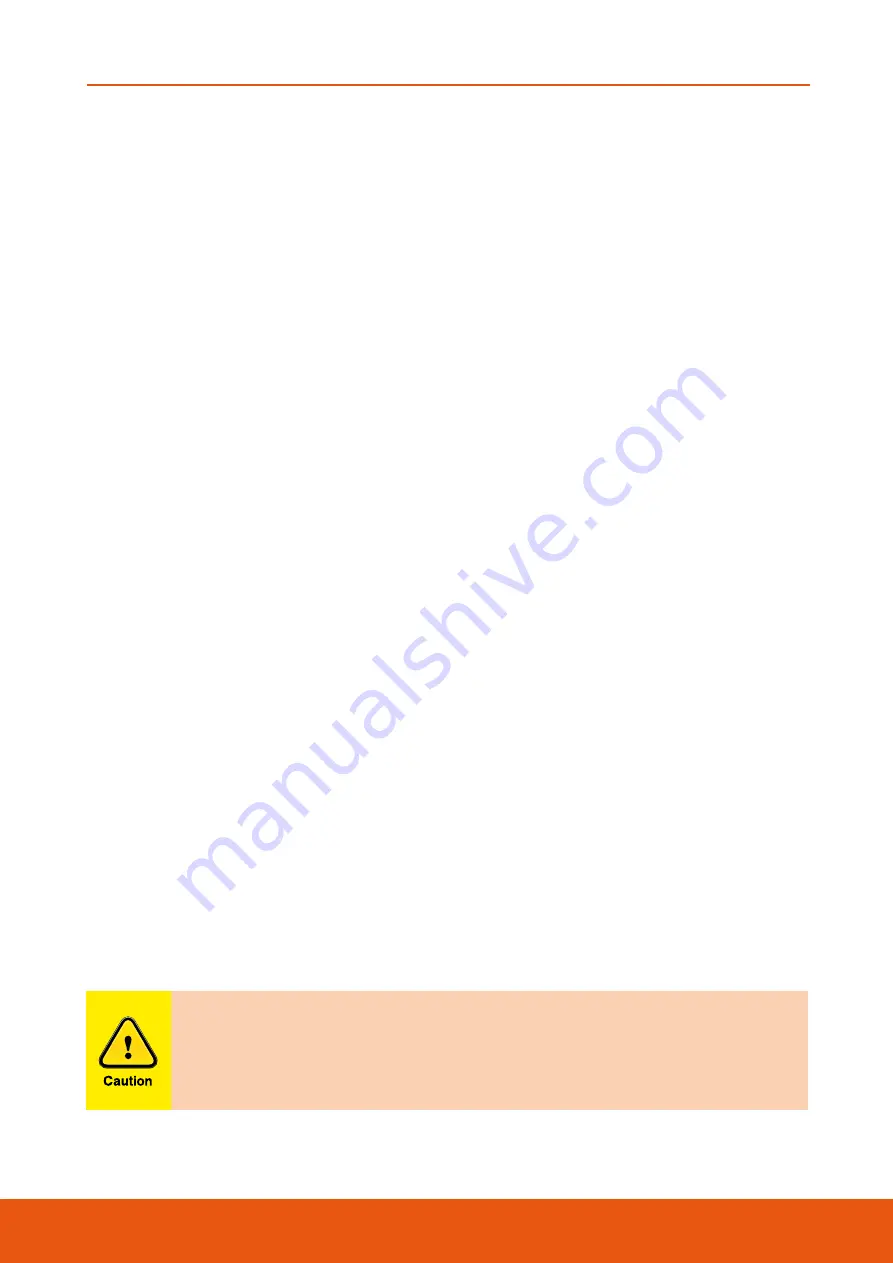
Australian Pipeline Valve - Installation, Operation and Maintenance Manual
10
BALL VALVES - FS900 SERIES
especially near point where leakage occurred. If damage is found, those surfaces must be repaired
before continuing.
7. Replace or repair all damaged parts.
Reassembly: -
1. Installation of new seats, packing and thrust washer is recommended, then follow reassembly
procedure 4.5 below.
2. Install stop plate.
3a. Install retainer/thrust washer.
3b. Install lever.
3c. Install belleville washer and tighten the gland nut.
3. To complete the reassembly, operate the valve 10 times through open and close cycles to ensure all the
parts are assembled correctly and the torques are the same value during the open/close operations. If
torques are not the same during operation this could indicate that some parts have not been correctly
positioned during installation causing interference. Allowing the vale to operate in this state on a
pipeline under higher pressure would only cause more damage. The unit must be dismantled and
re-assembled, then cycled & tested with perfect result.
4.4 DISASSEMBLY PROCEDURE
Before removing valve from line ensure valve is in the closed position and line is fully closed off and
drained. Client should observe all industry & regulatory procedures in this process. To disassemble first
remove the operator (4.3.2) then the following steps should be followed with reassembly in reverse
order.
1. Drain & clean valve including contents in cavity.
2. Remove (unscrew) retainer nut.
3. Remove body gasket.
4. Carefully remove ball. Avoid scratching ball surface.
5. Remove seats.
6. Remove stem nut, lever, gland nut, stopper, spring washer, and gland retainer.
7. Remove stem by pulling from inside body cavity.
8. Remove thrust washer.
9. Remove gland packing.
4.5 REASSEMBLY PROCEDURE
Check the packing box for pressurised process fluids even after the valve has been
removed from the pipeline, particularly when removing packing hardware or
packing rings, or removing packing box pipe plug.