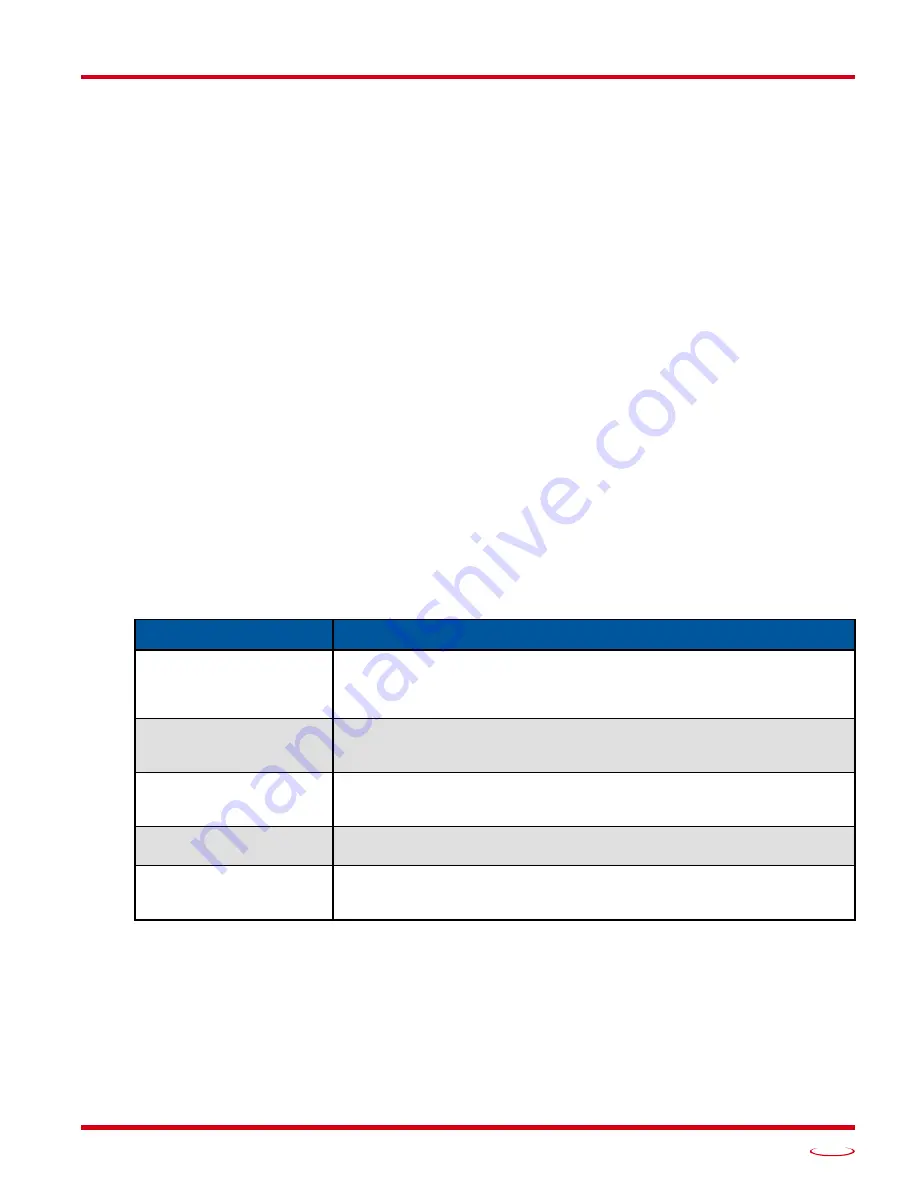
20 Gear Drive, Plymouth Ind. Park, Terryville, CT 06786
Tel: (860) 585-1254 Fax: (860) 584-1973 http://www.amci.com
SD4840EK User Manual
I
NTRODUCTION
TO
THE
SD4840EK
13
Indexer Functionality (continued)
Synchronizing Moves
By default, the SD4840EK uses the SyncManager 2 event to control the transfer of data from the EtherCAT
Slave Controller (ECS) to the microprocessor that controls motion. This allows the SD4840EK to execute
commands as soon as new data arrives. When more than one axis is updated with a single EtherCAT packet,
the time difference between axis updates is very short. Updating multiple axes with a single packet allows the
EtherCAT network to out perform the update times of other industrial network protocols.
On very fast machines, or large machines that require more than one transfer to update all axes, the EtherCAT
Distributed Clock (DC) functionality can be used to closely synchronize motion over multiple axes if using
the SyncMaster2 event proves to be ineffective.
The EtherCAT Distributed Clock functionality is built into the ECS used by the SD4840EK product. The
SD4840EK can act as the reference clock for the system if it is the first device in the EtherCAT network. The
SYNC0 signal, which is based off of the Distributed Clock, can be use to synchronize the start of moves over
multiple devices. The time between when the SYNC0 signal is received by the main processor of the
SD4840EK and when the driver begins to cause motion is 520 ± 25 microseconds. The 520 microseconds is
the time required to read the data from the ECS once the SYNC0 signal becomes active. The ±25 microsec-
onds is caused by the 20 kHz update frequency of the PWM drivers.
For the SD4840EK, the minimum update time on the SYNC0 signal is two milliseconds. If the task time is
less than two milliseconds, the SYNC0 time must be a multiple of the task time.
Encoder Functionality
In addition to the discrete I/O points, the SD4840EK has three inputs for a 5Vdc differential quadrature
encoder. The inputs will also accept 12 to 24Vdc single ended encoder inputs with current limiting resistors.
These signals are always decoded using X4 decoding. When the incremental encoder is used, the indexer sec-
tion of the SD4840EK has the following additional functionality.
Table R1.2 Indexer Encoder Functionality
Feature
Description
Position Verification
When mounted on the motor that is controlled by the SD4840EK, the
encoder can be used to verify motor position motion when a move command
is issued. The encoder position value can be preset to any value and it cam
be captured during a move.
Home to Z pulse
The Z pulse of the encoder can be used to home the machine. In this mode,
any discrete input that is configured as a home input will act as a home prox-
imity sensor.
Stall Detection
The encoder can be used to verify motion when a move command is issued.
An error is issued if the difference in motor and encoder positions is greater
that forty-five degrees.
Encoder Registration
Move
Uses the count from a quadrature encoder to determine when a move begins
to decelerate and stop. Commonly used in spooling/despooling applications.
Electronic Gearing
The SD4840EK can be configured to control the position of a motor based
on feedback from an external encoder. The ratio of encoder pulses to motor
pulses is full programmable and can be changed on-the-fly.
Summary of Contents for SD4840EK
Page 1: ...MICRO CONTROLS INC ADVANCED U s e r M anual Manual 940 0S310...
Page 6: ...TABLE OF CONTENTS SD4840EK User Manual ADVANCED MICRO CONTROLS INC 6 Notes...
Page 38: ...MOVE PROFILES SD4840EK User Manual ADVANCED MICRO CONTROLS INC 38 Notes...
Page 48: ...CALCULATING MOVE PROFILES SD4840EK User Manual ADVANCED MICRO CONTROLS INC 48 Notes...
Page 78: ...COMMAND DATA FORMAT SD4840EK User Manual ADVANCED MICRO CONTROLS INC 78 Notes...
Page 94: ...INSTALLING THE SD4840EK SD4840EK User Manual ADVANCED MICRO CONTROLS INC 94 Notes...
Page 104: ...LEADERS IN ADVANCED CONTROL PRODUCTS ADVANCED MICRO CONTROLS INC...