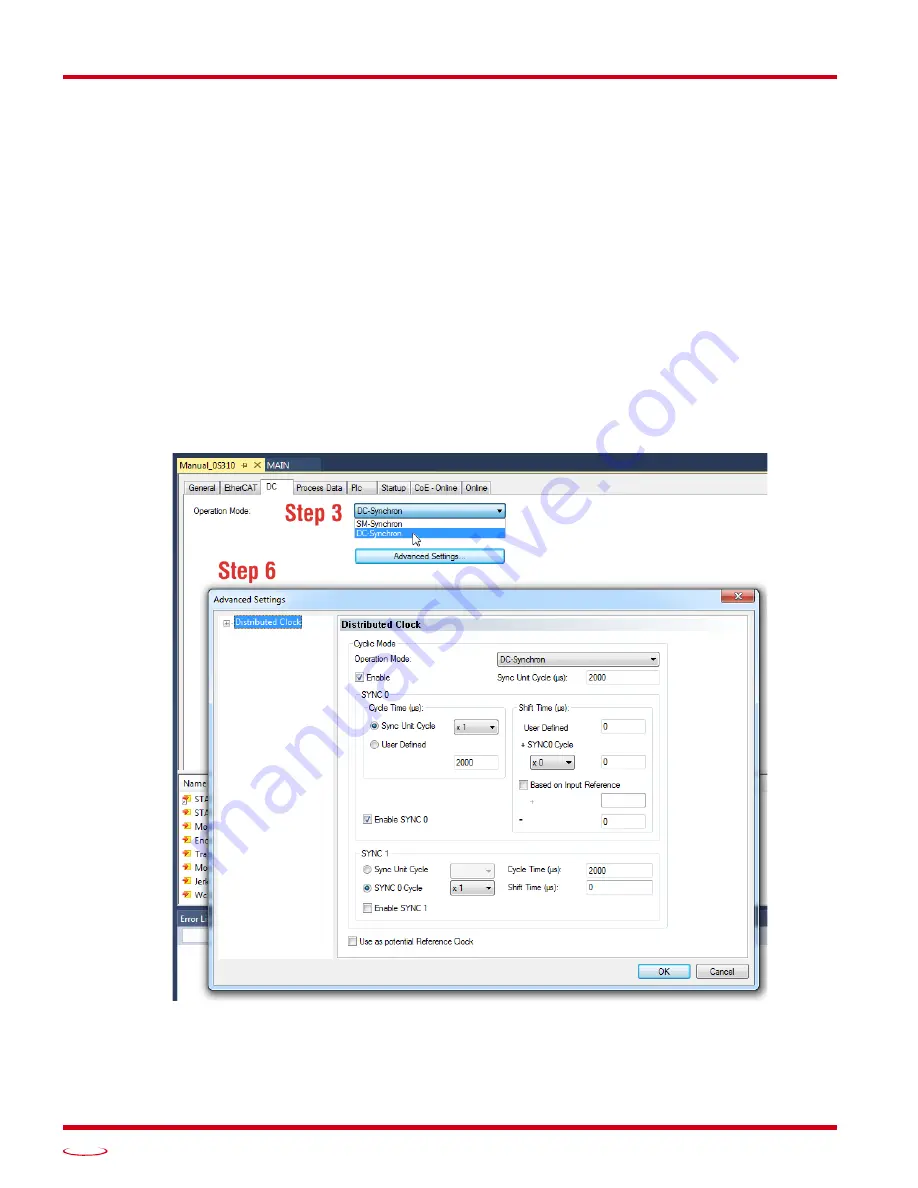
D
ISTRIBUTED
C
LOCK
- SYNC0 S
ETUP
SD4840EK User Manual
ADVANCED MICRO CONTROLS INC.
102
4.3 Set Operational Mode
1) If necessary, expand the I/O Device tree until the SD4840EK is visible.
2) Double click on the SD4840EK to open the setting window for the device.
3) Click on the “DC” tab.
4) Under the Operation Mode setting, click on the drop down menu and select “DC_Synchron”.
5) Click on the [Advanced Settings...] button.
6) Verify or set the following:
Cyclic Mode -> Enable
checkbox is checked.
Sync Unit Cycle (µs)
is equal to the time of the correct task. If not, the variables are not linked
correctly.
SYNC 0 -> Sync Unit Cycle
radio button is enabled. In the drop down menu, set the multiplier as
needed so that the S
ync Unit Cycle (µs)
time multiplied by the multiplier value is between 2 and
50 milliseconds.
Enable SYNC 0
checkbox is checked.
Enable SYNC 1
checkbox is not checked.
7) Click [OK] to close the window.
Figure T4.4 Distributed Clock Settings
Summary of Contents for SD4840EK
Page 1: ...MICRO CONTROLS INC ADVANCED U s e r M anual Manual 940 0S310...
Page 6: ...TABLE OF CONTENTS SD4840EK User Manual ADVANCED MICRO CONTROLS INC 6 Notes...
Page 38: ...MOVE PROFILES SD4840EK User Manual ADVANCED MICRO CONTROLS INC 38 Notes...
Page 48: ...CALCULATING MOVE PROFILES SD4840EK User Manual ADVANCED MICRO CONTROLS INC 48 Notes...
Page 78: ...COMMAND DATA FORMAT SD4840EK User Manual ADVANCED MICRO CONTROLS INC 78 Notes...
Page 94: ...INSTALLING THE SD4840EK SD4840EK User Manual ADVANCED MICRO CONTROLS INC 94 Notes...
Page 104: ...LEADERS IN ADVANCED CONTROL PRODUCTS ADVANCED MICRO CONTROLS INC...