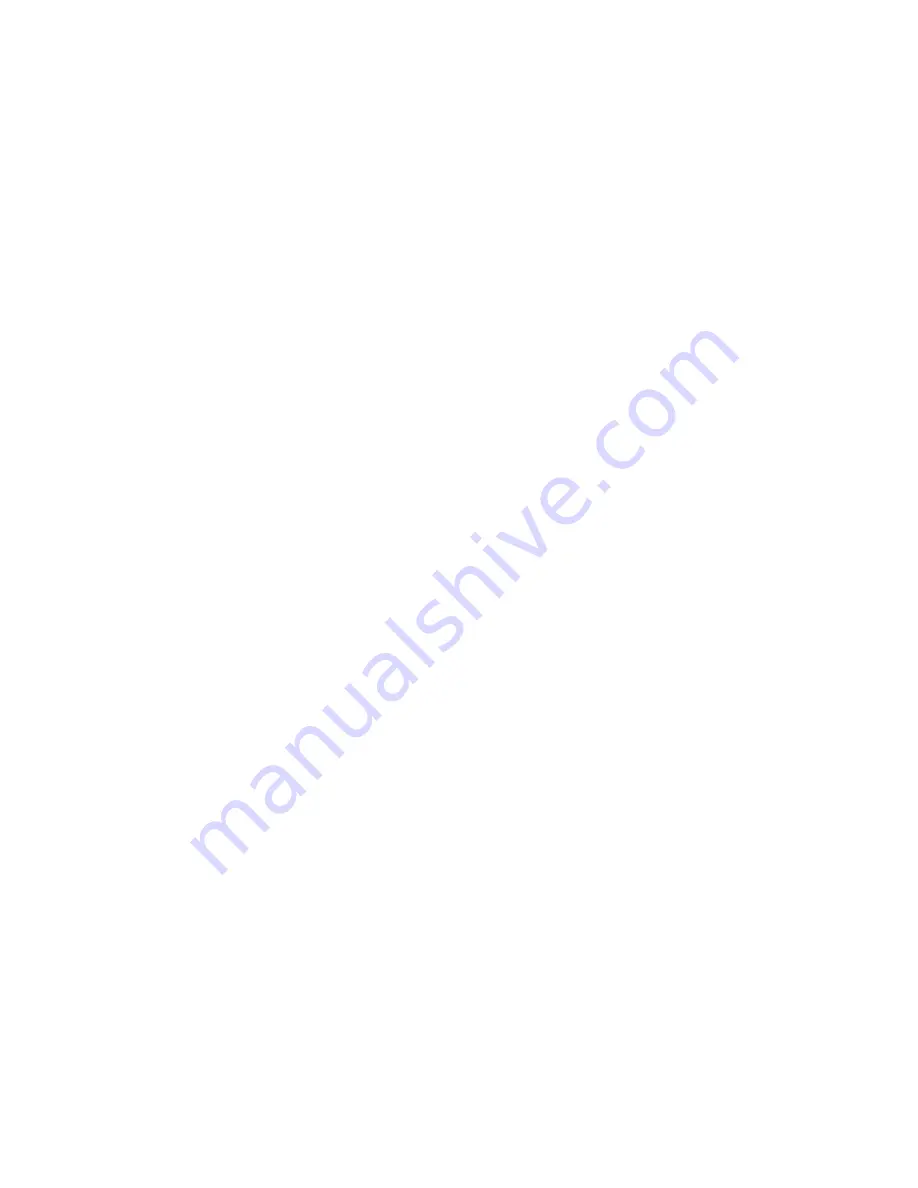
September 2012
L010194
3
Introduction
The DPC50501 is a single axis programmable controller, a 5 amp bipolar microstep driver, and
a 48VDC 65W power supply package. It provides flexible, independent control of bipolar step
motors with a current range from 0.5 to 5.0 amps and microstepping resolutions of 1, 2, 5, 8, 10,
16, 32 and 64. The easy to use software, SMC50WIN, can be used to directly control motion and
to program the controller. The DPC50501 also has the ability for real time functions. A “direct
mode” is used to directly control motion for real time movements through serial communication.
The DPC50501 has 20 commands which are easy to remember for direct movement and uses
the RS485 communication protocol so up to 32 units can be networked together from one com-
munications port on your PC or PLC (programmable logic controller). The DPC50501 also has 2
programmable “open drain” outputs and 4 TTL compatible inputs and can be powered from 105
VAC to 130VAC. The DPC50501 is direct replacement in size and connections with Anaheim
Automation’s DPC40501. The upgrades to this unit include higher resolution and higher motor
currents.
Section 1:
Description
Generally step motor controllers are open-loop systems, meaning that no information is sent back
to the controller from the motor to verify the number of steps that were taken. A step motor is
essentially a digital device - you give the step motor driver 10 step pulses, and the motor moves
10 steps. The DPC50501 provides independent programming of acceleration/deceleration, base
speed (start up speed), max speed (running speed), and the number of steps to both relative
and absolute positioning modes. On absolute positioning moves, the controller automatically
determines the proper direction to go and the number of steps to take. The relative positioning
will move a number of steps in the direction that the user defines. The controller has a high level
command set including: looping, conditional statements, time delays, and I/O. Hard, soft, and
home limit switch inputs are provided for each axis. These features are generally required in most
machine control designs. Four testable inputs and 2 programmable outputs are provided per
axis. These I/O are accessible independent of the busy state of the axis controls. The 4 inputs
are TTL/CMOS compatible. The 2 outputs are current sinking, open drain FETs. The controller
in the DPC50501 has a built-in programmable reset circuit. Reset is automatic on power-up or
by pressing the external reset button. A CD is provided when you purchase the unit. This CD
contains software that allows you to write and change programs that are to be store in the con-
troller for autostart use. This CD also allows you to save the programs onto your computer hard-
drive, and easily retrieve them when needed. The clock and direction outputs of the controller
are internally wired to the driver. The “microstep driver” in the DPC50501 has an output current
capability of 0.5 amp minimum to 5.0 amps maximum (peak rating). The driver offer motor cur-
rent ON/OFF capabilities. The Reduce Current Enabled automatically reduces motor current to
50% of the set value after the last step is made (20msec delay). With the DPC50501, various
step resolutions can be implemented by the onboard dip switch. These divisions range from
200 steps per revolution to 12800 steps per revolution. The bipolar driver configuration handles
4, 6, and 8 lead motors. Protection devices have been added to this driver for phase to phase
short-circuit conditions.
July 2018