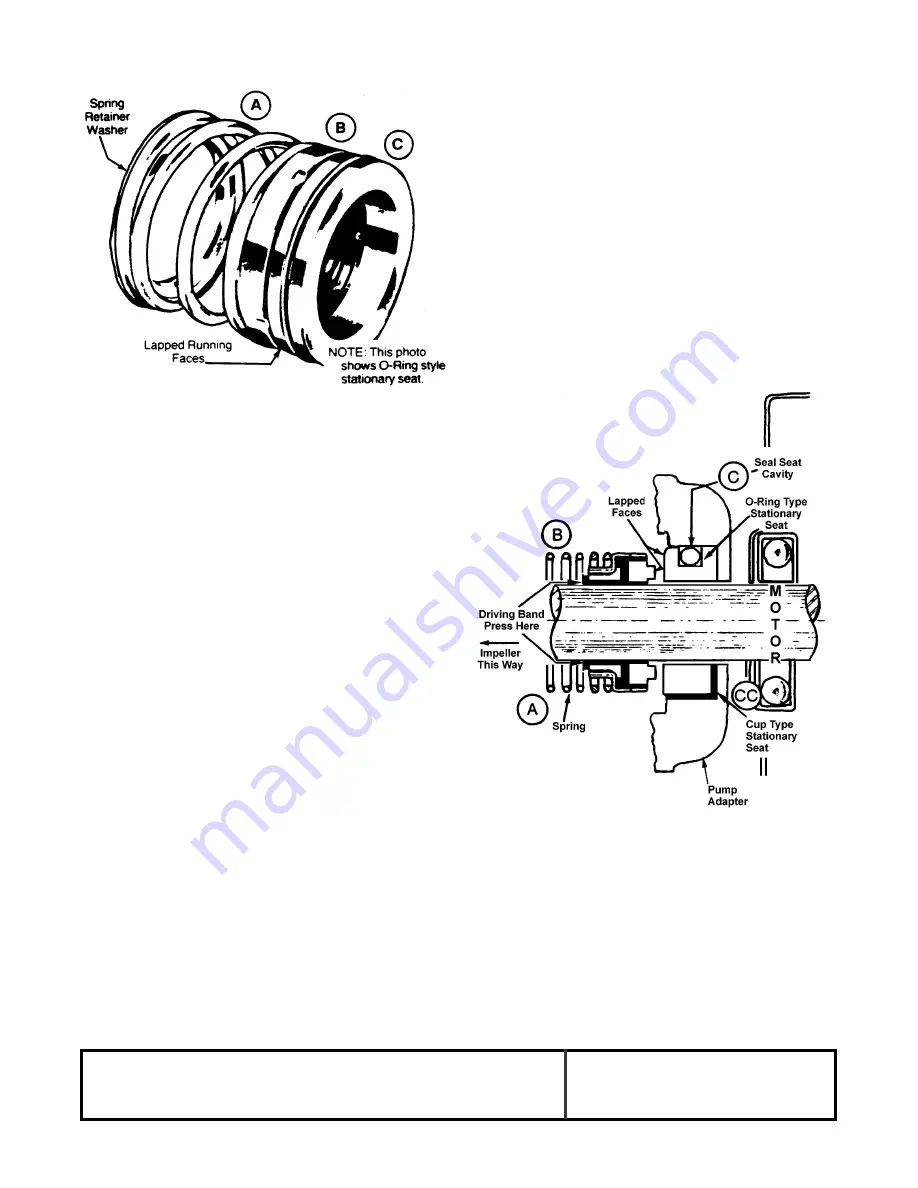
INSTALLATION INSTRUCTIONS
TYPE 21 SHAFT SEAL
The seal assembly consists of these components:
A
SPRING
B
ROTARY SEAL HEAD
C
STATIONARY SEAT - May
have an O-ring groove in seat (C)
or a rubber cup seat (CC).
CAUTION:
This seal is a precision product and should
be handled accordingly. Be especically careful of the
lapped sealing surface of the rotary washer and
stationary seat.
THE SEAL IS SUPPLIED WITH
A PACKET OF LUBRICANT.
LAPPED RUNNING FACES
The lapped running surfaces of the rotary seal head
and stationary seat must be treated with care. KEEP
CLEAN. DO NOT SCRATCH. Use a clean, soft cloth
during installation. Protect the faces. Install both the
seat and rotary square to the shaft. Check the
stationary seat installation from behind the seal cavity
for squareness.
STATIONARY SEAT INSTALLATION (C)
Clean the seal seat cavity of the adapter and lubricate.
Lubricate the seat O-ring or cup and press the
stationary seat in seal cavity of the adapter squarely
and evenly using an arbor press and the cardboard disc
supplied with the seal. Be careful not to scratch or
touch the lapped surface of stationary seat.
Inspect the face of the stationary seat to be certain
there is no dirt on face. If there is any dirt or fingerprints
on the face, wipe it off carefully with a soft cloth.
ROTARY SEAL HEAD INSTALLATION (B)
Clean, polish and lubricate the shaft (or shaft sleeve).
Check lapped faces on the stationary seat and rotary
seal head. Be certain no dirt is on either face.
Lubricate lightly.
Slide the rotary seal head on the shaft with the carbon
rotating ring facing the stationary seat. Press the drive
band until the head seats firmly against the seat. Install
spring (and spring retainer washer if used). Install
impeller which will compress the spring to proper length
assuring correct pressure on the lapped faces.
CAUTION:
Never operate the lapped running faces
dry. The liquid being handled ensures proper
lubrication.
In some cases a short period of operation is required
to clear up slight leakage.
NOTE: The lubricant supplied with the seal is the
only approved lubricant. DO NOT USE OTHER
LUBRICATING LIQUIDS!
61.000.172B
JANUARY 2000
SCOT
HOME OFFICE
• Cedarburg, WI 53012
• P.O. Box 286
• 262-377-7000
•
FAX 262-377-7330
FACTORY BRANCHES
• Irvine, CA 92614
• 1881 Kettering
• 949-756-8076
•
FAX 949-756-9480
• Ft. Lauderdale, FL 33315
• 77 SW 20th Street
• 954-524-6776
•
FAX 954-764-3361
SCOT
DIVISION OF
ARDOX CORP.
Replaces March 1990
20 of 34
Summary of Contents for ICS-TCP Series
Page 11: ...11 of 34 ...
Page 12: ...12 of 34 ...
Page 13: ...13 of 34 ...
Page 14: ...14 of 34 ...
Page 15: ...15 of 34 ...
Page 16: ...16 of 34 ...
Page 17: ...17 of 34 ...
Page 18: ...18 of 34 ...
Page 19: ...19 of 34 ...
Page 22: ...Amiad USA INC Level I Filter Controller UL 508A Standard 22 of 34 ...
Page 32: ...Page 11 Rev 091014 Operating and Maintenance Manual Page 11 32 of 34 ...