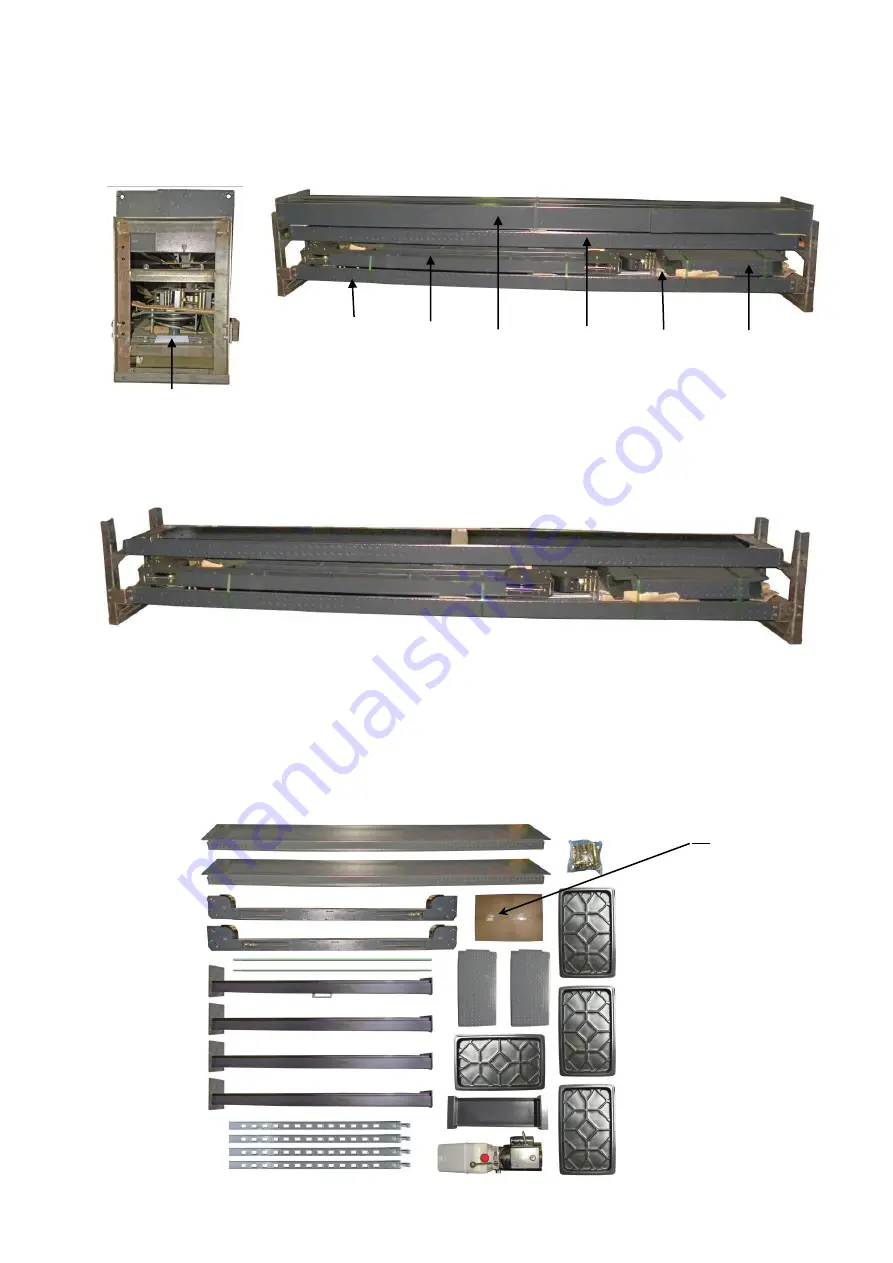
4
2. Open the outer packing carefully, check the parts according to the shipment list.
(See Fig. 5)
.
3. Take off the drive-thru ramps and columns
(See Fig.6)
.
4. Loose the screws of the upper package stand, take off the offside platform, take out
the parts inside the power-side platform, then remove the package stand.
5. Move aside the parts and check the parts according to the shipment parts list
(See Fig. 7).
Fig. 6
Powerside
Platform
Drive-in
Ramp
Offside
Platform
Cross
Beam
Column
Fig. 5
Parts box
62
Fig. 7
Shipment
Parts List
Summary of Contents for 408-P
Page 1: ......
Page 25: ...23 IV EXPLODED VIEW Model 408 P Fig 36 ...
Page 26: ...24 CROSS BEAM CYLINDERS 3 Fig 37 Fig 38 Fig 38 ...
Page 27: ...25 Manual power unit 110V 60HZ Single phase Fig 42 Fig 39 ...
Page 37: ......