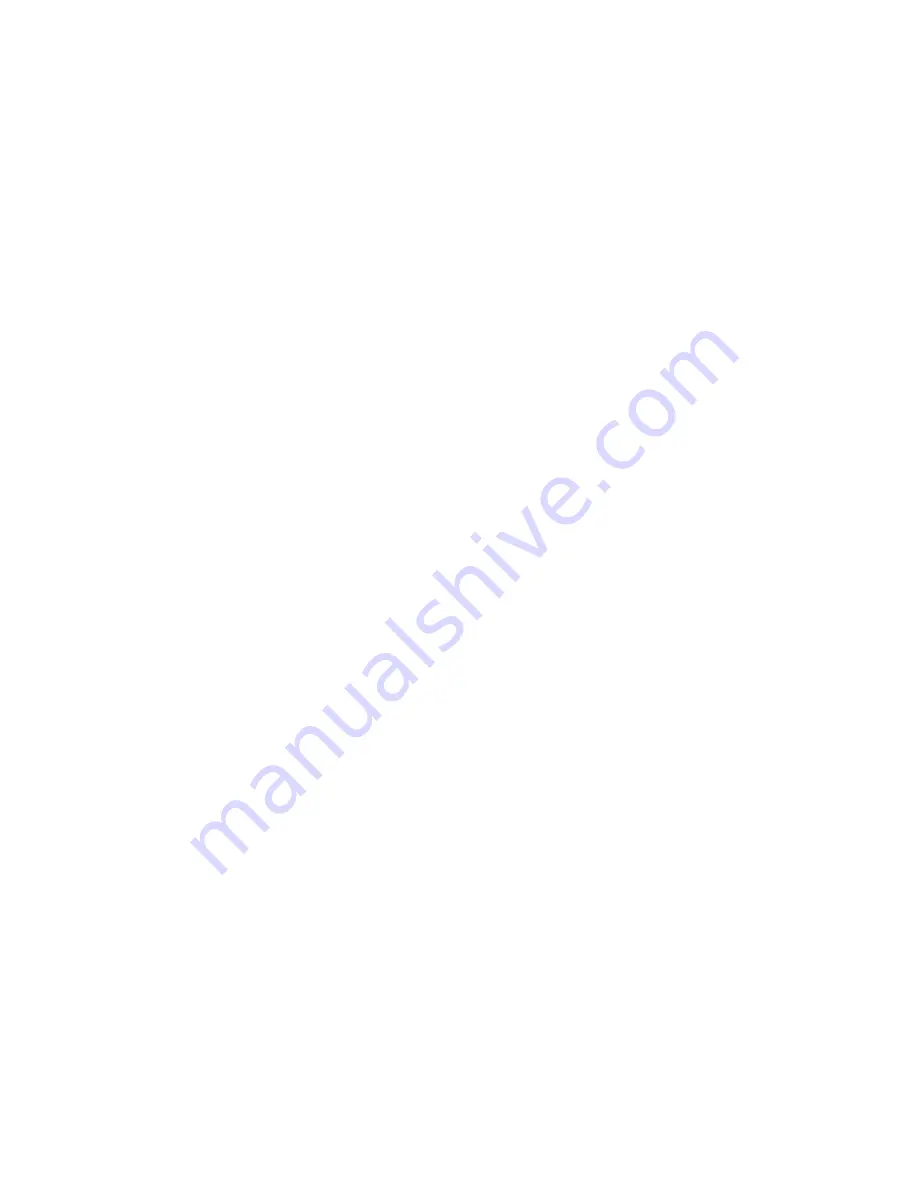
14
Check The Manifold Pressure
A tapped opening is provided in the gas valve to facili-
tate measurement of the manifold pressure. A “U” Tube
manometer having a scale range from 0 to 12 inches of
water should be used for this measurement. The mani-
fold pressure must be measured with the burners oper-
ating.
To adjust the pressure regulator, remove the adjust-
ment screw or cover on the gas valve. Turn out (coun-
terclockwise) to decrease pressure, turn in (clockwise)
to increase pressure. Only small variations in gas flow
should be made by means of the pressure regulator
adjustment. In no case should the final manifold pres-
sure vary more than plus or minus 0.3 inches water
column from the specified pressure. Any major changes
in flow should be made by changing the size of the
burner orifices.
Check The Gas Input (Natural Gas Only)
NOTE: On outdoor equipment, the gas input will vary
with the temperature of the gas. Rated input will be
obtained at approximately 10° F. With warmer ambient
and gas temperatures, the input will decrease. Ex-
ample: At 70° F the input will decrease 12%.
To measure the gas input using the gas meter proceed
as follows:
1. Turn off gas supply to all other appliances except
the unit.
2. With the unit operating, time the smallest dial on the
meter for one complete revolution. If this is a 2
cubic foot dial, divide the seconds by 2; if it is a 1
cubic foot dial, use the seconds as is. This gives the
seconds per cubic foot of gas being delivered to the
unit.
3. INPUT=GAS HTG VALUE x 3600 / SEC. PER
CUBIC FOOT
Example: Natural gas with a heating value of 1000 BTU
per cubic foot and 34 seconds per cubic foot as deter-
mined by Step 2, then:
Input = 1000 x 3600 / 0.34 = 106,000 BTU per Hour.
NOTE: BTU content of the gas should be obtained
from the gas supplier. This measured input must
not be greater than shown on the unit rating plate.
4. Relight all other appliances turned off in step 1. Be
sure all pilot burners are operating.
Check Main Burner Flame
Flames should be stable, soft and blue (dust may cause
orange tips but they must not be yellow) and extending
directly outward from the burner without curling, floating
or lifting off.
Check Temperature Rise
Check the temperature rise through the unit by placing
thermometers in supply and return air registers as close
to the unit as possible. Thermometers must not be able
to sample temperature directly from the unit heat ex-
changers, or false readings could be obtained.
1. All registers must be open; all duct dampers must
be in their final (fully or partially open) position and
the unit operated for 15 minutes before taking read-
ings.
2. The temperature rise must be within the range
specified on the rating plate.
NOTE: Air temperature rise is the temperature differ-
ence between supply and return air.
With a properly designed system, the proper amount of
temperature rise will normally be obtained when the unit
is operated at rated input with the recommended blower
speed.
If the correct amount of temperature rise is not ob-
tained, it may be necessary to change the blower
speed. A higher blower speed will lower the tempera-
ture rise. A slower blower speed will increase the tem-
perature rise.
NOTE: Blower speed MUST be set to give the correct
air temperature rise through the unit as marked on the
rating plate.
Checking External Static Pressure
The total external static pressure must be checked on
this unit to determine if the airflow is proper.