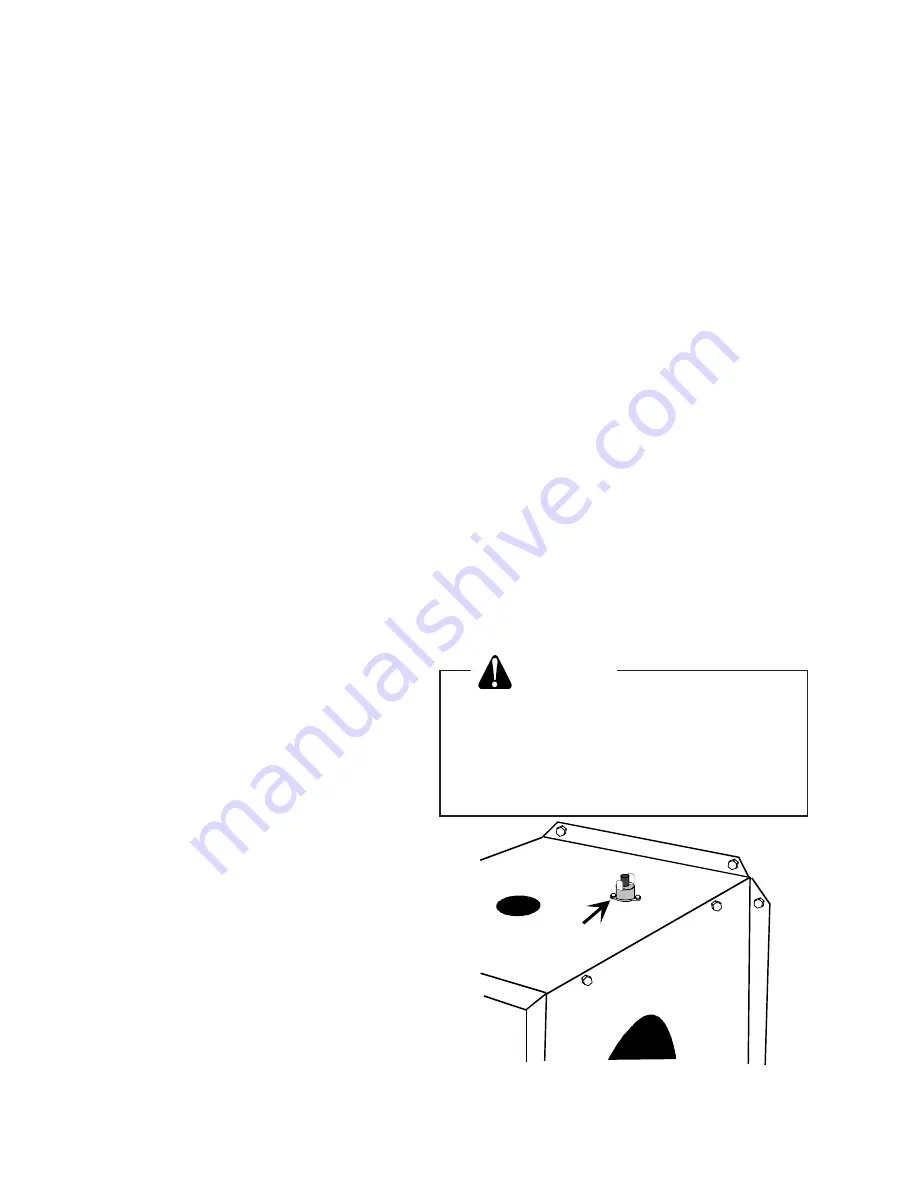
12
Xl. Startup and Adjustment
Heating Startup
General Information
This unit is equipped with an electronic ignition device
to light the pilot which then lights the burners. It also has
a power vent blower to exhaust combustion products.
On new installations, or if a major component has been
replaced, the operation of the unit must be checked.
Check unit operation as outlined in the following instruc-
tions. If any sparking, odors, or unusual sounds are
encountered, shut off electrical power and recheck for
wiring errors, or obstructions in or near the blower
motors. Duct covers must be removed before operating
unit.
Heat Anticipator Setting
The heat anticipator in the room thermostat must be
correctly adjusted to obtain the proper number of heat-
ing cycles per hour and to prevent the room tempera-
ture from over-shooting the room thermostat setting.
Heat anticipator must be set at 0.4 amps.
Roll-out Protection Control
If the flames from the burners are not properly drawn
into the heat exchanger, a roll-out protection device will
open, cutting power to the gas valve. The roll-out pro-
tection device is located on the side of burner box
(Figure 9). The reason for elevated temperatures at the
control should be determined and repaired prior to re-
setting this manual reset control.
WARNING
To prevent death, personal injury or prop-
erty damage due to fire or explosion,
before manually resetting the roll-out pro-
tection device, a qualified servicer must
investigate the reason for the roll-out
protection device to open.
Burner
Box
Roll-Out
Protector
Figure 9
Rollout Protection
IX. Heating Sequence of Operations
Normal Sequence of Operation - Heating
1. Thermostat calls for heat. The combustion blower is
immediately energized.
2. The pressure switch contacts transfer.
3. The ignitor is energized and pilot gas begins to flow.
4. After pilot flame is proven, the main valve is ener-
gized and the pilot will light the main burners.
5. The control checks the signal from the flame sen-
sor. Gas flow will continue only if a proper signal is
present. As soon as pilot flame is proven, the ignitor
is de-energized.
6. The unit will continue to fire for 30 seconds. The fan
control will then start the main circulating air blower.
7. The unit will deliver heat to the conditioned space
until the thermostat is satisfied.
8. The gas valve and combustion blower will be de-
energized when the thermostat opens.
9. There is an adjustable Heat Fan OFF of approxi-
mately 60/90/120/150 second delay (factory set at
120). The control module will de-energize the blower
once the selected time has elapsed. This allows
any additional heat in the heat exchanger to be
transferred to the conditioned space.
X. Cooling Sequence of Operations
Normal Sequence of Operations - Cooling
1. Thermostat calls for cooling. The compressor and
outdoor fan are energized.
2. Approximately six seconds later, the indoor fan
starts.
3. The unit will deliver cooling to the conditioned space
until the thermostat is satisfied.
4. The compressor and outdoor fan will be de-ener-
gized when the thermostat opens.
5. The indoor fan continues to run for approximately
30 seconds after the thermostat is satisfied. This
allows additional cooling from the indoor coil to be
transferred to the conditioned space. Then, the in-
door fan stops.