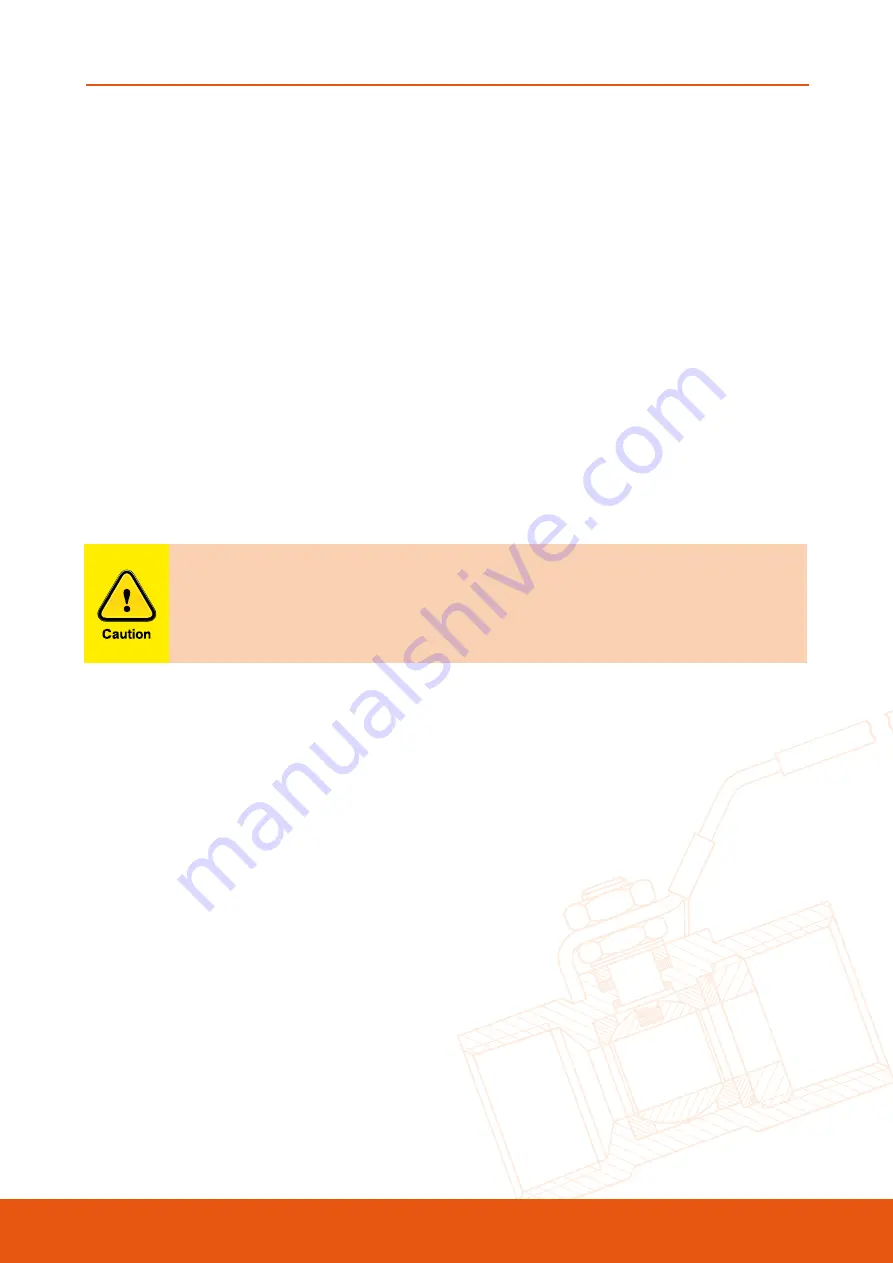
BALL VALVES - FS900 SERIES
Australian Pipeline Valve - Installation, Operation and Maintenance Manual
5
1.3 PREPARATION
a) Remove the valve end protection.
b) Prior to shipment, a preservative/corrosion inhibitor may have been applied to the inner body of the
valve. This preservative/corrosion inhibitor can be removed with a solvent provided the solvent used
does not affect the seats/seals used in the valve.
c) The inside of the valve should be inspected and blown out with compressed air. Adjacent piping must
be clean and free from debris to prevent damage to the valve.
d) To prevent valve distortion, inefficient operation or early maintenance problems, support piping on
each side of the valve.
e) Make sure the valve is positioned such that there is sufficient space so that the hand lever is easily and
safely reached and there is enough clearance for the stem when the valve is open.
f) Install the valve according to the flow indicator on the valve body where applicable.
2 . 0 I N S T A L L A T I O N
Piping should be properly aligned and supported to reduce mechanical loading on
end connections. Never use the lever (wrench) to hold the valve during transport,
handling or assembly.
The following procedure is required to be followed for correct installation.
a) Before installation confirm the marking (rating, size and material) on the valve body and name plate.
Ensure the valve is suitable for the service which it is being used.
b) Before installation check internal ball/seat retainer is tight.
c) Remove valve end protectors and ensure threads are free from damage. Check packing gland nut is
tight.
d) Prior to installation of valve, ensure the line is completely flushed to remove any debris as soft seated
ball valves are easily damaged. Filters or strainers should be installed upstream to protect soft seated
valves.
e) Valves will operate at any angle horizontally or vertically, although it is recommended you install
valves in a vertical position with stem pointing upwards for ease of operation, inspection and
accessibility.