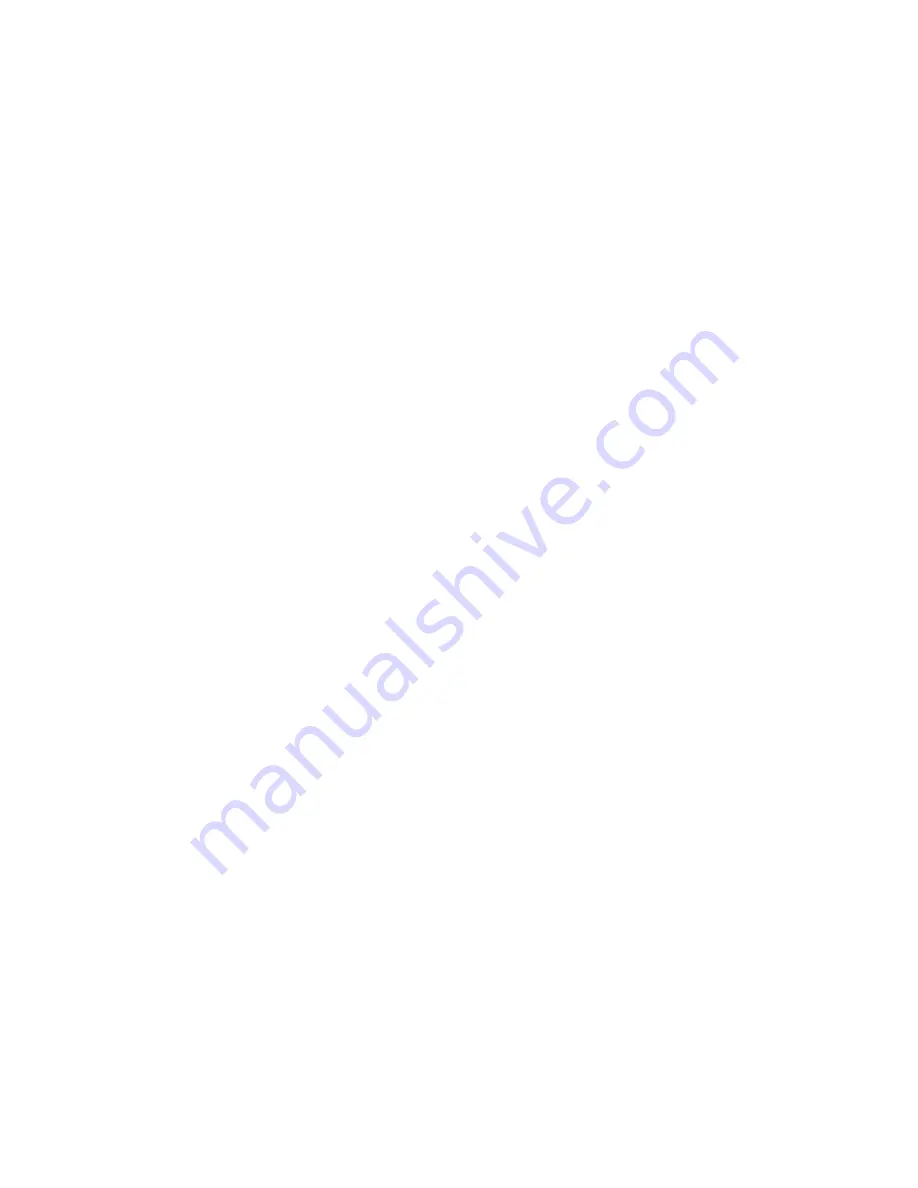
The Bambino® and The Transformer® Operation Manual
Updated 5/4/2021
23
© Apeks LLC, 2019
xii.
Clean the orifice by soaking it in alcohol and blowing it out with compressed air. Verify the orifice is
clear by looking through it.
xiii.
A stainless steel wire brush is available on the online store for stubborn clogs.
xiv.
Reassemble the orifice.
xv.
Replace the separator cap and tighten the clamp bolts per Section 2.7.
xvi.
Reinstall the CO
2
connections and the thermocouple wire.
xvii.
Close Valve 10.
xviii.
Press the pop up message button when orifice is reinstalled, the high pressure clamps are tight and the
flexible hoses are reconnected.
4.4.
Low Separator Pressure
Low separator pressure is typically caused by one of two things (an orifice clog or the wrong size orifice). If the
system has lower than normal separator pressure or does not seem to equalize this may be an indication of a
clogged or partially clogged orifice. To correct an orifice clog refer to the instructions in section 4.3 (Extractor
Overpressure).
4.5.
Wrong Orifice Size
Orifice size dictates the relationship between the separator and extractor. The main goal is to maintain the
separator pressure around 350psi. While the system may run at higher or lower pressure just fine, CO
2
flow may not
be optimal with lower pressures or you may be at risk for more carryover with higher pressures. The smaller the
orifice size the lower the separator pressure and vice versa. Two orifice sizes are shipped with each machine and
additional sizes for any specific optimization are available on the online store. See Section 4.3 (i-xviii) to change
orifices.
4.6.
Differing Separator Pressures
Large variations of separator pressure means there is a clog in the tubing between the two separators since they
should be around the same pressure (+/- 10psi). To check for obstructions, follow the service separator instructions
in Section 4.3 (i-xviii) and check tubing.
4.7.
Oil Carryover to Separator #2 or Filter Housing
Oil carryover can be detected during every maintenance run when cleaning the Separator #2 outlet to pump inlet
and when spot checking Separator #2. Light carryover can/will occur. The presence and severity of oil is an indication
of carryover to the pump. While slight oil can be tolerated, the pump was not designed to have oil circulating
through it. Oil carryover will reduce the life of the pump and can damage the pump if severe. If a large amount of
carryover is detected (more than a couple grams) check the following items during the next run:
i.
Separator temperatures are above 40
o
F after system is equalized, usually after 1 hour after initialing.
The temperature set point on the chiller has a direct relationship with separator temperature. Turn the
set point on the chiller down until separator temperature is below 40
o
F.
ii.
Extremely cold temperatures in separators cause oil carryover as well. If the separator is encased in a
block of ice the temperature is more than likely too cold. Ensure that the chiller is on and correctly
functioning before beginning a run, water lines are correctly assembled between the collector cup and
the separator, and the water line quick connects have disengaged the check valves.
iii.
For both cases check water line connections, chiller settings and water to propylene glycol
percentages.