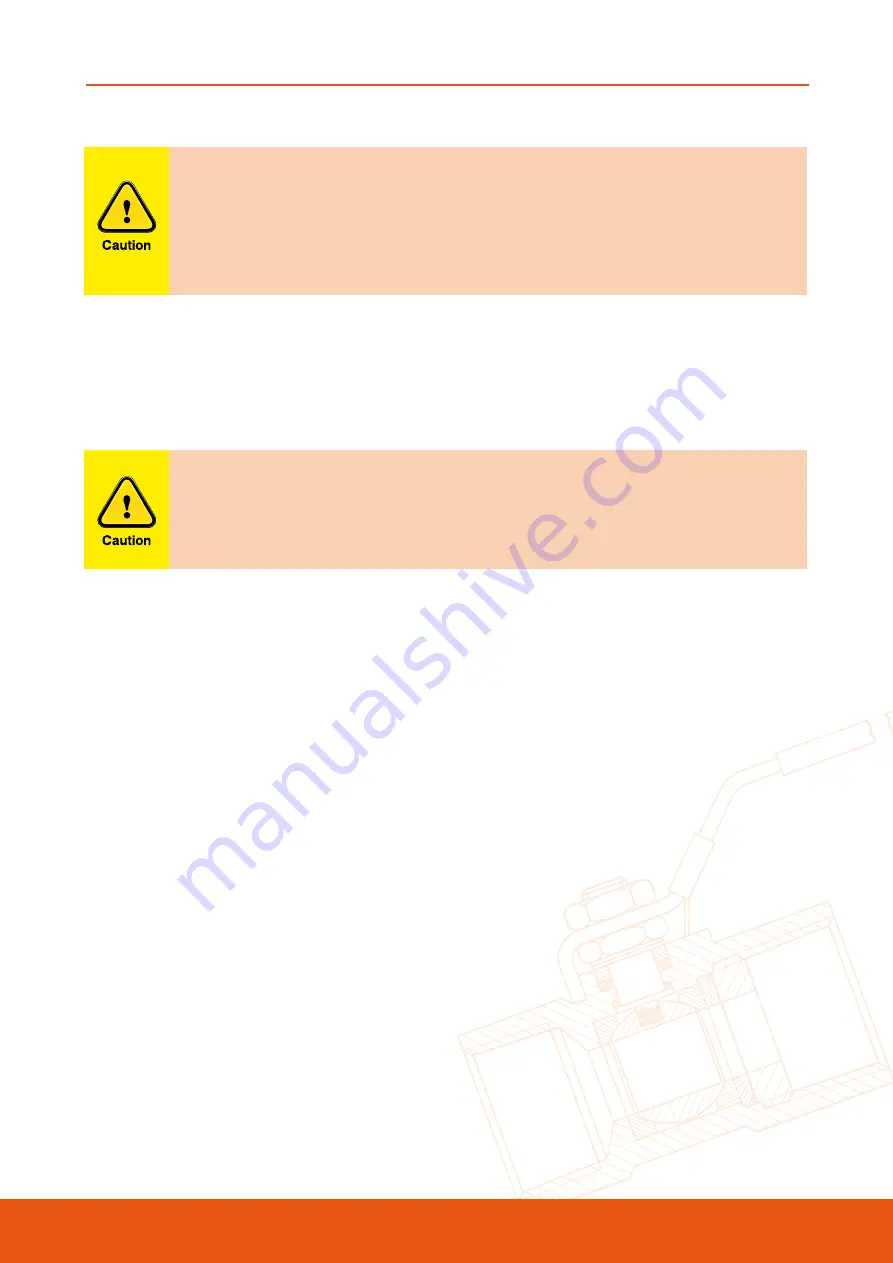
BALL VALVES - FS900 SERIES
Australian Pipeline Valve - Installation, Operation and Maintenance Manual
9
Personal injury may result from sudden release of any process pressure. APV
recommends the use of protective clothing, gloves and eye wear when performing
any installation or maintenance. Isolate the valve from the system and relieve
pressure prior to performing maintenance. Disconnect any operating lines providing
air pressure, control signals or electrical power to actuators.
4.2 BODY SEAL
Sealing between three body segments is provided by a friction fit retainer and a gasket (Teflon or
graphite). Ensure thread is undamaged and body pocket around gasket is clean and free from scratches
or damage.
If a gasket seal is distrubed while removing or adjusting gasketed parts, APV
recommends installing a new gasket while reassembling. A proper seal is required
to ensure optimum operation.
4.3 INSPECTION AND REPLACEMENT OF TRIM COMPONENTS
Disassembly: -
1. Place the valve in the half open position, remove all pressure and drain the system. Make sure that
leakage of any residual material is caught in an appropriate container and disposed of properly.
2. Remove the nut fastening the lever. Remove the lever. Remove the retainer/lock nut/washer and the
stop plate.
3. Follow disassembly procedure 4.4 below.
4. Remove the ball from the body. Inspect the surface of the ball for any scrapes or damage.
a. The cause of the problem such as dirt, fluid, etc must be rectifed to avoid further damage.
b. If imperfections are found on the contacting area of the ball and ball seat the ball must be taken for
fine milling. If heavily damaged, then it will need to be welded and re-machined or the ball
replaced completely. If the scraped area damage is elsewhere, it too must be fine milled to avoid
the ball heavily damaging the soft seat during the open and close operation.
c. Remove the seat from the body. Inspect the seat for any scrapes, concaves, dust (including welding
dregs, iron bits, sands, etc) and abrasion damage. Typically the damage will occur at the same time
the ball is damaged and is the leading cause of leakage. If leakage occurs before repairing, replace
the seat (PTFE or RPTFE).
d. If marks from press or fine scrapes are found during abnormal operation pressure, consider the
right choice of valve.
5. Remove the stem and thrust washer from the body. Remove the thrust washer from the stem. Check
the stem for any damage.
6. Clean and inspect body and retainer gasket surfaces. Check for erosion, corrosion, or damage,