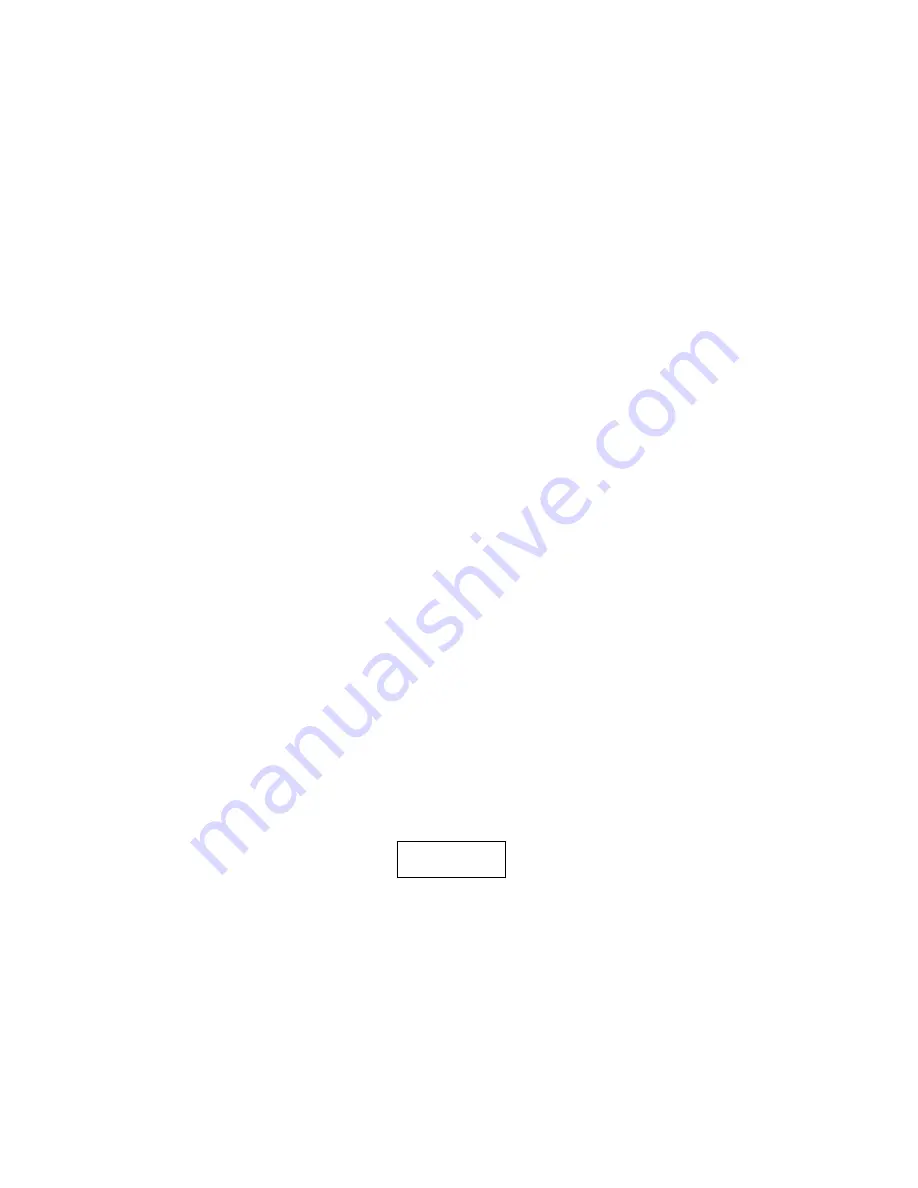
53
2.
Install all hardware and tighten to 8 Foot Pounds.
3.
Repeat procedure for all screws on all flange connections.
4.
After all electronic tests have been performed, wipe clean with isopropanol (not supplied),
allow to dry and apply sealer, using brush (item 19) supplied, to entire periphery of waveguide
flanges. It shall in all cases bridge completely interfaces between flange faces.
a.
Mount waveguide support hardware between feed support channels as shown in sections A-A and
B-B (Figure 3-9), except do not assemble retainers (item 15) or their associated hardware.
b.
Assemble waveguide bend (item 1) as shown to the transducer of the lower feed using one of the
choke flange hardware kits (item 4).
c.
Attach the assembled upper waveguide run to the supports per sections A-A and B-B using spacers
(item 12), retainers (item 15), flat washers (item 9), split washers (item 10) and nuts (item 8) as
shown. Clamp the waveguide with the retainers (item 15) by running nuts down until clamping
pressure is firm but avoid over tightening to prevent damage to waveguide. All supports should be
positioned to minimize stress on the waveguide runs.
d.
Assemble the WR.284 Flexible Waveguide (item 16) from the end of this waveguide using a CPR
flange hardware kit (item 3).
e.
Assemble the lower waveguide bend (item 2) from the transducer of the upper feed as shown using
the one of the choke flange hardware kits (item 4).
f.
Assemble the WR.284 Flexible Waveguide (item 16) from the end of this waveguide using a CPR
flange hardware kit (item 3).
g.
Support the lower waveguide run in the same manner as the upper. Refer to Figure 3-9, sections A-A
and B-B.
h.
Waveguide runs should be centered, one over the other, and flanges secured (tightened) before final
securing of the supports (sections A-A and B-B).
i.
After waveguide runs have been secured, attach free flange ends of flexible waveguide to the mating
flanges of the Rotary Joint using M6 metric hardware and CPRG half gaskets from item 5.
CAUTION
DO NOT APPLY FORCE ON THE WAVEGUIDE FLANGE WHEN HANDLING OR
INSTALLING THE FLEXIBLE WAVEGUIDE. BENDING THE FLEXIBLE WAVEGUIDE
SHOULD BE DONE BY APPLYING FORCE ON THE BODY OF THE WAVEGUIDE AND
NOT ON THE FLANGES.
Summary of Contents for 174100
Page 17: ...17 Figure 1 1 Typical Pattern Azimuth...
Page 18: ...18 Figure 1 2 Typical Pattern Elevation...
Page 19: ...19 Figure 1 3 Polarizer Schematic...
Page 20: ...02 08 2016 SDR ASR11 052 TI 6310 59 20...
Page 22: ...22 Figure 3 1 Complete Antenna Installation...
Page 23: ...23 Figure 3 2 Shipping and Support Stand...
Page 33: ...33 Figure 3 3 Base Interface Kit PSR Base Assembly...
Page 35: ...35 Figure 3 4 Fixed Feeds Unit Installation...
Page 42: ...42 Figure 3 5 Ladder Kit Installation...
Page 45: ...45 Figure 3 6 PSR SSR Interface Mount Installation...
Page 49: ...49 Figure 3 7 Antenna Lift Kit Installation...
Page 54: ...54 Figure 3 8 Waveguide Installation...
Page 55: ...55 Figure 3 9 Waveguide Hanger Installation...
Page 61: ...61 Figure 3 11 SSR Coaxial Cable Installation and Tilt Scale Bracket Installation...
Page 65: ...65 Figure 3 12 Antenna Feedhorn and Tilt Alignment Contour Cheek...
Page 66: ...66 Figure 3 13 Antenna Azimuth Alignment...
Page 67: ...67 Figure 3 14 Counterweight Installation...
Page 81: ...02 08 2016 SDR ASR11 052 TI 6310 59 75 This Page Intentionally Left Blank...
Page 82: ...76 Figure 4 1 Polarizer...
Page 83: ...77 Figure 4 2 Polarizer Motor Replacement...
Page 87: ...81 Figure 5 1 Test Antenna Kit...