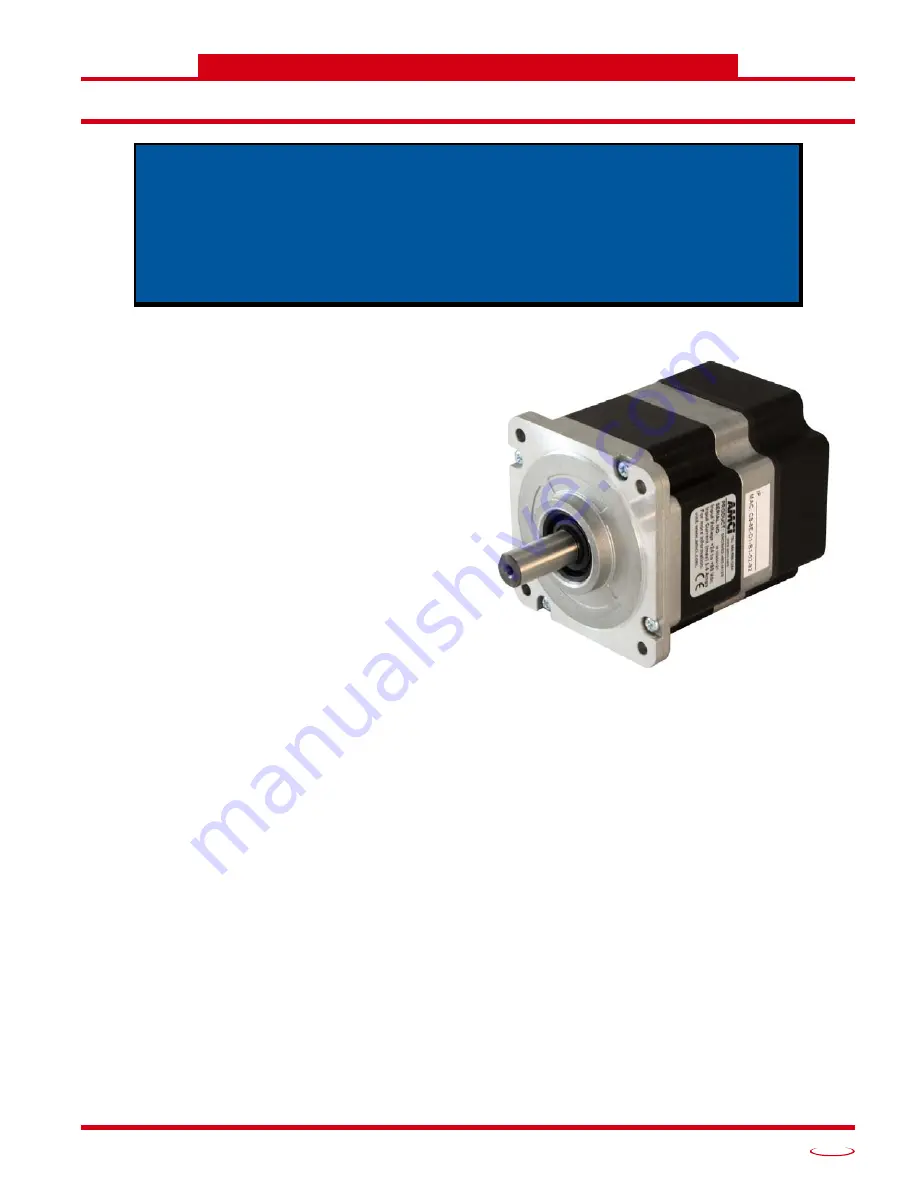
20 Gear Drive, Plymouth Ind. Park, Terryville, CT 06786
Tel: (860) 585-1254 Fax: (860) 584-1973 http://www.amci.com
9
REFERENCE 1
SMD34K S
PECIFICATIONS
The SMD34K Family
The SMD34K units are part of a growing product
line from AMCI with a simple concept: a stepper
indexer, driver, and motor that can be attached to
any popular industrial network. Each SMD34K
attaches to your Ethernet based network and com-
municates using the EtherCAT protocol.
EtherCAT uses standard Ethernet cabling, but
forgoes the full TCP/IP stack typically associated
with Ethernet communications. The EtherCAT
protocol transfers data to and from multiple
slaves with a single packet of information. Data
for each slave is located at a known position
within the packet. EtherCAT slave devices use a
hardware only solution to read and write data to
the packet before transmitting the packet to the
next slave. This results in a delay that is typically
4 microseconds or less. This results in a very fast
and deterministic network.
An EtherCAT Slave Information (ESI) file is
available for the SMD34K units. The ESI file is
required to add the device to the network. Con-
figuration of the SMD34K is accomplished using
the CANopen PDO and SDO objects. EtherCAT
supports CANopen through its CANopen over
Ethernet (CoE) interface. Motion commands and
status information is transmitted using the output
and input variables assigned to the SMD34K
when the EtherCAT system is configured.
Each unit also supports the Distributed Clock (DC) functionality of the EtherCAT system. This allows you to
synchronize the start of moves across devices using the SYNC0 signal instead of the SyncManager 2 event.
Each unit can be ordered with an optional incremental or absolute multi-turn encoder. This encoder gives you
the additional functionality of position verification and stall detection. The absolute multi-turn encoder allows
you to track machine position with power removed, eliminating the need to home the machine after cycling
power.
All units have a shaft seal and sealed connectors for their Ethernet, I/O, and power connections. These units
carry an IP64 environmental rating. Units can also be ordered sealed with an FDA approved epoxy. These units
carry an IP65/67 rating. These units are protected against low pressure washdown and can be submerged.
This manual is designed to get you up and running quickly with an SMD34K prod-
uct from AMCI. As such, it assumes you have some basic knowledge of stepper
systems, such as the resolution you want run your motor at, and the reasons why
you’d want to use Idle Current Reduction and the reasons why you wouldn’t. If
these terms or ideas are new to you, we’re here to help. AMCI has a great deal of
information on our website and we are adding more all the time. If you can’t find
what you’re looking for at http://www.amci.com, send us an e-mail or call us.
We’re here to support you with all of our knowledge and experience.
Figure R1.1 IP64 Rated SMD34K
Summary of Contents for SMD34K
Page 1: ...MICRO CONTROLS INC ADVANCED U s e r M anual Manual 940 0S280 ...
Page 6: ...TABLE OF CONTENTS SMD34K User Manual ADVANCED MICRO CONTROLS INC 6 Notes ...
Page 50: ...CALCULATING MOVE PROFILES SMD34K User Manual ADVANCED MICRO CONTROLS INC 50 Notes ...
Page 62: ...CONFIGURATION DATA FORMAT SMD34K User Manual ADVANCED MICRO CONTROLS INC 62 Notes ...
Page 80: ...COMMAND DATA FORMAT SMD34K User Manual ADVANCED MICRO CONTROLS INC 80 Notes ...
Page 100: ...LEADERS IN ADVANCED CONTROL PRODUCTS ADVANCED MICRO CONTROLS INC ...