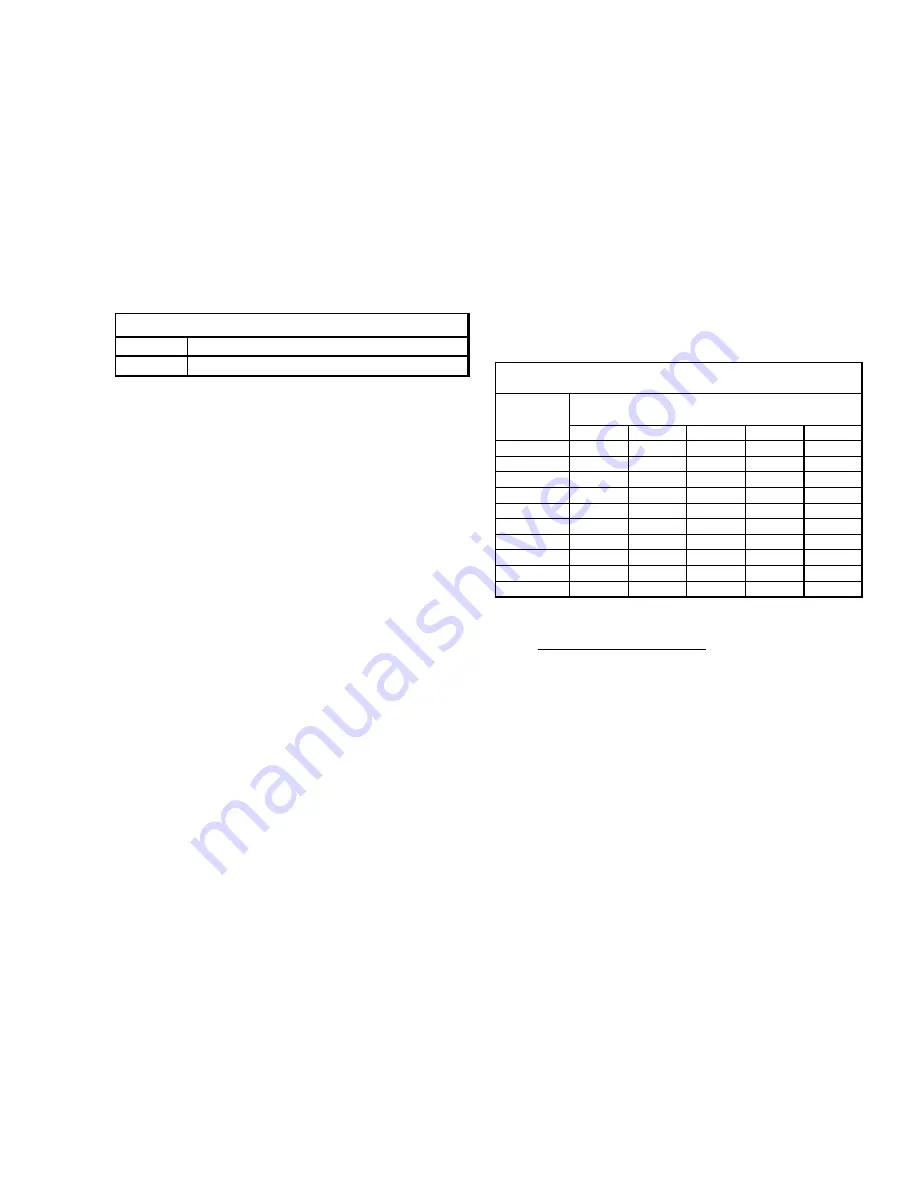
5
IV. Gas Piping
IMPORTANT NOTE: This unit is factory set to operate
on natural gas at the altitudes shown on the rating plate.
If operation at higher altitudes and/or propane gas op-
eration is required, obtain and install the proper conver-
sion kit(s) before operating this unit. Failure to do so
may result in unsatisfactory operation and/or equip-
ment damage. (High altitude kits are for U.S. installa-
tions only - not approved for use in Canada.)
The rating plate is stamped with the model number,
type of gas and gas input rating. Make sure the unit is
equipped to operate on the type of gas available.
INLET GAS PRESSURE
Natural
Min. 5.0" W.C., Max. 10.0" W.C.
Propane
Min. 11.0" W.C., Max. 14.0" W.C.
Inlet Gas Pressure Must Not Exceed the Maximum Value Shown in
Table Above.
Table 1
The minimum supply pressure should not vary from that
shown in the table above because this could prevent
the unit from having dependable ignition. In addition,
gas input to the burners must not exceed the rated input
shown on the rating plate. Overfiring of the unit could
result in premature heat exchanger failure.
High Altitude Derate (US. Installations
Only)
IMPORTANT NOTE: The gas/electric units will natu-
rally derate itself with altitude. Do not attempt to in-
crease the firing rate by changing orifices or increasing
the manifold pressure. This can cause poor combustion
and equipment failure.
At all altitudes, the manifold pressure must be within 0.3
inches W.C. of that listed on the “Specification Sheet”
for the fuel used. At all altitudes and with either fuel, the
air temperature rise must be within the range listed on
the unit nameplate.
Refer to the “Specification Sheet” for kits for conversion
from natural gas to propane gas and for altitude adjust-
ments.
Piping
IMPORTANT NOTE: To avoid possible unsatisfactory
operation or equipment damage due to under firing of
equipment, do not undersize the natural/propane gas
piping from the meter/tank to the unit. When sizing a
trunk line as shown in Table 2, include all appliances on
that line that could be operated simultaneously.
The rating plate is stamped with the model number,
type of gas and gas input rating. Make sure the unit is
equipped to operate on the type of gas available.
The gas line installation must comply with local codes,
or in the absence of local codes, with the latest edition
of the National Fuel Gas Code (ANSI Z223.1).
Connecting The Gas Piping - Natural Gas
Natural Gas Capacity of Pipe
in Cubic Feet of Gas Per Hour (CFH)
Length of
Nominal Black Pipe Size (inches)
Pipe in Feet
1/2
3/4
1
1 1/4
1 1/2
10
132
278
520
1050
1600
20
92
190
350
730
1100
30
73
152
285
590
980
40
63
130
245
500
760
50
56
115
215
440
670
60
50
105
195
400
610
70
46
96
180
370
560
80
43
90
170
350
530
90
40
84
160
320
490
100
38
79
150
305
460
Pressure = .50 PSIG or less and Pressure Drop of 0.3" W.C. (Based
on 0.60 Specific Gravity Gas)
CFH = BTUH Furnace Input
Heating Value of Gas (BTU/Cubic Foot)
Table 2
Refer to Figure 2 for the general layout at the unit. The
following rules apply:
1. Use black iron or steel pipe and fittings for the
building piping.
2. Use pipe joint compound on male threads only.
Pipe joint compound must be resistant to the action
of the fuel used.
3. Use ground joint unions.
4. Install a drip leg to trap dirt and moisture before it
can enter the gas valve. The drip leg must be a
minimum of three inches long.
5. Use two pipe wrenches when making connection to
the gas valve to keep it from turning.
6. Install a manual shut-off valve in a convenient
location (within six feet of unit) between the meter
and the unit.
7. Tighten all joints securely.