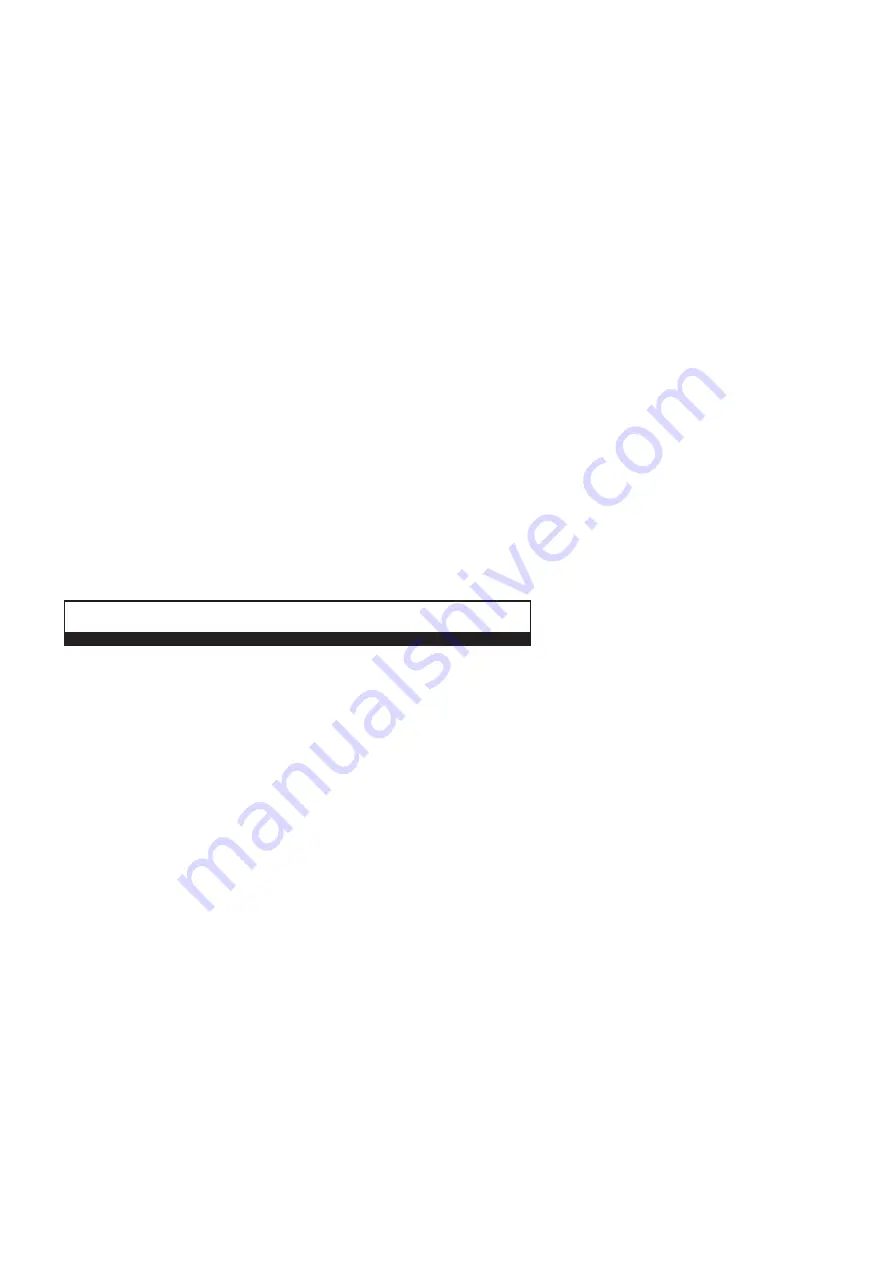
22
Alpha SolarSmart 100 - System Operation/Routine Inspection
Temperature display
The normal display will be as shown in Fig 25 with the collector (S3) and upper cylinder (S1) sensor temperatures shown.
S3 is the top reading and S1 the bottom reading.
Domestic hot water circuit
When a hot tap is opened, cold mains water enters the solar cylinder at the bottom forcing hot water out from the top to go
to the boiler. If it is below 60°C the boiler fires to maintain a 60°C outlet, if the water is above 60°C the boiler does not fire
and the hot water passes through the boiler to the hot outlet. The cylinder pump passes the cool water from the bottom of the
cylinder through the drain back unit heat exchanger and hot water back to the cylinder.
Collector water circuit
The drain back unit pump is controlled by the control box. The collector water is circulated in a closed loop through the
collector where it is heated then passes through the heat exchanger in the drain back unit where the heat is transferred to
the domestic water from the cylinder.
Frost protection
The system will only operate when there is a 10°C differential between the cylinder temperature and the collector
temperature.
Pumps
If the electrical supply is on and the solar system has not operated for 24 hours, the pumps will operate automatically every
24 hours, providing the collector temperature is above 10°C.
7 ROUTINE INSPECTION
To ensure efficient operation of the SolarSmart system, it is recommended that it is inspected and checked (by a competent
person) as necessary at regular intervals.
Warning:
Before removing any covers or working on the system, isolate the electrical supply.
The data badge (serial number) for the cylinder and DBU are located on the lefthand side of the case. See Figs. 10 and 11.
Always carry out electrical system checks, i.e. earth continuity, resistance to earth, short circuit and polarity with a suitable
meter, after any electrical work has been carried out on the system.
Check the operation of the system before and after any servicing or replacement of parts.
7.1 IMPORTANT NOTES FOR ROUTINE INSPECTION
1. Run the system and check the operation.
2. Ensure that all system connections and fittings are sound.
3. Open the Solar cylinder's drain valve (Fig. 1, item 13) until the water from the bottom of the cylinder runs clear.
4. Inspect and clean, if required, the filter in the cold fill manifold assembly. See Fig. 19.
5. Check the operation of the pressure relief valve by turning the head anti-clockwise until it clicks. The click is the valve
lifting off its seat allowing water to escape to the discharge pipe - check that this is happening and that the valve is not
leaking after it has been operated,
6. Check the charge in the domestic hot water expansion vessel and re-pressurise, if necessary. See Fig. 20.
Note:
Only check the expansion vessel charge when the
system
pressure is zero, i.e. drained.
7. Record details of the service in the Service Record at the back of these instructions.
It is recommended that any service work is carried out by a competent person.
Warning:
Before removing any covers or working on the system, isolate the electrical supply.