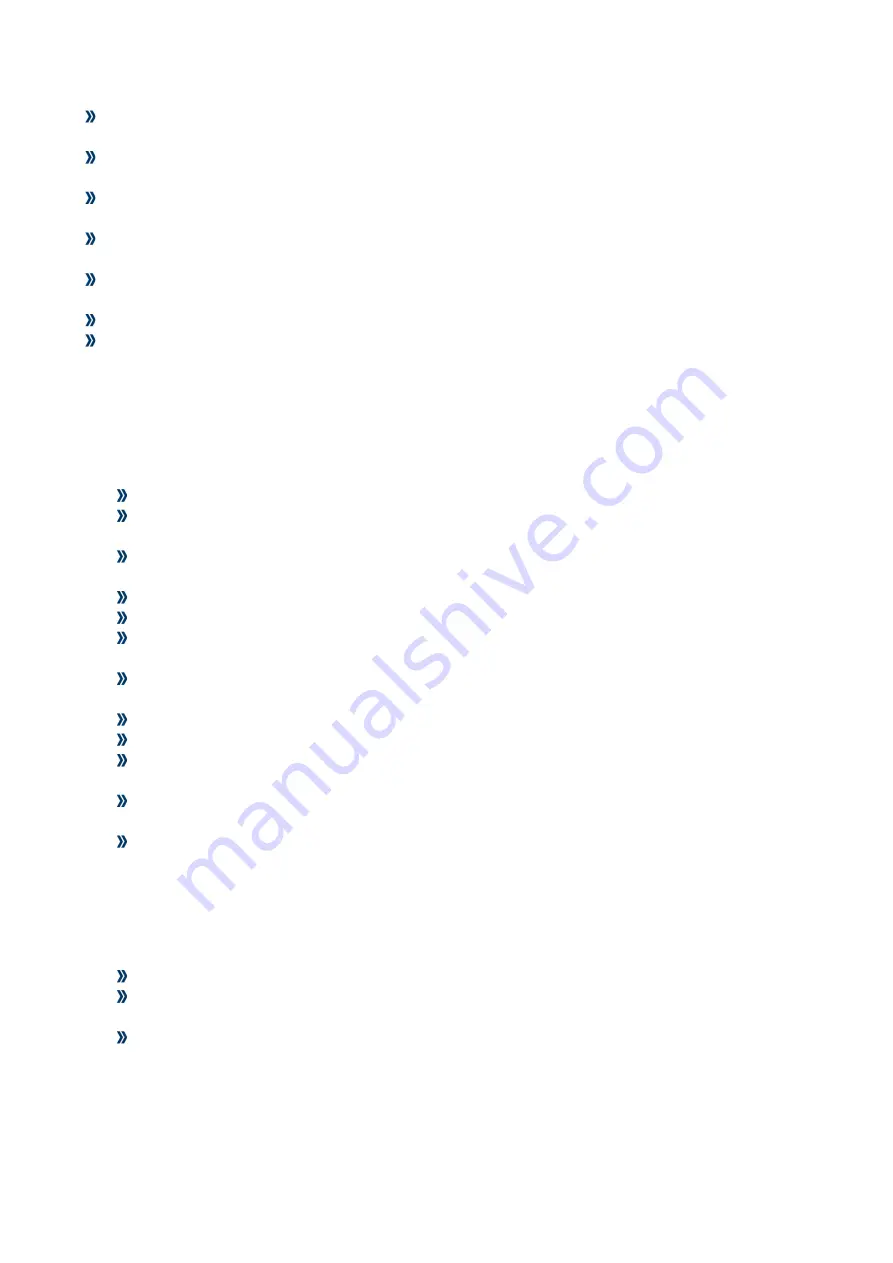
6
VCS - Viscomaster™
3.1.1
Installation checklist
Verify the contents of the product shipment to confirm that you have all parts and information necessary for
the installation.
Verify that the meter calibration-type code corresponds to the pipe size. If it does not, measurement
accuracy may be reduced due to the boundary effect.
Make sure that all electrical safety requirements are met for the environment in which the meter will be
installed.
Make sure that the local ambient and process temperatures and process pressure are within the limits of the
meter.
Make sure that the hazardous area specified on the approval tag is suitable for the environment in which the
meter will be installed.
Make sure that you will have adequate access to the meter for verification and maintenance.
Verify that you have all equipment necessary for your installation. Depending on your application, you may
be required to install additional parts for optimal performance of the meter.
3.1.2
Best practices
The following information can help you get the most from your meter.
Handle the meter with care. Follow local practices for lifting or moving the meter.
If you have an HFVM with calibration code B (viscosity and density calibration), perform a Known Density
Verification (KDV) check of the meter prior to installing the meter.
For the DLC-coated tines, always fit the protective cover over the tines when the meter is not in use. The
tine coating is not resistant to impact damage.
Always store and transport the meter in its original packaging.
Do not use liquids that are incompatible with the materials of construction.
Do not expose the meter to excessive vibration (greater than 0.5 g continuously). Vibration levels in
excess of 0.5 g can affect the meter accuracy.
For optimal performance of the meter, ensure that operating conditions correspond to the meter
calibration-type code and boundary.
Ensure that all piping connections conform to the local and national regulations and codes of practice.
Follow fluid velocity guidelines and install the tines vertically for side insertion.
Properly tighten the transmitter housing cover after wiring to maintain ingress protection and hazardous
area approvals.
After installation, pressure test the meter and the associated pipework to 1½ times the maximum
operating pressure.
Install thermal insulation in the meter, the inlet, and the bypass-loop pipeline to maintain stable
temperatures. The thermal insulation should cover the process connection.
3.1.3
Power requirements
Following are the DC power requirements to operate the meter:
24 VDC, 0.65 W typical, 1.1 W maximum
Minimum recommended voltage: 21.6 VDC with 1000 ft of 24 AWG (300 m of 0.20 mm
2
)
power-supply cable
At startup, power source must provide a minimum of 0.5 A of short-term current at a minimum
of 19.6 V at the power-input terminals.
Summary of Contents for Viscomaster
Page 35: ...VCS Viscomaster 35 ...
Page 36: ...36 VCS Viscomaster ...
Page 37: ...VCS Viscomaster 37 For connection with external power supply controller and sensor passive ...
Page 38: ...38 VCS Viscomaster ...
Page 39: ...VCS Viscomaster 39 ...
Page 47: ...VCS Viscomaster 47 ...