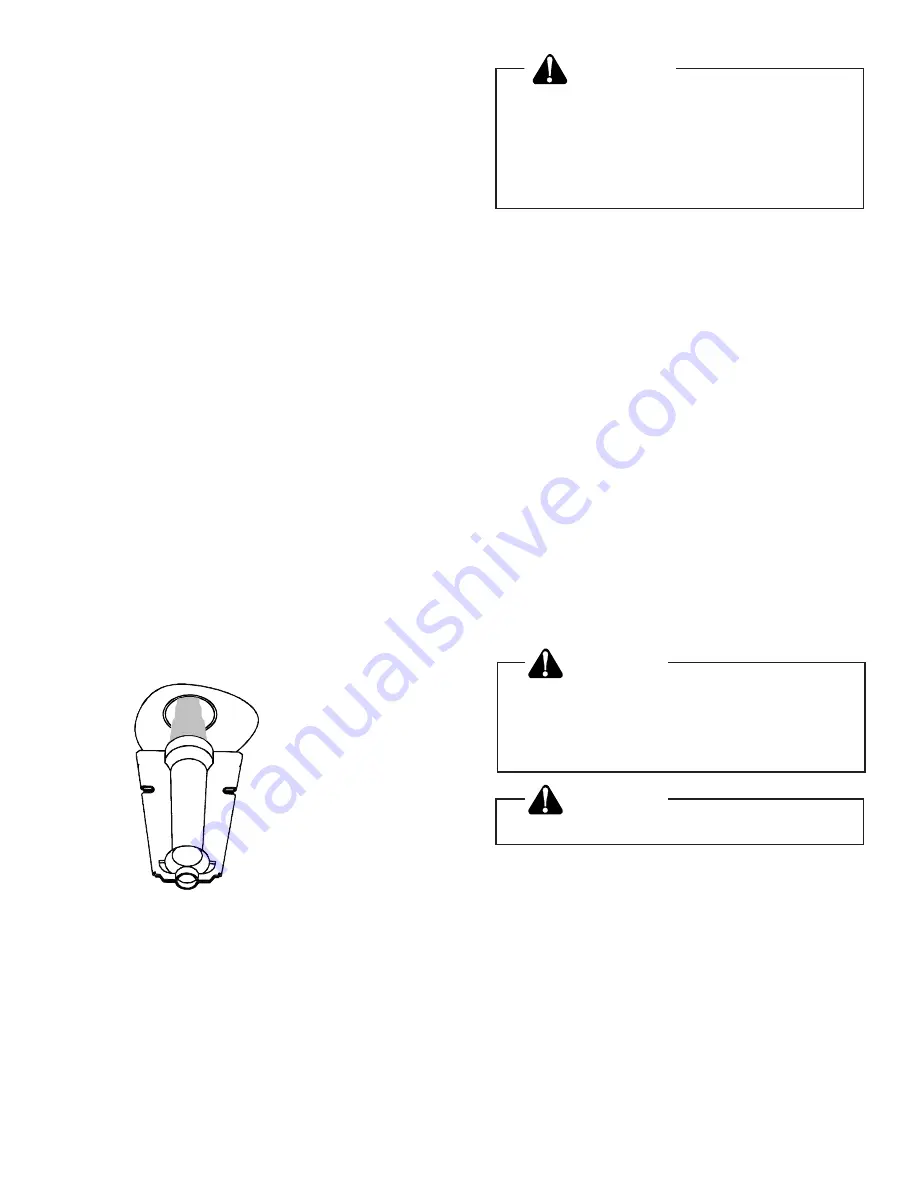
17
Cleaning Flue Passages (Qualified Servicer Only)
1. Shut off electric power and gas supply to the unit.
2. Remove burner assembly by disconnecting the gas
line and removing the manifold brackets from the
partition panel.
3. Remove the flue from the induced draft blower and
the collector box from the partition panel.
4. The primary heat exchanger tubes can be cleaned
using a round wire brush attached to a length of
high grade stainless steel cable, such as drain
cleanout cable. Attach a variable speed reversible
drill to the other end of the spring cable. Slowly
rotate the cable with the drill and insert it into one of
the primary heat exchanger tubes. While reversing
the drill, work the cable in and out several times to
obtain sufficient cleaning. Use a large cable for the
large tube, and then repeat the operation with a
small cable for the smaller tube. Repeat for each
tube.
5. When all heat exchanger tubes have been cleaned,
replace the parts in the reverse order in which they
were removed.
6. To reduce the chances of repeated fouling of the
heat exchanger, perform the steps listed in “Start-
up and Adjustment”.
Main Burner Flame (Qualified Servicer
Only)
Flames should be stable, soft and blue (dust may cause
orange tips but must not be yellow). The flames must
extend directly outward from the burner without curling,
floating or lifting off (Figure 15).
Check the burner flames for:
1. Good adjustment
2. Stable, soft and blue
3. Not curling, floating, or lifting off.
Figure 15
Burner Flame
WARNING
To avoid death or personal injury due to
electrical shock, do not remove any in-
ternal compartment covers or attempt
any adjustment. Contact a qualified ser-
vicer at once if an abnormal flame ap-
pearance should develop.
At least once a year, prior to or during the heating
season, make a visual check of the burner flames.
NOTE: This will involve removing and reinstalling the
heat exchanger door on the unit, which is held by
several screws. If you are uncertain about your ability to
do this, contact a qualified servicer.
If a strong wind is blowing, it may alter the airflow
pattern within the unit enough that an inspection of the
burner flames is not possible.
Cleaning of Burners
1. Shut off electric power and gas supply to the unit.
2. Remove the screws holding the burner retention
bracket in place.
3. Remove the burners.
4. Use a bottle brush to clean burner insert and inside
of the burners.
5. Replace burners and burner retention bracket, in-
spect the burner assembly for proper seating of
burners in retention slots.
6. Reconnect electrical power and gas supply.
CAUTION
Label all wires prior to disconnection
when servicing controls. Wiring errors
can cause improper and dangerous op-
eration.
CAUTION
Verify proper operation after servicing.
For further information on the yearly inspection, consult
the User Manual. It is recommended that a qualified
servicer inspect and service the unit at least once each
year.
Turn the unit on at the thermostat. Wait a few minutes,
since any dislodged dust will alter the normal flame
appearance. Flames should be predominantly blue and
directed into the tubes. They should not be yellow. They
should extend directly outward from the burner ports
without curling downward, floating or lifting off the ports.