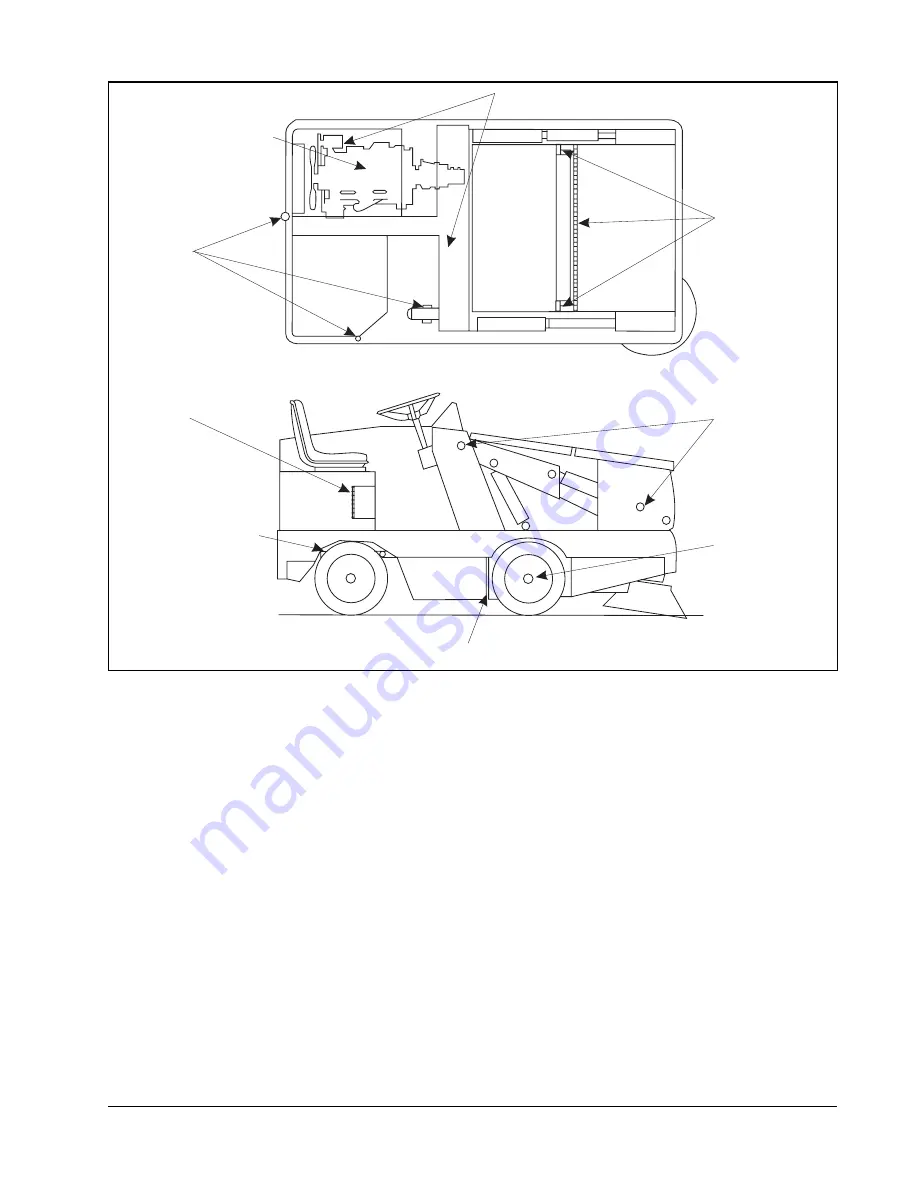
American-Lincoln Technology
3366XP / 4366XP
FORM NO. 56041668 -
19
GENERAL MACHINE MAINTENANCE
THROTTLE CABLE
#10 OIL
#10 OIL
#10 OIL
#10 OIL
DUMP SYSTEM
PIVOT POINTS
FRONT WHEEL
BEARINGS
DRIVE WHEEL
SWIVEL BEARINGS
GOVERNOR &
CHOKE LINKAGE
Perform the following lubrication procedures after every 50 hours of machine use:
1. Lubricate dump system pivot points, with a good grade multipurpose grease. Do the following lubrication procedures after every
100 hours of machine use.
2. Lubricate drive wheel swivel bearing, and the front wheel bearings with a good multi-purpose grease.
3. The steering gear assembly has a grease
fi
tting, located on the front section of the steering gear housing. Use E.P. Lithium
grease to lubricate the steering gear through the grease
fi
tting.
4. Lubricate all other moving joints of the machine with #10 oil.
5. Lubricate the clamp ends of the throttle cable with NAPA #765-1363 or equivalent anti-seize lubricant.