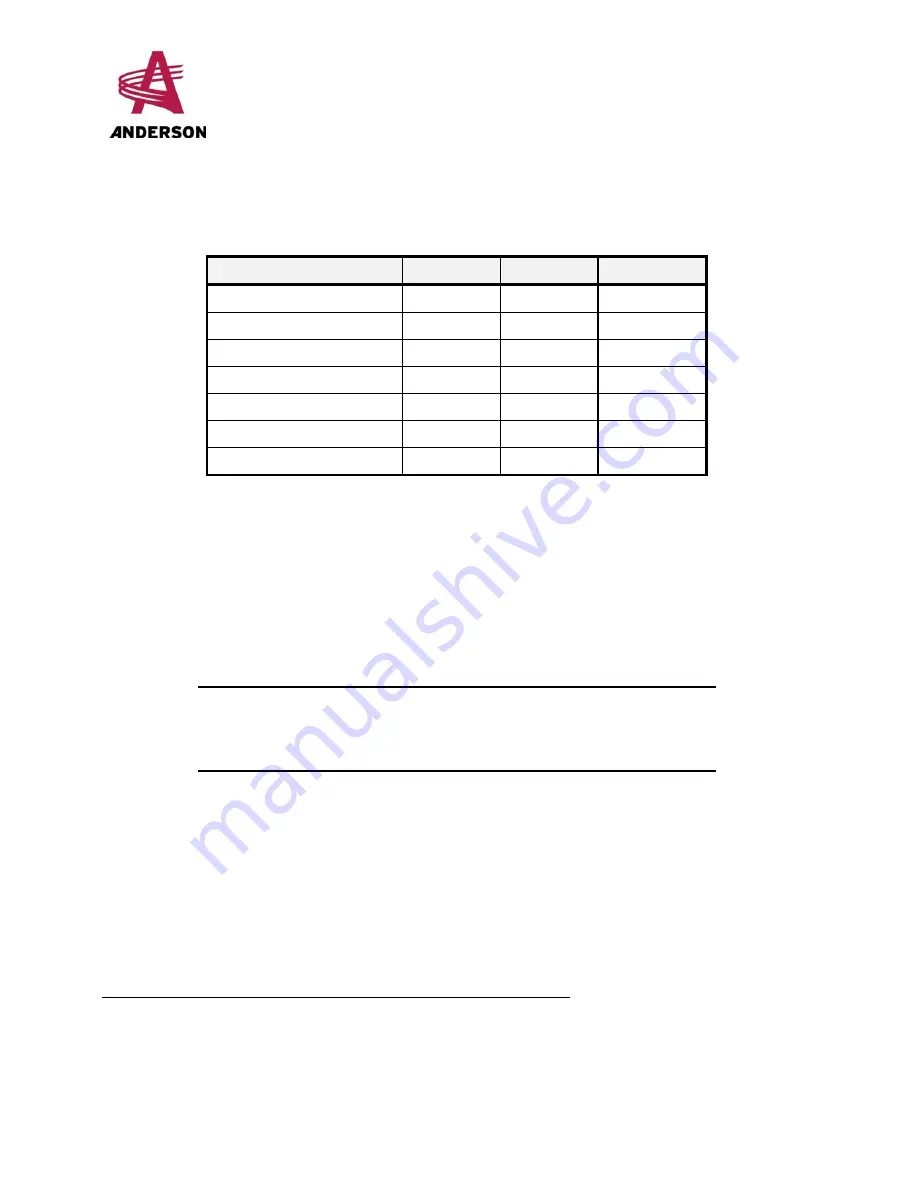
18
Operator's Manual – Self-Loading Trailer
Anderson Group
1.3 Options
The following table shows the optional parts available for your trailer.
Table 5 — Optional Parts for the RBM Self-Loading Trailers
Option
RBM1400
RBM2000
RBM2000S
Air brake
X
X
Hydraulic brake
X
X
X
Ring hitch
X
X
Dual hitch
X
X
X
Hydraulic selector valve
1
X
X
Bale spacer
X
X
X
Backup camera
X
X
X
1.4 Machine identification
A 5 x 10 cm (2 x 4 in.) nameplate is located near the trailer arm. It displays the following information
about your equipment:
l
Model
l
Serial number
l
Tare weight
l
Gross weight
l
Manufacturing year
NOTE:
You must always have this information on hand when
ordering replacement parts or requesting assistance from
our customer service department.
You can record the identification information of your equipment in Figure 4.
1
Used when the tractor has only two hydraulic systems. This valve allows you to control the pusher
and unloading functions on the same oil outlet.
Summary of Contents for RBM Series
Page 1: ...Self Loading Trailer RBM 404676 Operator s Manual 2018 2019...
Page 2: ......
Page 6: ......
Page 8: ......
Page 12: ......
Page 30: ......
Page 36: ......
Page 48: ......
Page 60: ......
Page 68: ...68 Operator s Manual Self Loading Trailer Anderson Group Figure 28 Pusher Greasing Points...
Page 86: ......