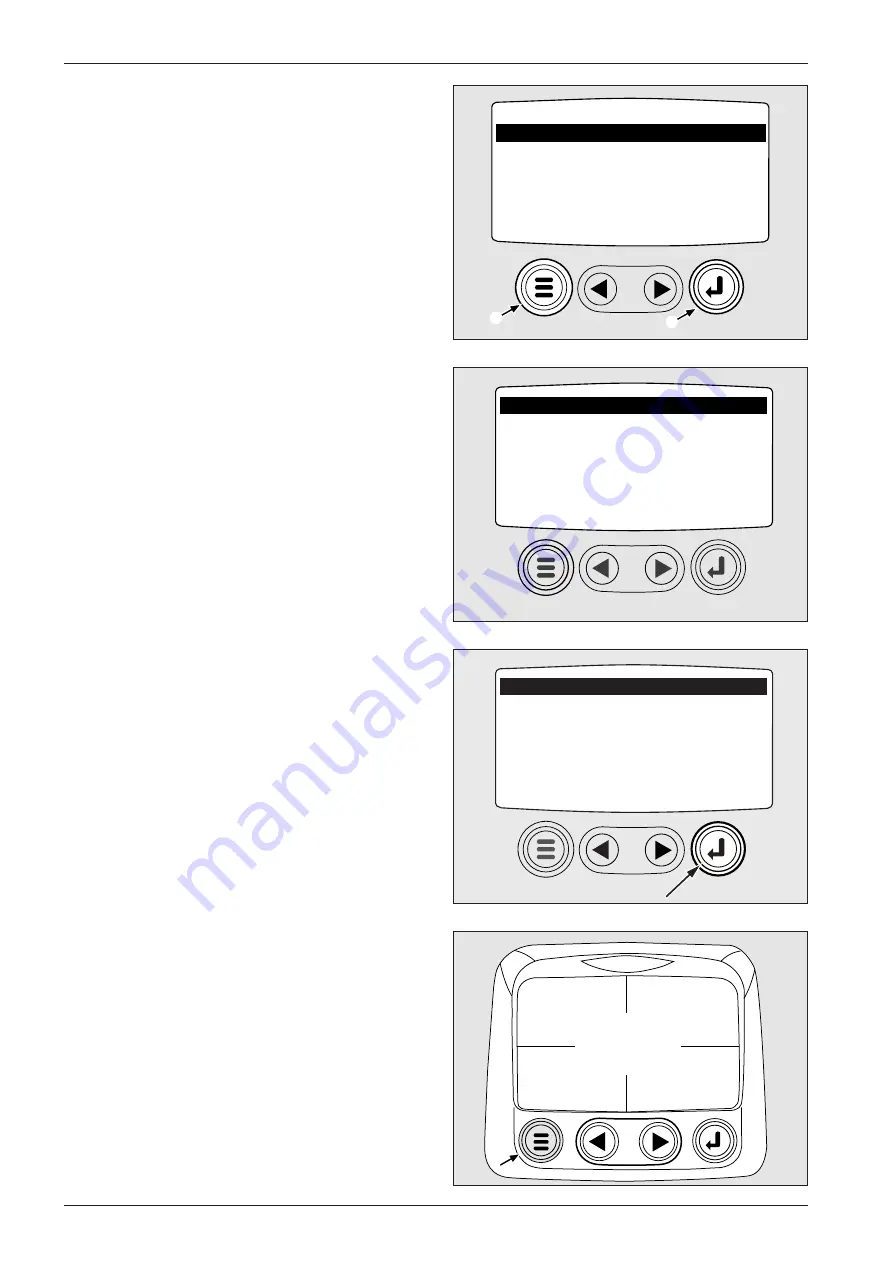
54
AP 240
GO TO 4 - UP DISPLAY
LANGUAGES
STORED CODES
ENGINE CONF
SETUP 1 - UP DISPLAY
SETUP 4 - UP DISPLAY
SELECT UNITS
396012
ADJUST BACKLIGHT
ADJUST CONTRAST
UTILITIES
396031
2
1
GO TO 4 - UP DISPLAY
LANGUAGES
STORED CODES
ENGINE CONF
SETUP 1 - UP DISPLAY
SETUP 4 - UP DISPLAY
SELECT UNITS
396045
396322
20%
FUEL LEVEL
100
ENG HRS
28°C
COOL TEMP
0 RPM
ENG RPM
2.6. Controllers & Control Instruments
Use ENTER 1 to open highlighted item. Press buttons in Menu
2.
Main menu will be displayed (GO TO 4-UP DISPLAY).
Press ENTER button.
Four-parameter display will show. Press MENU button to display
main menu.
Note
Four-parameter display is basic setting from the machine manu-
facturer; turn ON ignition box key to display it.
Summary of Contents for AP 240
Page 1: ...Book ID 4 P06430CU AP 240 Cummins EN Operating manual...
Page 2: ......
Page 4: ......
Page 5: ...M sto a datum vyd n Place and date of issue Ort und Datum der Ausgabe...
Page 6: ......
Page 14: ...8 AP 240...
Page 15: ...9 AP 240 SPECIFICATION MANUAL 1 SPECIFICATION MANUAL AP 240 Cummins Tier 3...
Page 24: ...18 AP 240 Notes...
Page 25: ...19 AP 240 SPECIFICATION MANUAL Notes...
Page 26: ...20 AP 240...
Page 27: ...21 AP 240 OPERATION MANUAL 2 OPERATION MANUAL AP 240 Cummins Tier 3...
Page 28: ...22 AP 240...
Page 88: ...82 AP 240 Notes...
Page 89: ...83 AP 240 OPERATION MANUAL Notes...
Page 90: ...84 AP 240...
Page 91: ...85 AP 240 MAINTENANCE MANUAL 3 MAINTENANCE MANUAL AP 240 Cummins Tier 3...
Page 92: ...86 AP 240...
Page 156: ...150 AP 240...
Page 166: ...160 AP 240 3 8 Annexes Notes...
Page 167: ...161 AP 240 MAINTENANCE MANUAL Notes...
Page 168: ...162 AP 240 3 8 Annexes Notes...
Page 169: ......