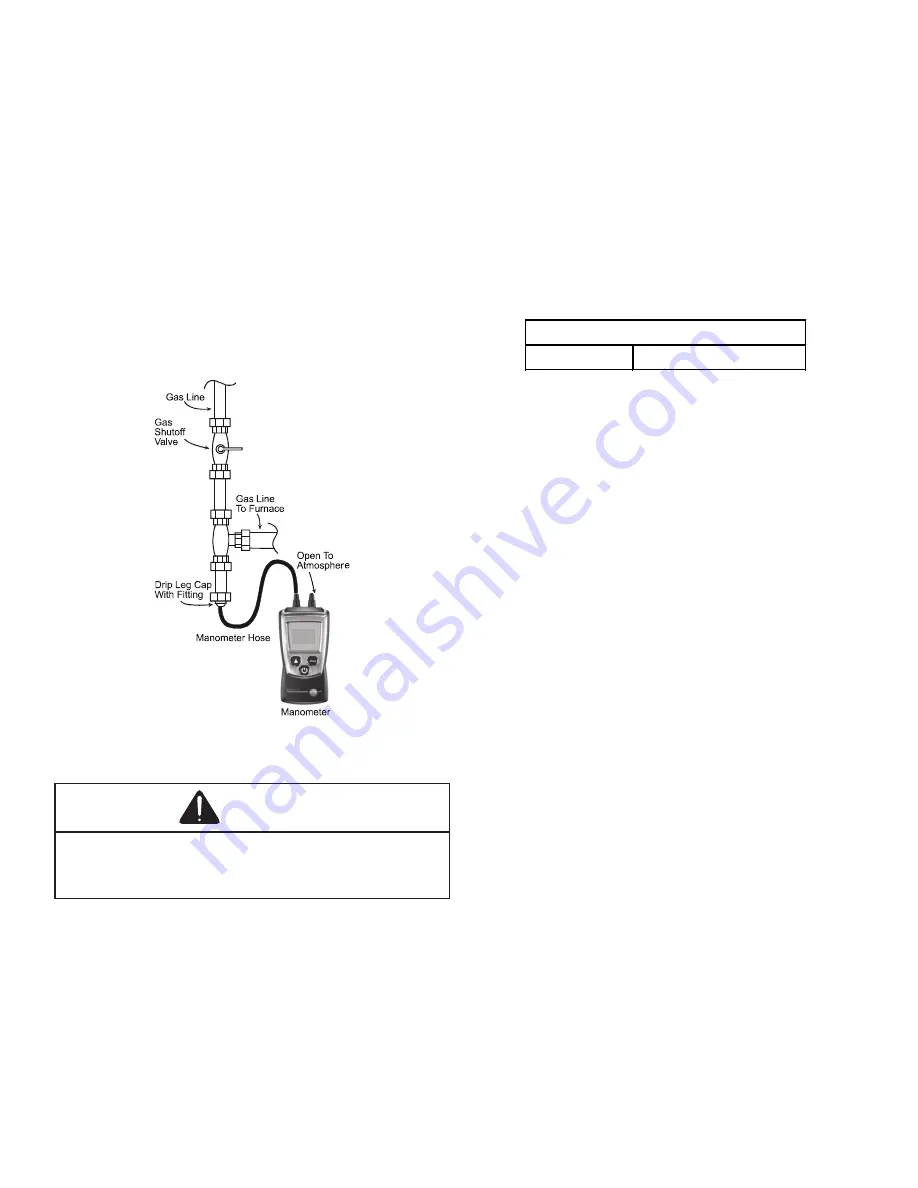
15
8. Remove the manometer hose from the hose barb
fitting or inlet pressure Tap.
9. Replace inlet pressure tap:
a. White-Rodgers Valve:
Turn inlet pressure test screw in to seal pressure
port (clockwise, 7 in-lb minimum).
10. Retest for leaks. If bubbles form, shut down gas and
repair leaks immediately.
11. If there are no leaks, turn ON electrical power and gas
supply to the system.
12. Turn valve switch ON.
NOTE: If measuring gas pressure at the drip leg, a
field-supplied hose barb fitting must be installed
prior to making the hose connection. If using
the inlet pressure Tap on the White-Rodgers gas
valve, then use the 36G/J Valve Pressure Check Kit,
Goodman Part No. 0151K00000S.
.
Measuring Inlet Gas Pressure (Alt. Method)
Gas Manifold Pressure Measurement and
Adjustment
CAUTION
To prevent unreliable operation or equipment damage, the
gas manifold pressure must be as specified on the unit rating
plate. Only minor adjustments should be made by adjusting
the gas valve pressure regulator.
Only small variations in gas pressure should be made by
adjusting the gas valve pressure regulator. The manifold
pressure must be measured with the burners operating.
To measure and adjust the manifold pressure, use the
following procedure.
1.
Turn OFF gas to furnace at the manual gas shutoff
valve external to the furnace.
2. Turn OFF all electrical power to the system.
3. Outlet pressure tap connections:
a. White-Rodgers Valve:
Back outlet pressure test screw (outlet pressure
Tap) out one turn (counterclockwise, not more than
one turn).
4. Connect manometer (or appropriate pressure gauge)
at the gas valve outlet pressure tap. See White-
Rodgers 36J22Y-204 gas valve for location of outlet
pressure tap.
5. Turn ON the gas supply.
6. Turn ON power and close thermostat “R” and “W”
contacts to provide a call for heat.
7. Using a leak detection solution or soap suds, check
for leaks at outlet pressure tap screw (White-Rodgers
valve). Bubbles forming indicate a leak. SHUT OFF
GAS AND REPAIR ALL LEAKS IMMEDIATELY!
8.
Measure the gas manifold pressure with burners firing.
Adjust manifold pressure using the following
Manifold
Gas Pressure
table.
Natural Gas
2.8" - 3.2" w.c.
Manifold Gas Pressure
The Manifold Gas Pressure must be within the range
specified.
9. Remove regulator cover screw from the outlet
pressure regulator and turn screw clockwise to
increase pressure or counterclockwise to decrease
pressure. Replace regulator cover screw.
10. Turn OFF all electrical power and gas supply to the
system.
11. Remove the manometer hose from the hose barb
fitting or outlet pressure tap.
12. Replace outlet pressure tap:
a. White-Rodgers Valve: Turn outlet pressure test
screw in to seal pressure port (clockwise, 7 in-lb
minimum).
14. Turn ON electrical power and gas supply to the
system.
15. Close thermostat contacts to provide a call for heat.
16. Retest for leaks. If bubbles form, SHUT OFF GAS
AND REPAIR ALL LEAKS IMMEDIATELY!
Gas BTU Input (Natural Gas Only) Check
To measure the gas input use a gas meter and proceed as
follows:
1.
Turn off gas supply to all other appliances except the
unit.
2. With the unit operating, time the smallest dial on the
meter for one complete revolution. If this is a 2 cubic
foot dial, divide the seconds by 2; if it is a 1 cubic foot
dial, use the seconds as is. This gives the seconds per
cubic foot of gas being delivered to the unit.
3. INPUT=GAS HTG VALUE x 3600 / SEC. PER CUBIC
FOOT
Example:
Natural gas with a heating value of 1000
BTU per cubic foot and 36 seconds per cubic foot as
determined by
Step 2, then:
Input = 1000 x 3600 / 36 = 100,000 BTU per Hour.