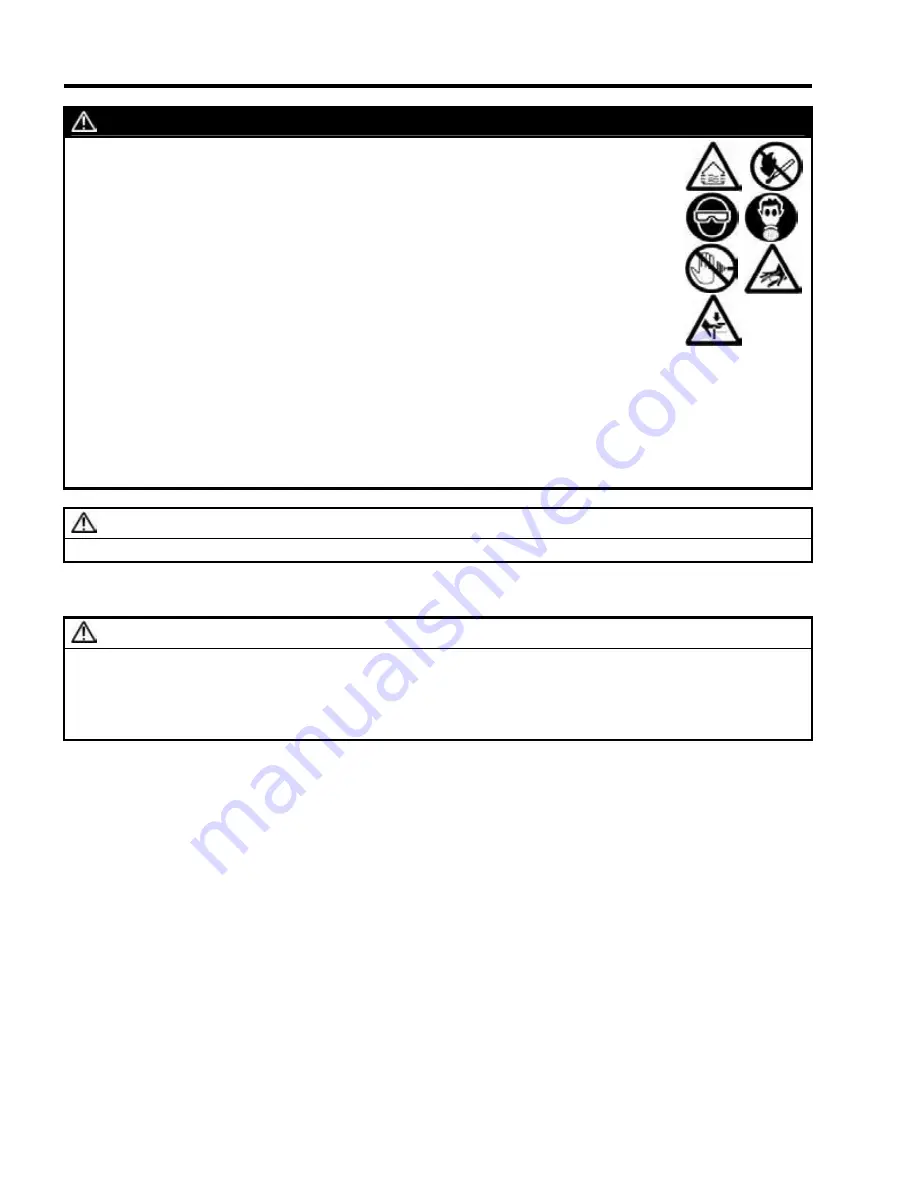
- 12 -
Ű
5. Operation
WARNING
1. Use in well-ventilated spray booth.
2. Avoid any ignition sources such as smoking, open flames or electrical hazard.
3. Always wear protective clothing, eyewear, gloves and respirator.
4. Never spray toward a person or animals and never pull the trigger of the spray gun
near the body.
5. Never stop or deflect a fluid leak from the spray equipment or fluid hose with your
hand. Be sure to stop the spray equipment according to
5-4. Emergency stopping
procedure on page 13.
6. Never touch moving parts.
7. Always release air and fluid pressure when not the use.
8. Always release air and fluid pressure before cleaning, disassembly or service. For
emergency stop and to prevent unintended operation, a shut off valve is installed on
this unit to stop the air supply.
9. Be sure to use the spray equipment at less than the maximum working pressure. If not,
it can cause spray equipment failure, malfunction, serious injury or death.
10. Never modify this unit for any other applications.
11. Never use this unit to spray or supply food products.
12. If operation appears incorrect, immediately stop operation and find the cause. See
8.
Trouble Shooting
on page 16.
13. Never use until the problem has been solved.
CAUTION
1. Be sure to use compatible fluid and cleaning fluid with the wetted parts of this unit.
5-1. Flushing
IMPORTANT
1. Flush fluid passages of this unit completely with cleaning fluid before first use and every time after use. If
not, it can cause finish problem and pump malfunction.
2. Always fully close or fully open circulation valve. Opening valve halfway can cause seat wear, fluid leakage
and lack of fluid pressure.
3. Be sure to follow local guidelines for proper cleaning and fluid disposal procedures.
Refer to
Fig.1
on page 8 or
Fig.2
on page 9 to find reference letters.
1. Remove air cap set and nozzle tip from spray gun.
2. Close
Air Regulators
(C and F) fully.
3. Open
Circulation Valve
(G).
4. Set
Emergency Valve
(D) to “
Operating
” position.
5. Put
Suction Hose Set
(E) and
Circulation Tube
(H) into cleaning fluid container.
6. Adjust
Air Regulator
(C) to 22 - 73psi (0.15 - 0.5MPa, 1.5 - 5bar) slowly.
7. Circulate cleaning fluid or dump to another container through
Circulation Tube
(H).
8. Point the spray gun toward to container and pull the trigger of the spray gun. Be sure that compressed air is
not supplied to the spray gun before pulling the trigger.
9. Close
Circulation Valve
(G).
10. Circulate cleaning fluid or dump to another container through the spray gun.
11. After flushing, lift
Suction Hose Set
(E) from container and keep operating pump until air comes out of spray
gun.
12. Open
Circulation Valve
(G) and release the trigger of spray gun.
13. Keep operating until air comes out from
Circulation Tube
(H).
14. Close
Air Regulators
(C and F) fully.
Summary of Contents for MSU-111N
Page 31: ...29 10 Parts List 10 2 Plunger pump 13 1 PP 7131N...
Page 33: ...31 10 Parts List 10 3 Plunger pump 17 1 PP 1171CNE...
Page 38: ...36 Note...
Page 39: ...37 Note...
Page 40: ...Manual Nr T032 00...