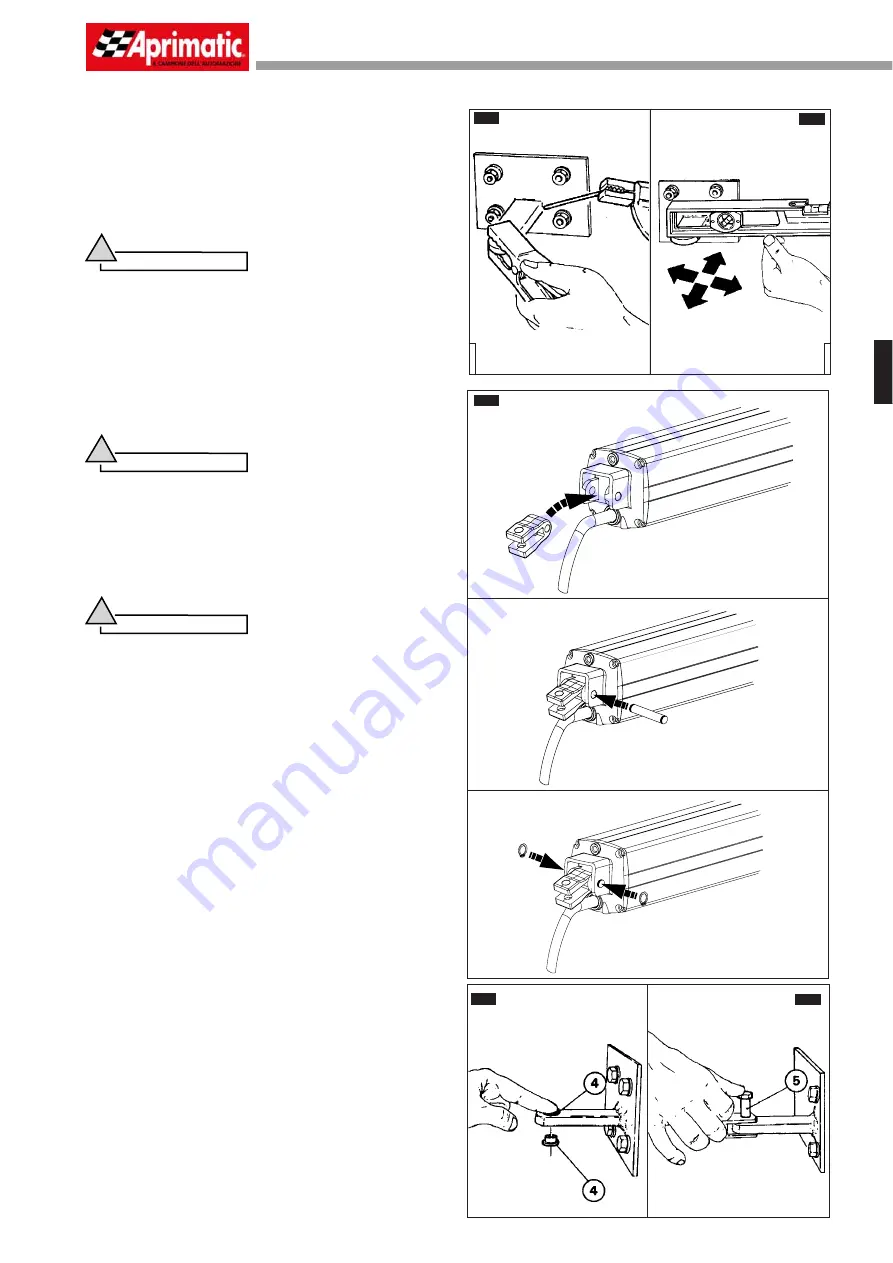
-
21
-
English
AP030017
AP030016
C9
C10
C12
C13
Installation
4.2 FIXING THE REAR OPERATOR MOUNTING
Position the rear mounting (
B4
pos.
4
) at the height previously
measured and weld it on the anchorage plate with two weld points
(
C9
).
Check the lengthwise and crosswise alignment of the mounting
(
C10
) with a water level.
Complete the welding and clean away the residues with a wire
brush.
Warning
!
•
Before welding, ensure that there are no bushes (B4 pos. 5)
in the mounting, and that the fi tting hole is properly protected
from weld residues.
• When the welded zone has cooled down, apply a coat of
anti-rust paint.
4.3 TEMPORARY INSTALLATION OF THE
OPERATOR
Temporarily mount the operator to fi nd the correct fi xing position
of the front mounting.
Warning
!
Handle the operator with care during assembly.
Fit the fork (
C11
pos.
1
) to the operator bottom. Lock the fork with
the special pin (
C11
pos.
2
) and fi x both with the two snap rings
(
C11
pos.
3
).
Fit the two vibration damping bushes (
C12
pos.
4
) above and below
the mounting.
Position the fork of the operator on to the mounting and lock it with the
vertical pin (
C13
pos.
5
) after greasing abundantly.
Warning
!
Grease both the pin and the housings abundantly.
C11
1
2
3
3