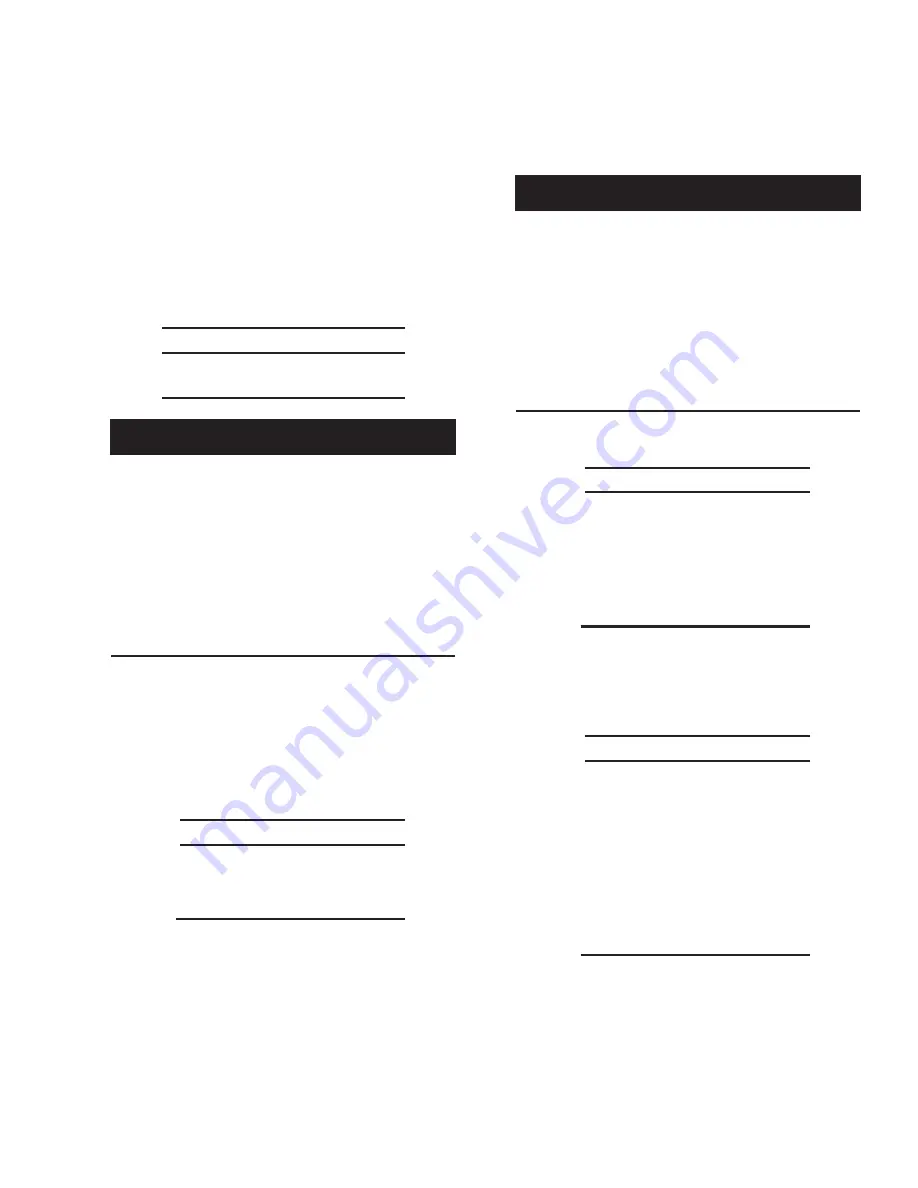
To prepare the ANSUL suppressing/securing system for
placement in service:
1. Remove all cord, wrapping, and banding ties. Examine entire
system and component parts for concealed shipping damage
before placement or securement on site.
2. Make certain hose is in place on support and nozzle is ring
pinned and sealed to nozzle holder with triggers forward in the
closed position.
3. Confirm the dry chemical tank is completely dry before adding
dry chemical to tank. Fill the dry chemical tank by completing
the following steps:
NOTICE
Certain dry chemical systems are filled
before shipment.
Be careful when removing fill cap(s) as tank(s) may be pres-
surized.
• If fill cap has a red indicator stem in the up position, pres-
sure must be relieved from tank.
• If fill cap vent starts relieving pressure while opening the fill
cap, stop and let all pressure vent before removing cap.
• If fill cap is difficult to remove, pressure must be relieved
from tank.
Refer to page 4, steps 1 - 5 to confirm tank pressure is
released. Attempting to remove fill cap when tank has pres-
sure could result in personal injury or damage to property.
a. Remove fill cap and place funnel in opening.
b. Fill tank to rated capacity with
only
the ANSUL dry chemi-
cal specified on the nameplate. ANSUL dry chemical
should not be more than 6 in. (152 mm) from bottom of fill
opening.
c. Clean fill opening threads and gasket seating surface.
(Make certain gasket is in place before reinstalling fill cap.)
d. Secure fill cap and hand tighten.
NOTICE
If the fill cap is an indicator model, be
sure the red indicator stem is in the
DOWN POSITION before securing fill
cap.
4. Fill the ANSULITE AFFF solution tank by completing the fol-
lowing steps:
Be careful when removing fill cap(s) as tank(s) may be pres-
surized.
• If fill cap has a red indicator stem in the up position, pres-
sure must be relieved from tank.
• If fill cap vent starts relieving pressure while opening the fill
cap, stop and let all pressure vent before removing cap.
• If fill cap is difficult to remove, pressure must be relieved
from tank.
Refer to page 4, steps 1 - 5 to confirm tank pressure is
released. Attempting to remove fill cap when tank has pres-
sure could result in personal injury or damage to property.
a. Remove fill cap and fill tank one-half full with fresh potable
tap water.
NOTICE
Tyco Fire Protection Products recom-
mends that the quality of the tap water
be examined each time the system is
charged (see Field Inspec
tion Manual
(Part No. 31274) at the back of this
manual). The quality of the water should
be noted on the Field Inspection
Record.
b1. 6% SOLUTION: Place funnel in fill opening and pour 2 gal
(7.6 L) of only ANSULITE AFFF (Aqueous Film-Forming
Foam) 6% Concentrate into tank.
b2. 3% SOLUTION: Place funnel in fill opening and pour 1 gal
(3.8 L) of only ANSULITE AFFF 3% Concentrate into tank.
NOTICE
Prior to adding the concentrate to the
tank, its refractive index should be mea-
sured and recorded on the Field
Inspection Record, along with a refrac-
tive index vs. concentration curve. The
pro ce dures for these operations are
covered in the Field Inspection Manual
(Part No. 31274) at the back of this
manual. It is also recommended that the
batch numbers from the ANSULITE
AFFF pails be recorded for future refer-
ence.
c. Submerge hose and fill remainder of tank to within 3 in.
(76 mm) from bottom of fill opening, reducing rate of water
flow as tank becomes full.
d. Stir solution for 30 seconds using a non-metallic rod.
e. Clean fill opening threads and gasket seating surface.
!
CAUTION
!
CAUTION
ASSEMBLY
2012-MAR-22
REV. 01 PAGE 1
ANSUL Fire Suppression/Securing Systems
Operation and Maintenance – Model 100/30