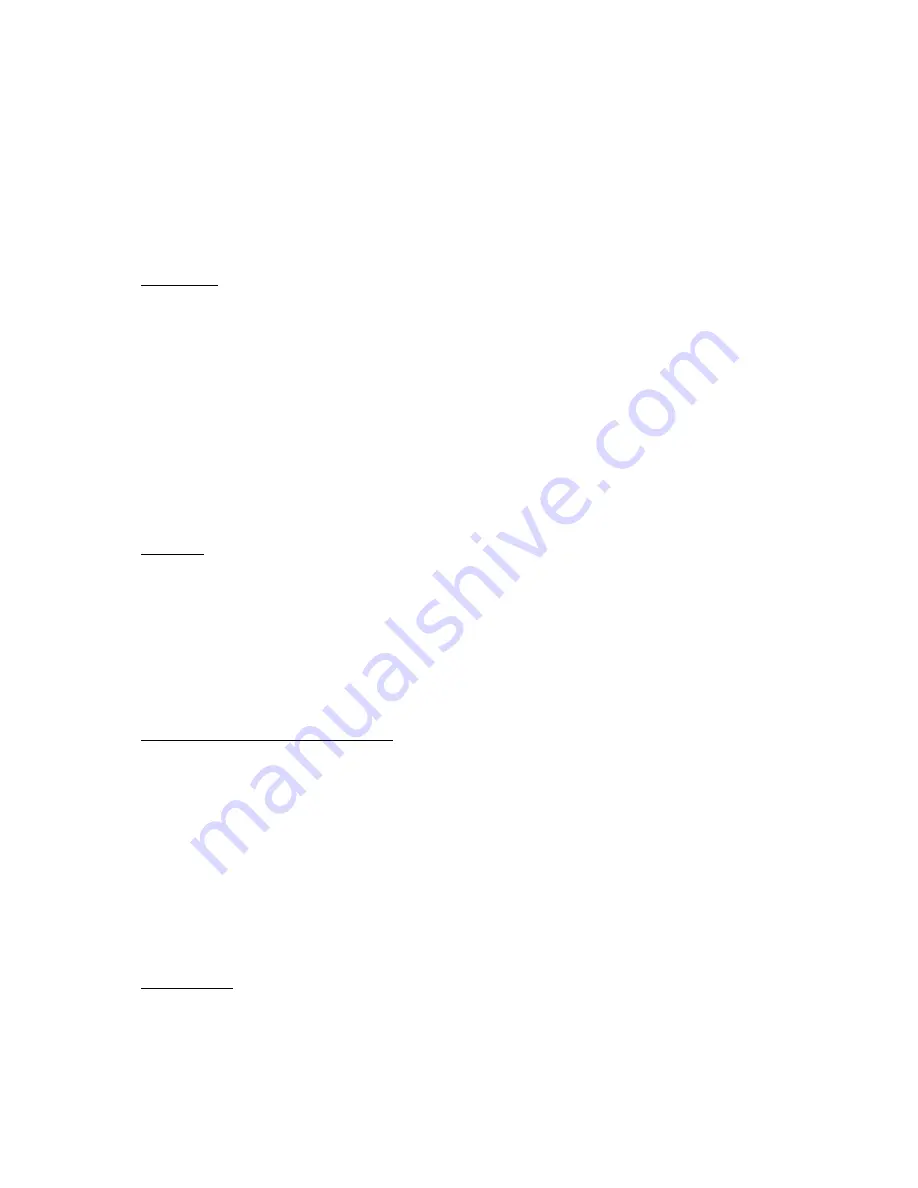
You can desolder the motor from the ESC and test each phase (wire windings inside the
motor) in turn to see if they have a short to the stator (the bit of the motor that the wires
come out of which stays stationary when on the quad) to determine if there is a short
circuit. There should
never
be one. If a motor spins freely at all then it will probably be
good, a brushless motor is usually a remarkably robust piece of technology but it is still
prone to poor workmanship, abuse and overloading, so it is still worth testing.
Fourth test
To proceed further you need to remove the motor from the chassis (4 screws holding it in
underneath). Then unscrew the screws holding in the Electronic Speed Controller, the little
circuit board in the picture above. Once this is done you need to desolder the motor from
the esc if not already done, completely removing it from the quad.
Take the motor and put the screw end (rotor shaft) in the chuck of the drill and while
holding the end of the motor that the wires come out of so that it should stay stationary,
run it up to speed for a couple of minutes making sure the wires do not connect to each
other, isolate with a little white electrical tape and labelling them A, B, C. What you are
looking for here are two things, sound and heat, the motor should be more or less silent,
just a gentle whirring noise or whistle with virtually no heat as it is not under load. If there
is either of these it’s usually a mechanically dead motor and needs replaced.
Fifth test
While still on the drill, again spin it up to full speed then use your multimeter on the (highest
range first if not an autoranging meter then work your way down the ranges until you see a
reading) VAC setting, test the voltage output across each phase in turn.To do this keep the
three wires isolated from each other labeled A, B, C. Connect the meter to the bare wires of
A and B. Take note of the AC voltage. Then repeat this test on wires labeled B and C then
wires labeled A and C. All three readings should be pretty much the same, providing your
drill is running at the same speed on all tests. If not, then dead motor. Needs replaced.
Sixth test, no multimeter (optional)
If you do not have access to a multimeter (I strongly suggest buying one) then you can try
swapping out the motor for the diagonally opposite one. E.g. Clockwise for clockwise motor
to see if this works. This means desoldering and soldering the
good
motor back where the
suspected bad one was. This way if you have to buy and fit a new motor you do not have to
do this process twice. Spin the motors up to idle and see if there is any change.
Please note:
Every time you desolder from a PCB (Printed Circuit Board) you run the risk of delaminating
or lifting the copper circuit, this should only be attempted a limited number of times as it
will, eventually, destroy the board, also this has to be done using the like-for-like motors as
they are designed to run in one direction only.
Seventh test.
So the more probable cause is with the ESC, this is a much more fragile part.
Unfortunately there is no real home test for this other than a visual inspection for charring
caused by overload (just compare it to a known good one, it should be identical) checking
for poor solder joints or just swapping it out, it is just that complicated. If you want to do