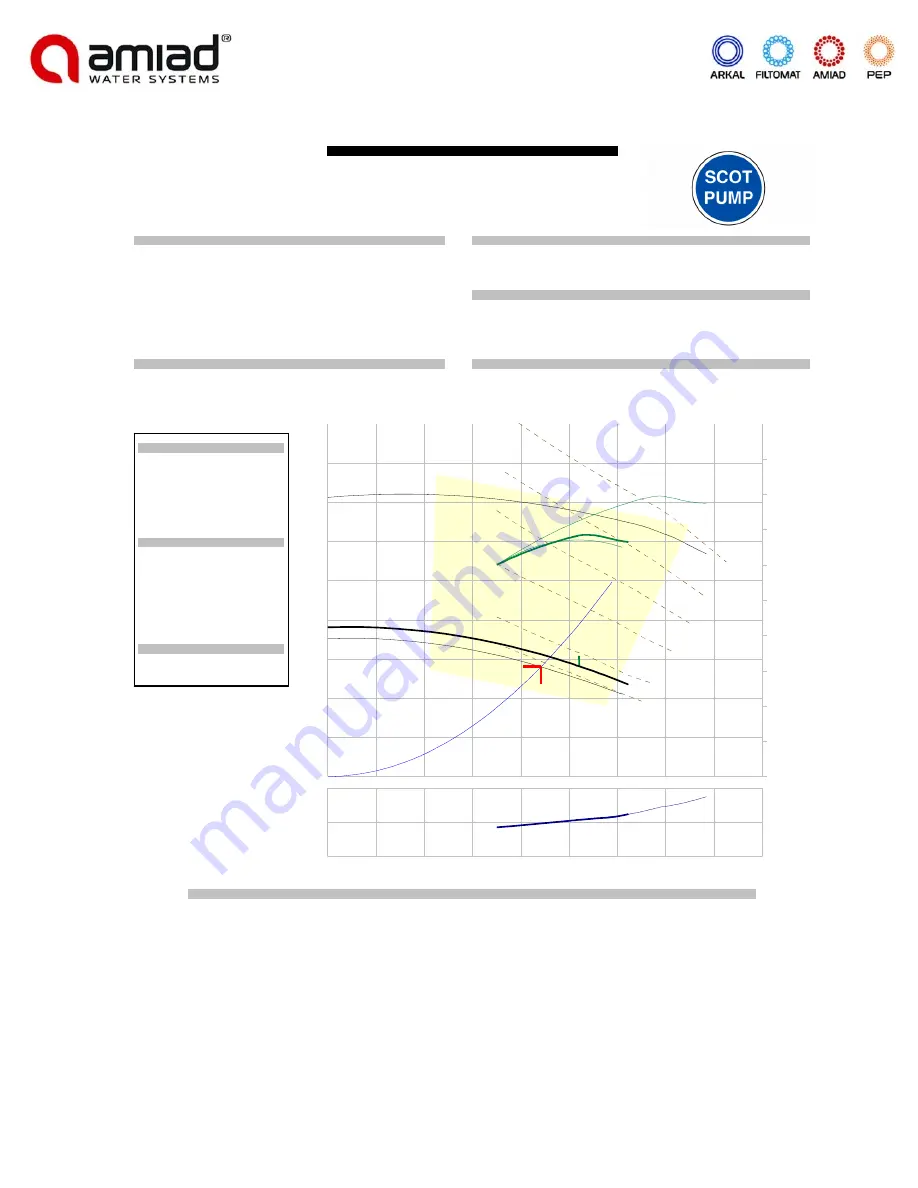
Rev: 09.2017
EBS Pre-Engineered Skid IOM
24
Pump Data Sheet - Scot Division of Ardox Corp.
Company: Amiad Water Systems
Name: EBS_10K_883
Date: 2/5/2016
Pump:
Size: 059-7.0-6.0x5.0
Type: Endsuct-Encl
Speed: 3500 rpm
Synch speed: 3600 rpm
Dia: 5.625 in
Curve: 40.000.502
Impeller:
Specific Speeds:
Ns: ---
Nss: ---
Dimensions:
Suction: 6 in
Discharge: 5 in
Pump Limits:
Temperature: 300 °F
Power: ---
Pressure: 175 psi g
Eye area: ---
Sphere size: ---
Search Criteria:
Flow: 883 US gpm
Head: 70 ft
Near miss: 5 % of Head
Fluid:
Water
Temperature: 60 °F
SG: 1
Vapor pressure: 0.2563 psi a
Viscosity: 1.105 cP
Atm pressure: 14.7 psi a
NPSHa: ---
Motor:
Size: 30 hp
Speed: 3600
Frame: 286TS
Standard: NEMA
Enclosure: TEFC
Sizing criteria: Design Point
Selected from catalog: Scot.60 Vers: 10.1
---- Data Point ----
Flow:
883 US gpm
Head:
77.4 ft
Eff:
65%
Power:
26.3 hp
NPSHr:
19.4 ft
---- Design Curve ----
Shutoff head:
95.2 ft
Shutoff dP:
41.2 psi
Min flow:
---
BEP:
68% @ 1042 US gpm
NOL power:
27.9 hp @ 1236 US gpm
-- Max Curve --
Max power:
72.6 hp @ 1568 US gpm
US gpm
NP
SH
r
-
ft
1600
1400
1200
1000
800
600
400
0
200
20
40
Head
-
ft
%
-
Efficien
cy
0
10
20
30
40
50
60
70
80
90
1600
0
1400
25
1200
50
1000
75
100
800
125
600
150
400
175
200
200
68.3
5.625 in
7 in
5.5 in
25 hp
30 hp
40 hp
50 hp
60 hp
75 hp
Performance Evaluation:
Flow
Speed
Head
Efficiency
Power
NPSHr
US gpm
rpm
ft
%
hp
ft
1060
3500
69.3
68
27.2
21.8
883
3500
77.4
65
26.3
19.4
706
3500
84.8
60
25.1
17.1
530
3500
87.5
56
24
14.8
353
3500
---
---
---
---